Лазерная резка – это современная технология обработки металлов и других материалов. Она используется на разных производствах и позволяет получать из заготовок или первичного сырья детали нужных размеров, заданной геометрии. Узнайте, как работает резка лазером, где её используют. Выясните преимущества и существующие недостатки.
Суть технологии
Принцип работы, на котором основана лазерная резка, – это влияние сфокусированного, высокомощного луча лазера. Он, действуя целенаправленно на зону обработки, за счёт интенсивной тепловой энергии сначала доводит материал до плавления, затем провоцирует его закипание, потом вызывает полное сгорание или испарение. Такие процессы связаны со значительными энергозатратами, поэтому способ наиболее эффективен по отношению к листовому, относительно тонкому сырью.
Если листы имеют среднюю толщину, то для достижения результатов и оптимизации расхода энергии в участки резки направляется газ. Это может быть аргон, азот, кислород, атмосферный воздух или гелий. Газовое вещество, подаваемое под давлением, обеспечивает интенсивное горение, убирает продукты расплавления, увеличивает производительность, а также охлаждает прилегающие необрабатываемые зоны.
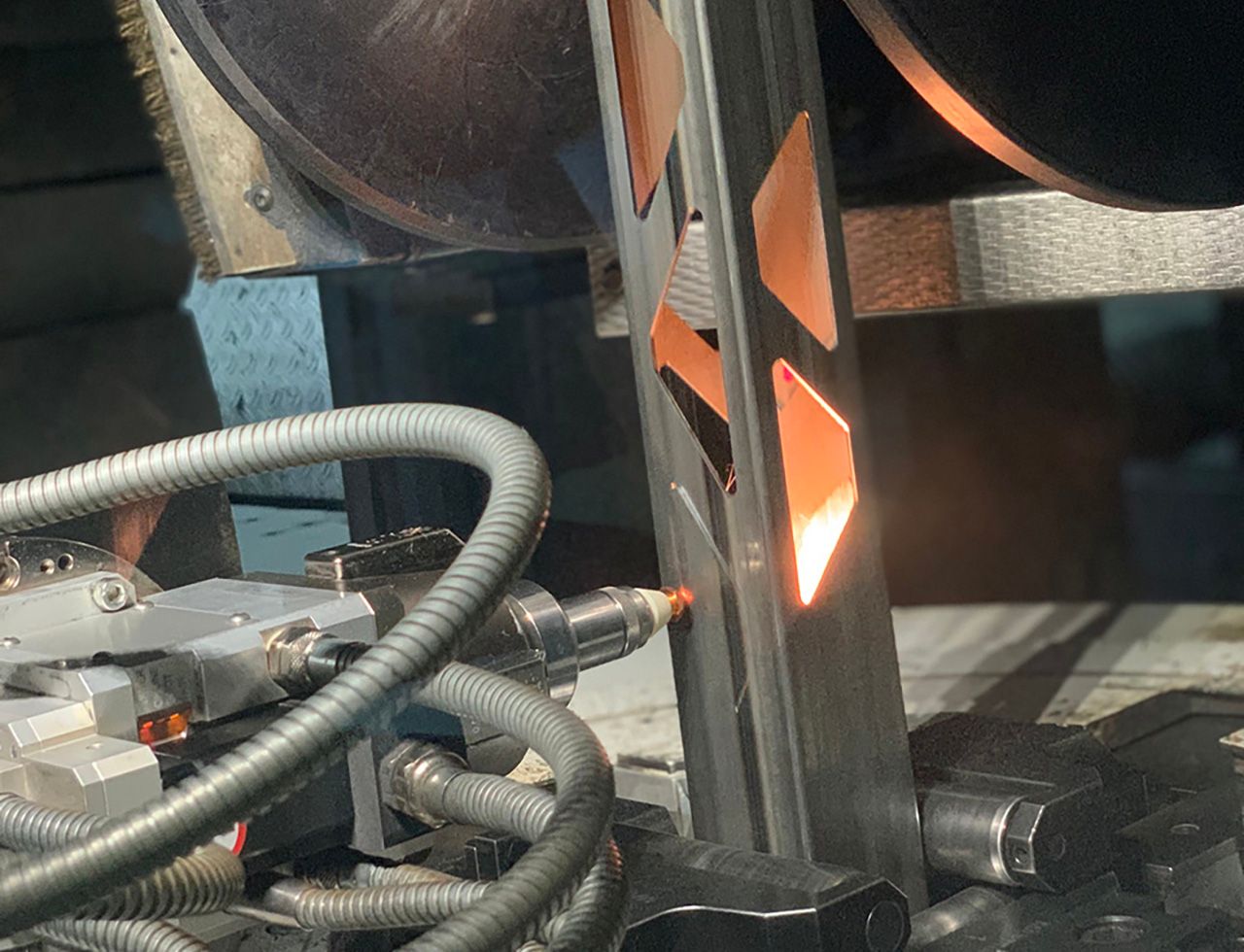
Процесс резки с применением лазера
Технология лазерной резки – энергоёмкий процесс, который предполагает интенсивное разогревание фокусируемым лучом лазера. Такое воздействие вызывает локальное нарушение целостности. Ниже рассмотрим механизмы разделения, за счёт которых происходит локальное разрезание.
Плавление
Способ самый распространённый, подходит не только для металлов, но и для стекла, горных пород, керамики. Лазер интенсивно нагревает нужную зону до температуры, при которой материал расплавляется. При правильно подобранном режиме плавление затрагивает только срез, без повреждений кромок. Разжиженный металл из зоны убирается сжатым газом, направляемым потоком под давлением. Он же исключает деформирование прилегающих зон, охлаждает их.
Газ выбирается с учётом разрезаемого материала. При контактах алюминия и стали с кислородом участки срезов окисляются. Во избежание этого применяют азот. Плавление не подходит для пластиков и отдельных минералов, так как необратимо изменяет их химические свойства, структуру, состав.
