Какой газ выбрать при лазерной резке стали ?
Чаще всего переработчики сталкиваются с задачами по лазерной резке конструкционных сталей, и это естественно, так как это наиболее массовые материалы для изготовления продукции. К таким материалам из холоднокатанных сталей можно отнести: Ст3, 08пс, различные виды оцинковки, электротехническую сталь, сталь с полимерными покрытиями, а из горячекатаных: 09Г2С или марку S350 применяющуюся в строительстве. Для большинства из этих материалов у производителей станков уже существуют технологические таблицы, они довольно похожи по параметрам и имеют общие подходы. Конструкционные стали можно резать всеми тремя традиционно использующимися газами. Азот и кислород – это классические режимы, но также широко используется в России и сжатый воздух из-за практически нулевой себестоимости. Рассмотрим отдельно каждый режим.
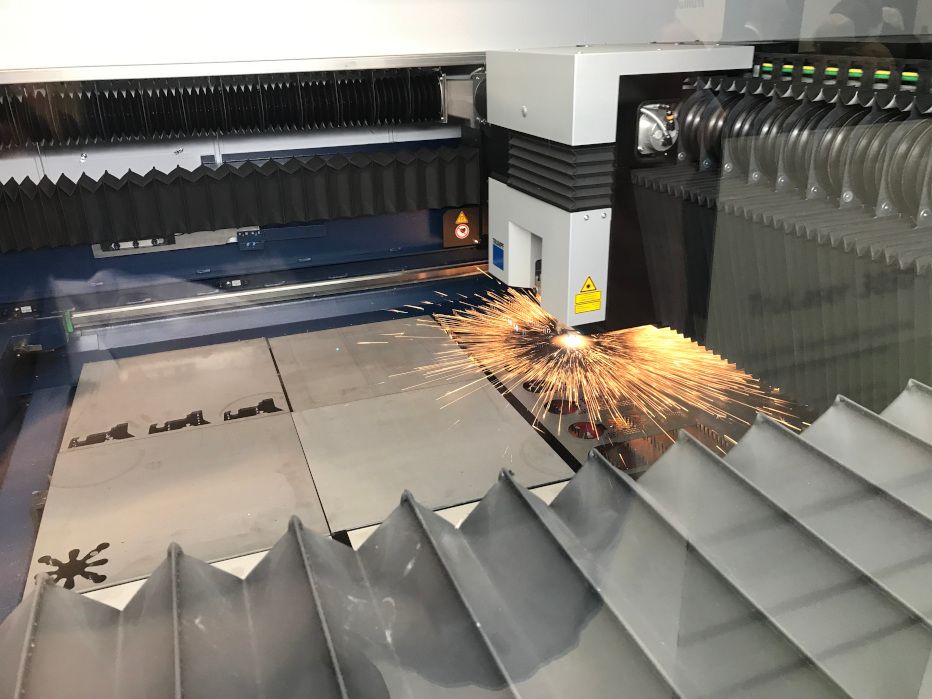
Азот
Позволяет добиваться прекрасных характеристик по скорости на тонком листе (до 3 мм), при этом оставляя чистейшую кромку и близкое к идеальному качество отверстий. Ни о какой последующей мехобработке речи здесь не идет. Лазерный луч плавит металл в точке реза и азот выдувает расплавленную массу без горения. Такой режим может использоваться для выполнения филигранных деталей с мельчайшими элементами. С увеличением мощности источников данный режим позволяет резать и в диапазоне средних толщин (на 12 кВт – до 12 мм), однако, на этих толщинах азот не приносит такой производительности и перестает быть целесообразным. Для выполнения чистого реза без грата комфортный диапазон здесь – до 8 мм. Негативная сторона – высокая стоимость газообразного азота высокой чистоты (99,99%). По этой причине нередко применяются решения по газификации жидкого азота непосредственно на производстве.