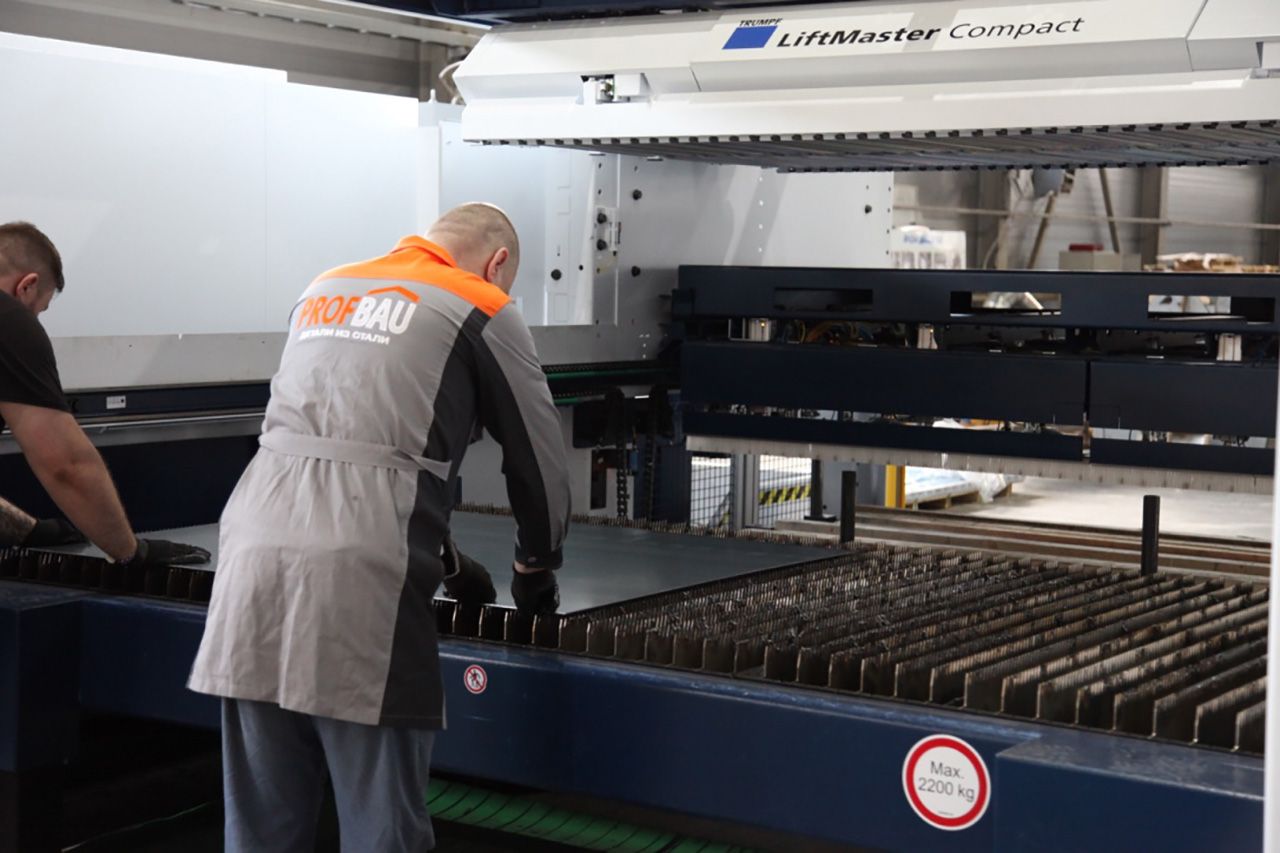
Горение
Оно подойдёт для чёрных металлов, но не применимо к цветным, к высоколегированным сталям. Действие лазера дополняется кислородным потоком, увеличивающим объём тепловой энергии, сокращающим длительность процесса и уменьшающим потребление энергии. Но у некоторых материалов кромки горят, повреждаются. Для устранения дефектов и придания ровности краям среза дополнительно проводят финишную обработку, но она увеличивает стоимость услуги.
Испарение
Методика не самая востребованная, используемая для изделий с тонкими стенками, для листовых заготовок малой толщины. Луч подаётся не струйно и непрерывно, а импульсно, с высокой мощностью. Это позволяет мгновенно нагревать зону до такой температуры, при которой кипение сразу переходит в активное испарение. Образующиеся пары, сконденсированные вещества и отходы убираются воздушной струёй.
Испарение предполагает максимально интенсивное нагревание. Метод энергозатратный. Его применение оправдано тогда, когда другие технологии малоэффективны. Для твёрдых неметаллических тел используют возгонку, называемую сублимацией.
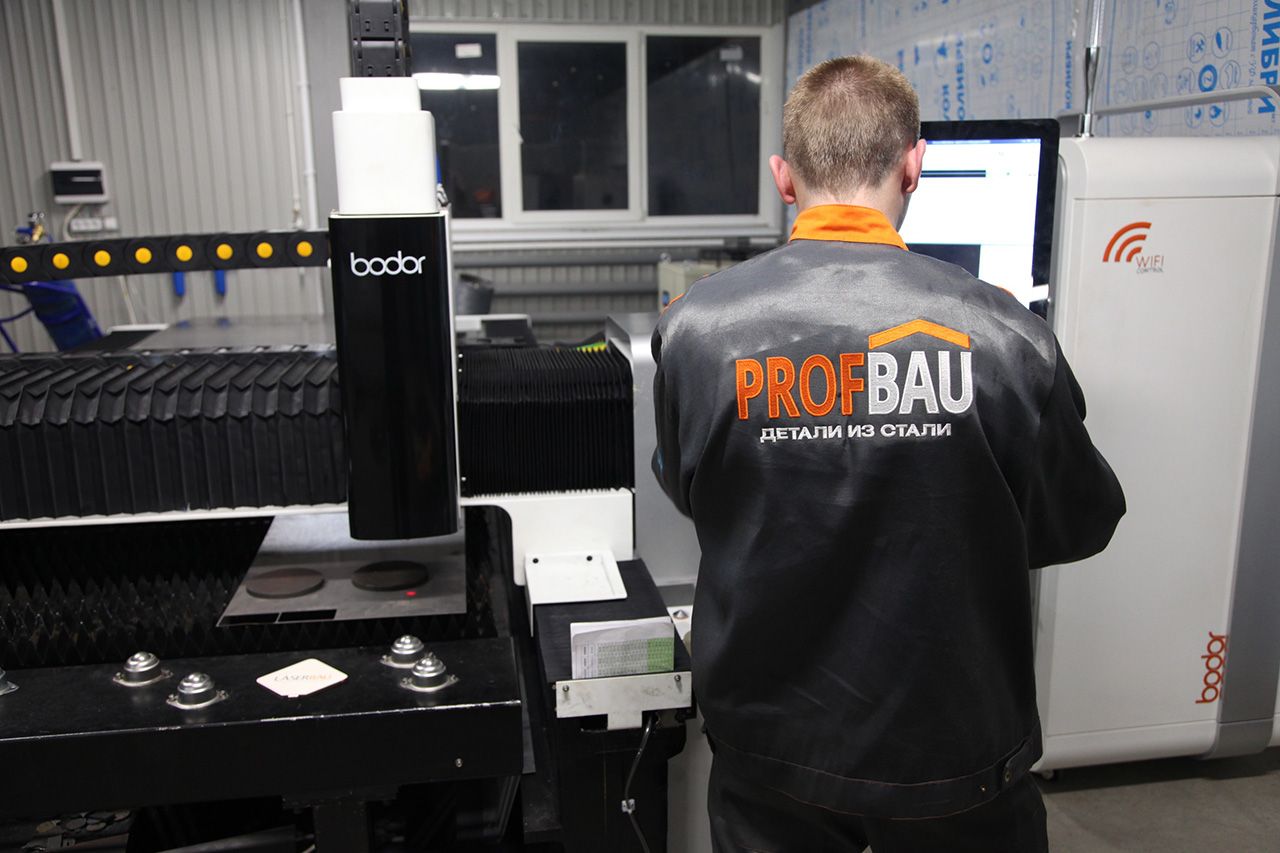
Термохимическое воздействие
Отдельные материалы подвергаются термохимическому воздействию, возникающему из-за:
- Поглощения молекулой фотонов. Она диссоциирует или возбуждается и реагирует с другой частицей практически без изменения температурного значения среды.
- Локального нагревания. При нём создаются частицы, обладающие внутренней собственной энергией, которая превосходит ту, при которой запускаются химические реакции.
- Макроскопического разогревания. При нём тоже возникает химическое действие.
- Радиационных химических превращений. При них формируются радикалы, ионы, а также возбуждённые частицы.
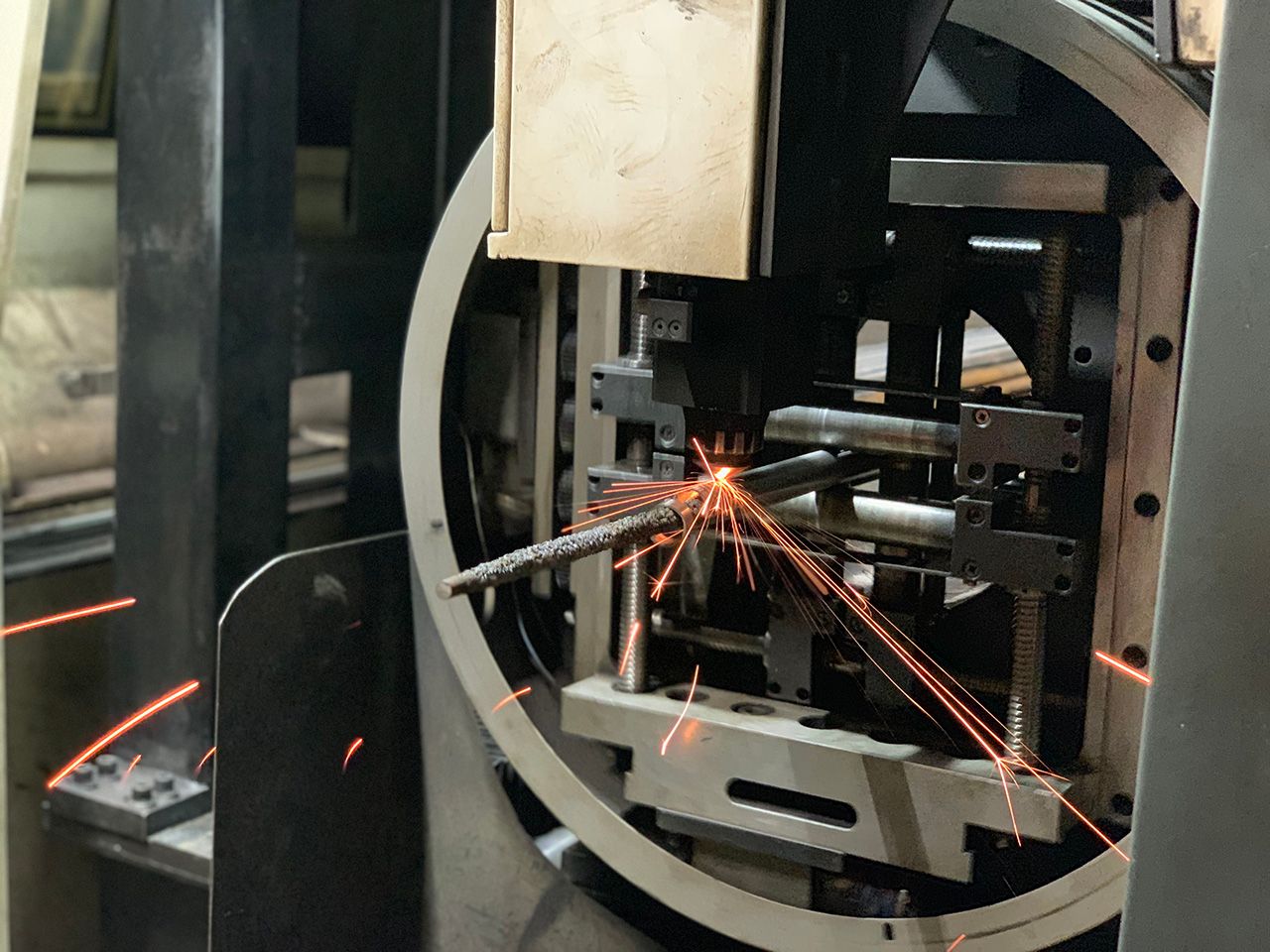
Термораскаливание
Оно подходит для материалов хрупких, с легко разрушаемой структурой. Температурный перепад, возникающий в зоне резки, обусловливает термоупругие напряжения, которые превосходят пределы прочности вещества. В итоге участок растрескивается. Трещины могут распространяться контролируемо посредством корректировки характеристик луча. Расход энергии невысокий.