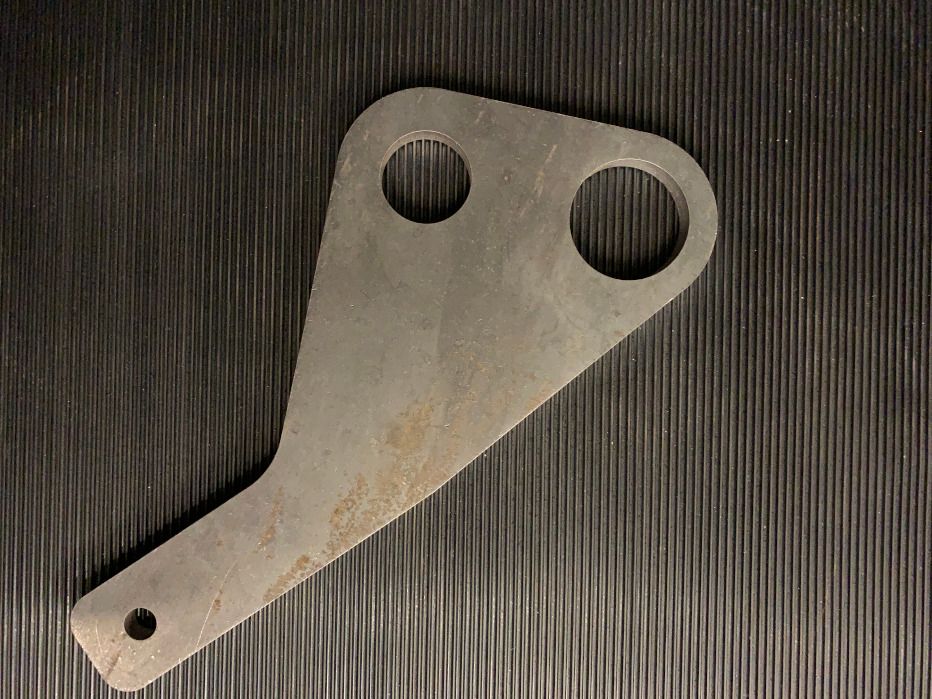
Кислород
В процессе резки данным газом происходит термическое окисление (горение) материала. Им можно резать во всем диапазоне толщин от 0 до 25 (в индивидуальных случаях до 32 мм), но наиболее эффективен он становится от 10 мм, где азот уже не справляется. Также кислородом режут материалы от 5 до 10 мм плохого качества, или если мощность источника не позволяет использовать азот. На тонком листе производительность в разы уступает азоту (на толщине 1 мм примерно в 2,5 – 3 раза медленнее), при таком же хорошем качестве кромки. Этот режим сопровождается большим количеством шлака и нагара. При резке толстого металла возможен грат. При резке горячекатаных металлов от 4 мм из-за высокой температуры может закаляться кромка, что затруднит дальнейшие механические операции в случае их необходимости, например нарезку резьбы в вырезанном лазером отверстии. Но и стоимость кислорода в разы меньше азота.
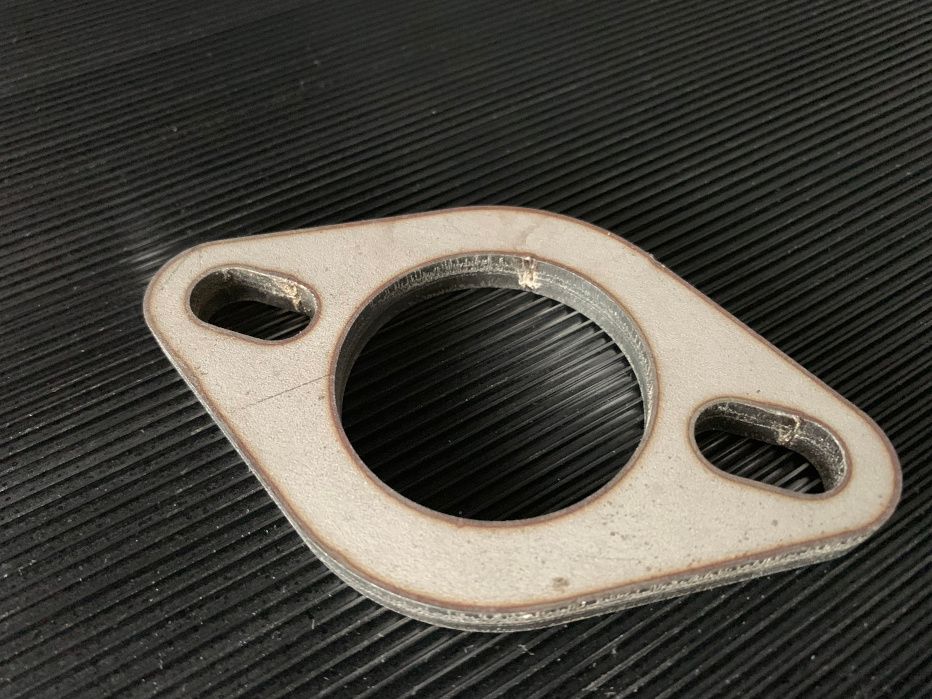
Сжатый воздух