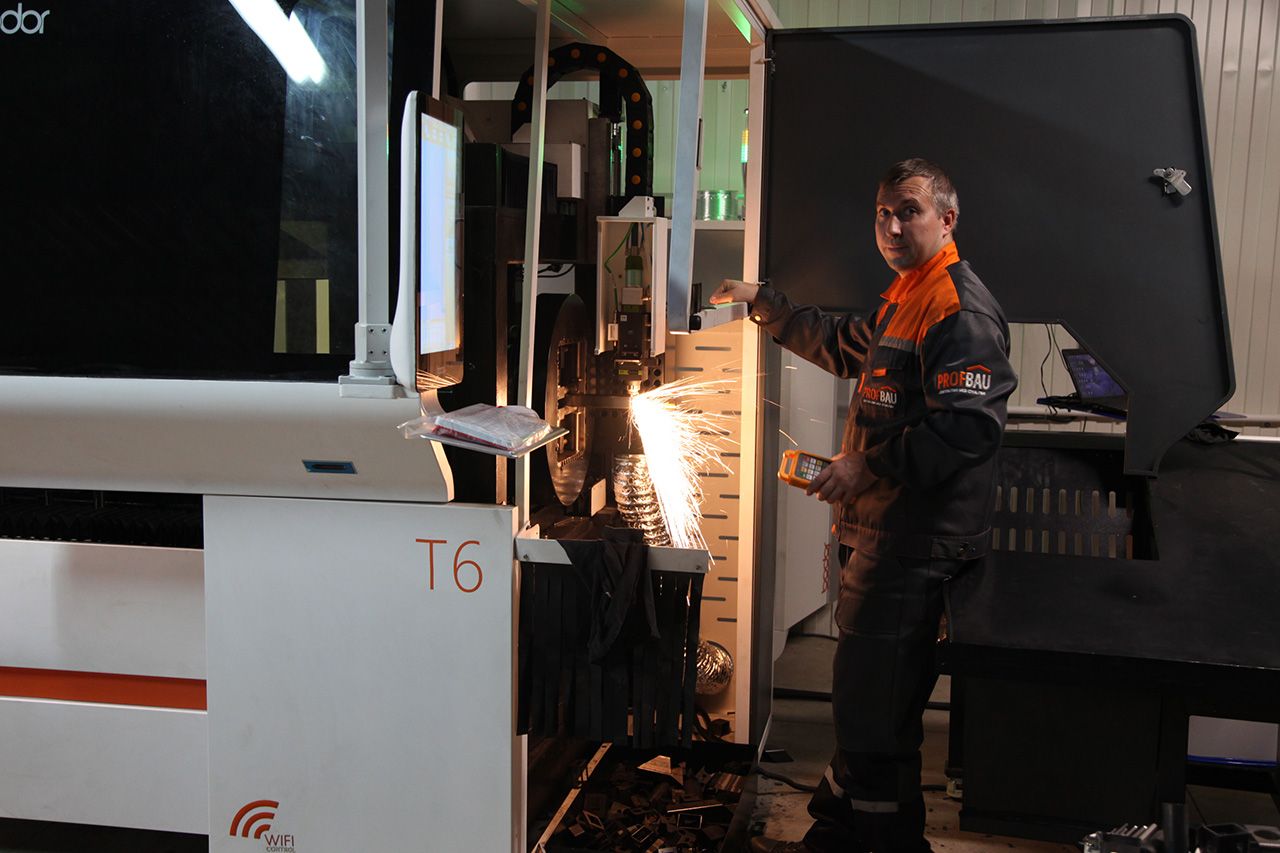
Виды лазерной резки
Технология резки лазером включает несколько типов, различающихся по характеристикам внедряемого газа, показателям давления, интенсивности излучения.
Существуют такие виды обработки:
- Лазерно-кислородная. Рабочую среду образует кислород. При взаимодействии с ним в раскалённых металлах начинаются экзотермические реакции с окислением. Формирующиеся окислы из участка резки выдуваются с помощью подаваемого под напором кислорода.
- Кислородная с поддержкой излучения лазера. Её название – LASOX. Этот метод подходит для толстолистовых сталей. Они предварительно разогреваются до 1000 градусов Цельсия. На нагретый участок подаётся кислородная сверхзвуковая струя, создаваемая под давлением, достигающим 9-10 атмосфер. Кромки получаются ровными, без шероховатостей.
- Испарительная лазерная, она же сублимационная. Излучение пико- или наносекундное, с короткими, но высокоинтенсивными импульсами. Термическое воздействие минимизированное, но КПД низкий.
- С инертными газами. Этот способ подходит для металлов, окисляемых при контактах с кислородом, например, титана, алюминия, нержавейки. Для создания газовой среды используют азот, аргон.
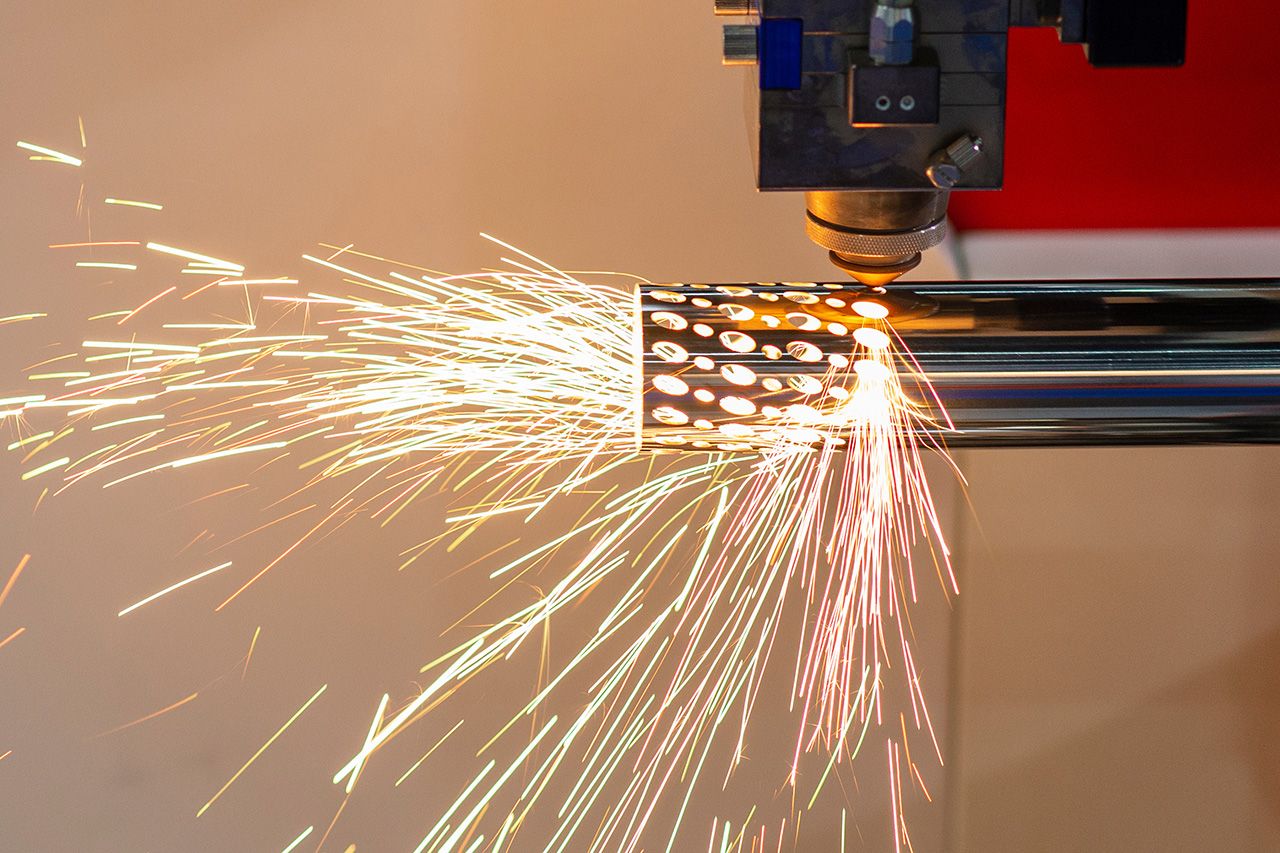
Оборудование
Для лазерной резки металла используют специальные установки, в конструкции которых предусмотрено три составляющих. Первая – активная среда. Это источник, создающий луч лазера. Вторая часть – система накачки. Она обеспечивает условия для запуска излучения. Третий компонент – это оптический резонатор, представляющий собой комплекс зеркал для усиления лазера, его фокусировки в участке обработки.
Рабочие среды бывают разными, и по ним оборудование делится на:
- Твердотельное. В осветительной камере располагается рабочее твёрдое тело – стержень, изготовленный из граната, рубина, неодимового стекла или иного подобного материала. Энергия исходит от газоразрядной высокомощной лампы. В боковых частях стержневого элемента установлены зеркала. Одно отражает, второе является полупрозрачным. Исходящий от рабочего тела лазер отражается много раз, а потом через полупрозрачную зеркальную часть выходит из установки, фокусируясь.
- Газовое. Рабочая среда здесь – углекислый газ, который может комбинироваться с азотом и гелием. Газовый поток проходит через газоразрядную трубку, получает возбуждение от электрических разрядов. Излучение усиливается полупрозрачным и отражающим зеркалами.
- Газодинамическое. Оборудование мощное, в нём оксид углерода выполняет функцию рабочего тела. Но его для достижения нужного эффекта нагревают до высоких температурных показателей: от 726-730 градусов Цельсия до 2700. Возбуждение вещества осуществляется имеющим небольшую мощность вспомогательным лазером. Газ далее достигает сверхзвуковой скорости, через особое суженное в центре сопло прокачивается с резким расширением и охлаждением. Возбуждённые атомы трансформируются в обычные, создавая излучение.
Лазерная обработка выполняется на автоматизированном оборудовании, оснащаемым числовым программным управлением. Благодаря ЧПУ достигается точность, соответствие заданным характеристикам деталей. Исключается негативное влияние человеческого фактора, сокращаются риски ошибок, возникновения брака.