Первый бросающийся в глаза плюс – условная нулевая стоимость. Подавать сжатый воздух как режущий газ можно непосредственно с компрессора. Необходимо проследить, чтобы компрессор был винтовой, а не масляный и были установлены необходимые ступени очистки. Не допускается использование сжатого воздуха из заводских магистралей! Вышеуказанные опасности могут привести к серьезным загрязнениям дорогостоящей оптики режущего блока. При резке этим газом образуется оксидная пленка. Несмотря на то, что воздух состоит в основном из азота, значительная доля кислорода в нем также присутствует (порядка 24%). На этом, пожалуй, минусы заканчиваются. Сжатый воздух на тонком листе до 3 мм дает практически такую же производительность как азот, разница в пользу азота порядка 10%. Эти толщины в основном и считаются диапазоном его применения. По экономическим причинам многие пытаются приспособить параметры резки этим газом вплоть до 10 мм. Консервативные европейские инженеры не жалуют такой подход, но некоторые азиатские производители уже достигли определенных успехов в этом направлении.
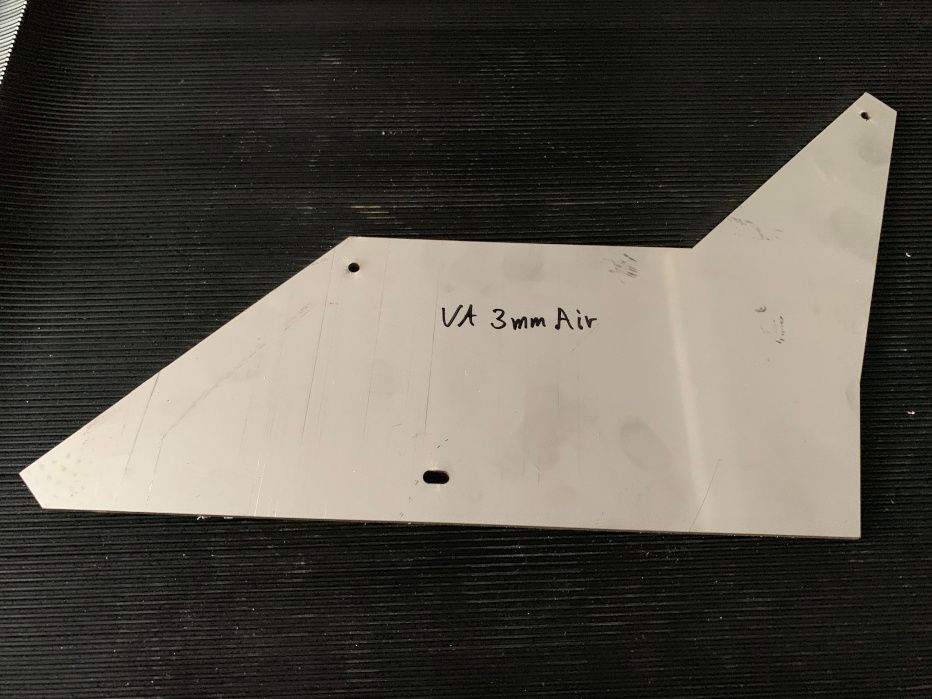
Подобрать оптимальный режим для лазерного раскроя это задача специалистов подрядчика, исходя из технического задания заказчика.