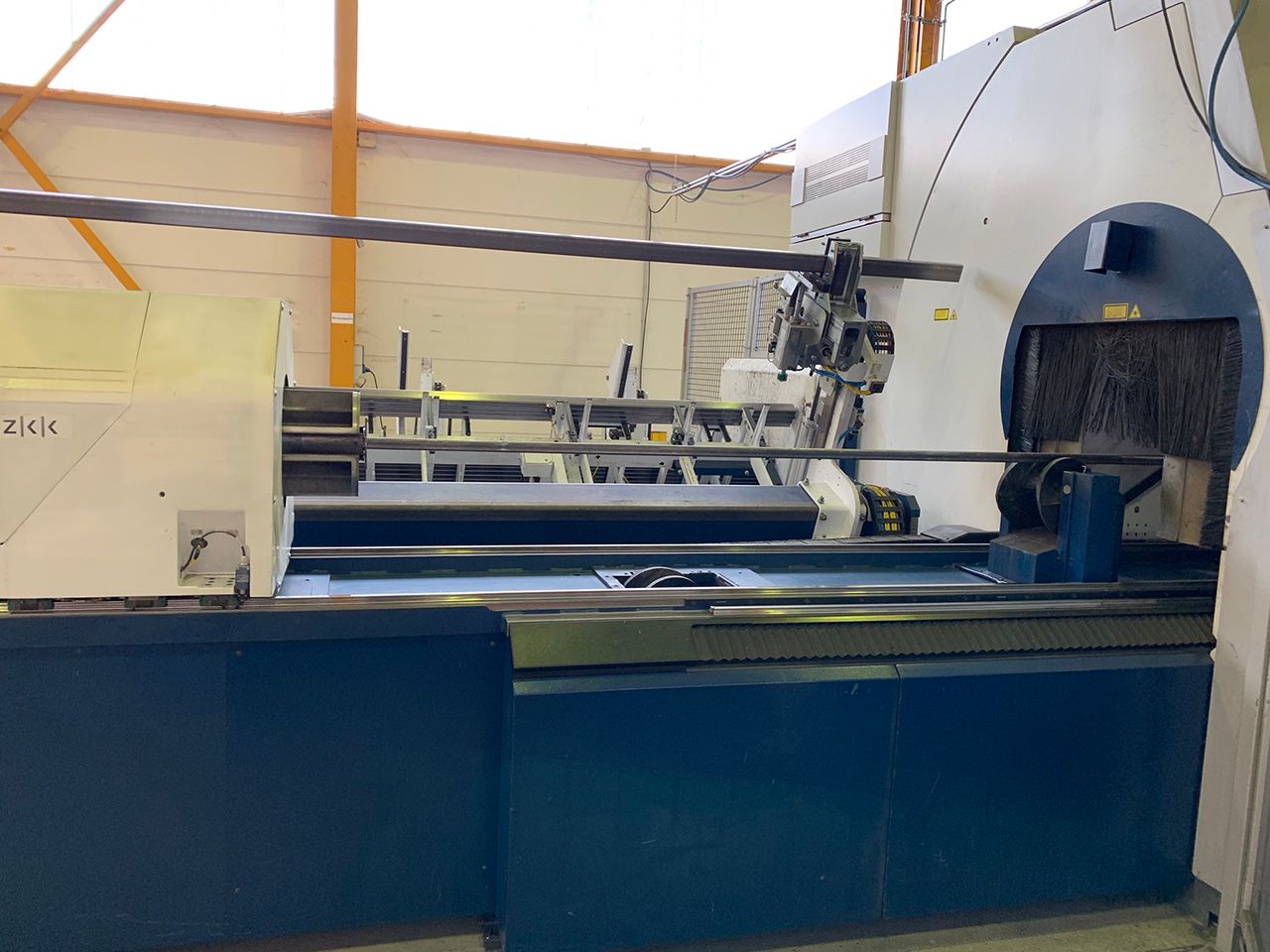
Области применения
Резка лазером подходит для разных металлов, а также других материалов: стекла, акрила, полимера, пластиков, дерева, картона, резины. Сфера применения охватывает такие области:
- автомобилестроение – изготовление деталей, корпусов;
- машиностроение – производство станков, сложного оборудования;
- судостроение – выпуск морских, речных судов;
- мебельные производства – изготовление корпусной мебели: столешниц, шкафов, кроватей, стеллажей из дерева, металла, ДСП, пластика;
- авиационная отрасль – подготовка элементов конструкции вертолётов, самолётов;
- оборонная промышленность – выпуск военной техники;
- рекламная сфера – производство штендеров, букв для растяжек и витрин, световых коробов, визиток, макетов, ростовых фигур;
- лёгкая промышленность, например, изготовление обуви, прочих товаров массового потребления;
- подготовка печатей, трафаретов, форм, штампов;
- сувенирная продукция, такая как брелоки, календари, магниты, рамки для фотографий;
- декор интерьеров – гравировка, фигурная резка по металлам или другим материалам;
- выпуск сельскохозяйственной и спецтехники;
- приборостроение, электротехника, электроника;
- производство медицинского оборудования, диагностического, другого высокоточного.
С помощью лазерной резки можно создавать изделия любых форм, в том числе со сложной геометрией – тонкими перемычками, фигурными контурами, углами, срезами. Также технология позволяет раскраивать листы, формировать пазы и выемки, отверстия.
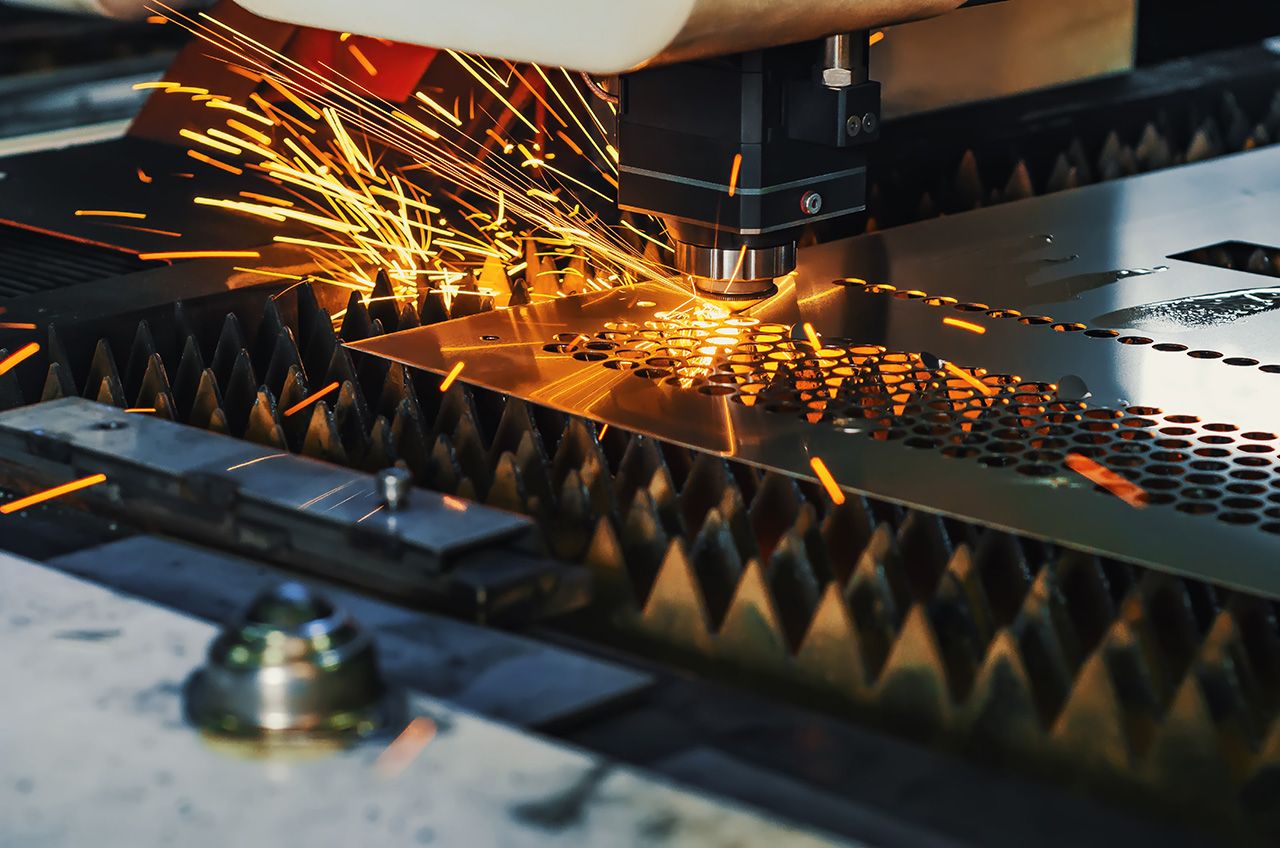
Преимущества, недостатки
Технология имеет плюсы и минусы. Проанализируем её преимущества:
- Универсальность. Можно резать сталь, латунь, чугун, медь, железо, алюминий, титан, другие материалы, включая хрупкие.
- Возможность создания сложных деталей. Можно сделать не только прямой стандартный срез, но и трёхмерный, фигурный, под углом. С помощью резки лазером получают крупные и мелкие изделия практически любой конфигурации.
- Резка разных заготовок: листов, труб, профилей, болванок, нетолстых плит.
- Экономное расходование материалов. Луч фокусируется, поэтому воздействие локальное, без повреждений прилегающих зон. Также расходы снижаются благодаря нанесению разметок на заготовки.
- Возможность успешно обрабатывать материалы разных толщин – от 0,2 до 20-40 миллиметров, в зависимости от вида.
- Узкий и ровный рез, получаемый благодаря точной фокусировке луча малого диаметра.
- Отсутствие пыли, окалины, вредных испарений при операциях. Процесс безопасен.
- Ровные края срезов без дефектов типа сколов, зазубрин, грата, наплавов.
- Максимальная автоматизация процессов с высокой точностью настроек, минимальными рисками ошибок и брака.
- Отсутствие повреждений, полное сохранение исходной структуры. Нагревание локальное, без термического воздействия на прилегающие участки.
- Отличная производительность. За минуту возможно нарезать до 25 метров в среднем. При малой толщине листов и высокой мощности станка производительность достигает 100-150 м/мин.
- Высокая точность. Возможная погрешность обычно не превышает 0,1 мм.
- Минимальные требования к нарезаемым материалам: не превышающая предельное значение толщина, отсутствие коррозии, окисления, загрязнений.
- Средняя цена услуг, рассчитываемая индивидуально с учётом используемой технологии, требований клиента, характеристик металла, типа и толщины заготовок, а также заданных конечных характеристик деталей.
Есть некоторые недостатки:
- Энергоёмкость. Расход энергии довольно большой. Чем толще заготовка, тем энергопотребление выше.
- Дорогостоящие станки, которыми владеют не все специализирующиеся на металлообработке компании. Из-за их высокой стоимости увеличивается и цена работ.
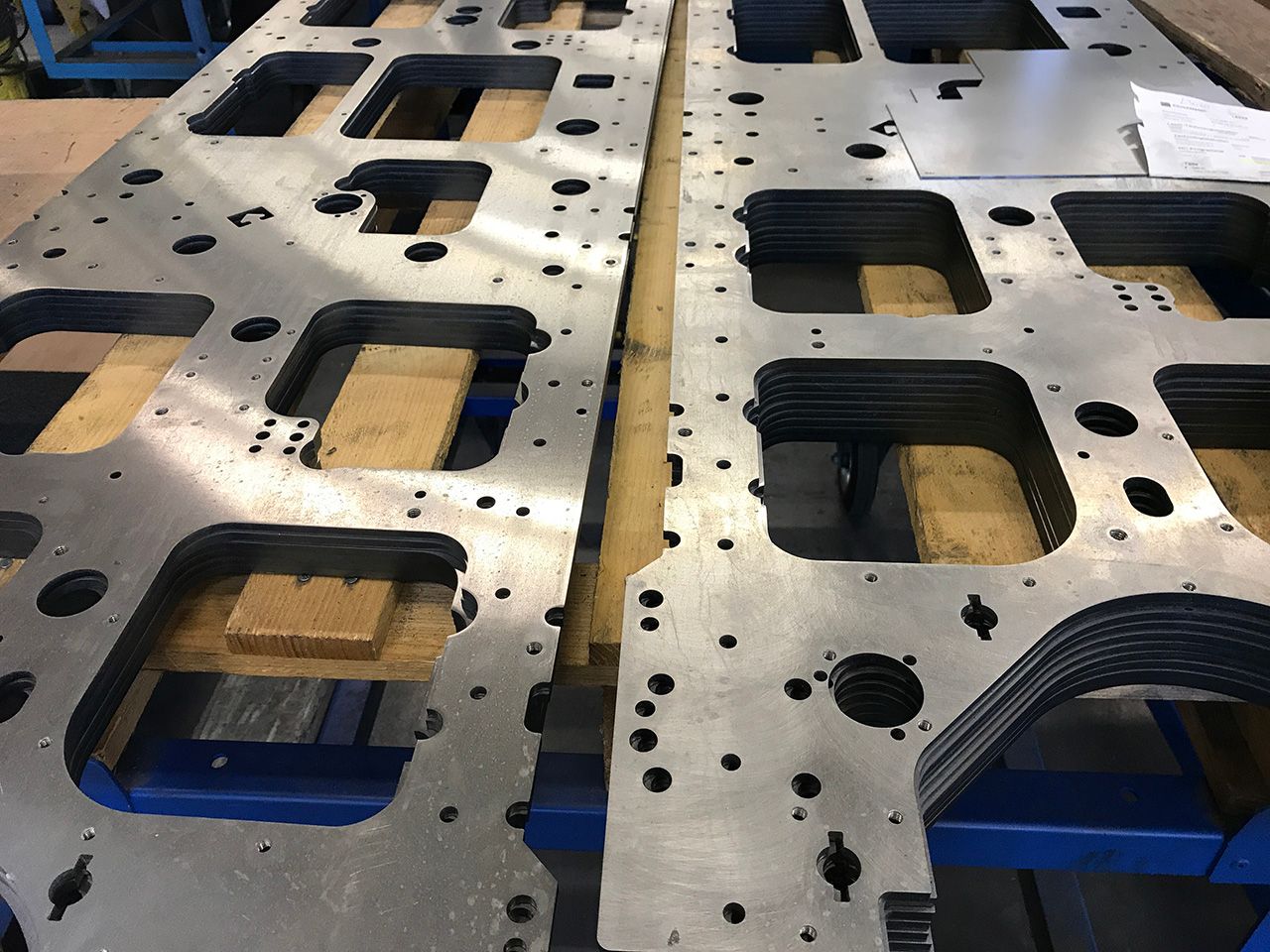
Параметры качества резки лазером
Использование лазера делает резку высокоточной, эффективной. На итоговый результат и качество готовых изделий влияют такие факторы:
- вид нарезаемого металла либо сплава, а также его марка;
- характеристики используемого оборудования: мощность установленного в нём источника энергии, диаметр фокусируемого на металле луча; количество и схема размещения линз и зеркал;
- исходного состояния материала: его чистоты, наличия поверхностных загрязнений, примесей и посторонних вкраплений, следов коррозии;
- применяемый совместно с лазером газ;
- желаемая чистота реза;
- толщина нарезаемых заготовок;
- скорость, с которой рабочая головка двигается по обрабатываемой поверхности;
- состояние, исправность лазерного станка;
- наличие, точность чертежей, технического задания;
- точность настроек используемой установки, например, фокусное расстояние;
- конечные характеристики деталей.
Некоторые показатели нормируются, другие определяются с учётом исходных параметров, ожидаемых результатов, энергозатрат, скорости работ. Например, когда вместо кислорода используют атмосферный воздух, станок демонстрирует вдвое меньшую производительность.
При некорректной фокусировке, неподходящей скорости, недостаточной или чрезмерной мощности, неверно выбранном газе или других ошибках качество снижается. Если учесть все факторы, погрешность составит всего 0,1 мм, а срезы получатся гладкими, ровными.
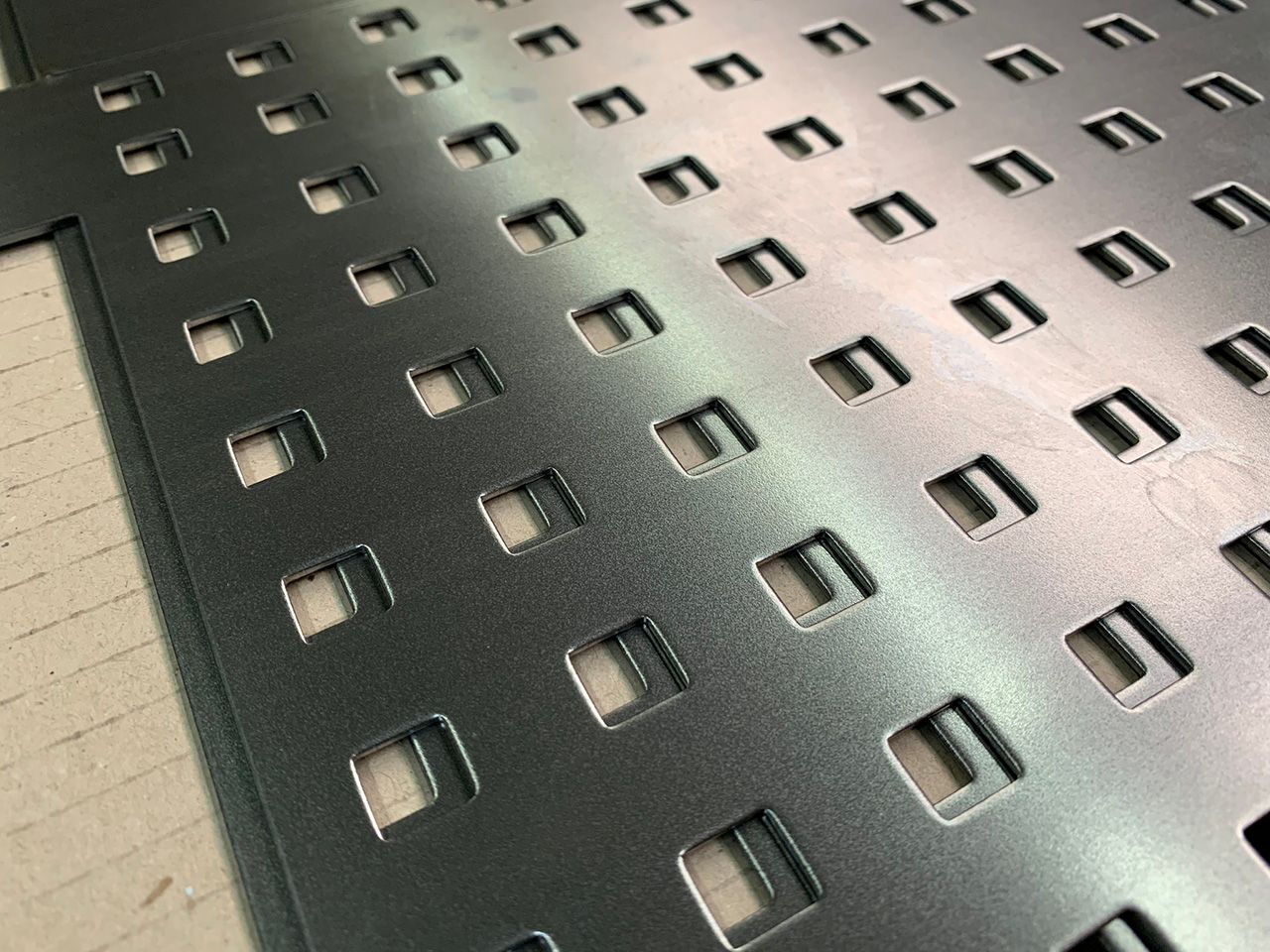
Чем отличается лазерная резка от плазменной
Основное отличие – это источник энергии. При лазерной технологии это фокусируемый, обладающий высокой мощностью луч лазера. При плазменном способе используют ионизированный газ, который подаётся с большой скоростью, локально (струёй). Плазма подходит для металлов значительной толщины, но не применима к неметаллам, например, пластику, дереву, стеклу.
Качество лазерной резки выше, кромки не требуют финишной обработки. При плазменном способе вероятно появление грата, окалины. Края нужно дополнительно шлифовать. Кроме того, точность лазера превосходит показатели плазменной струи. Но при толщине заготовительного сырья больше 6-7 мм скорость плазмы выше.
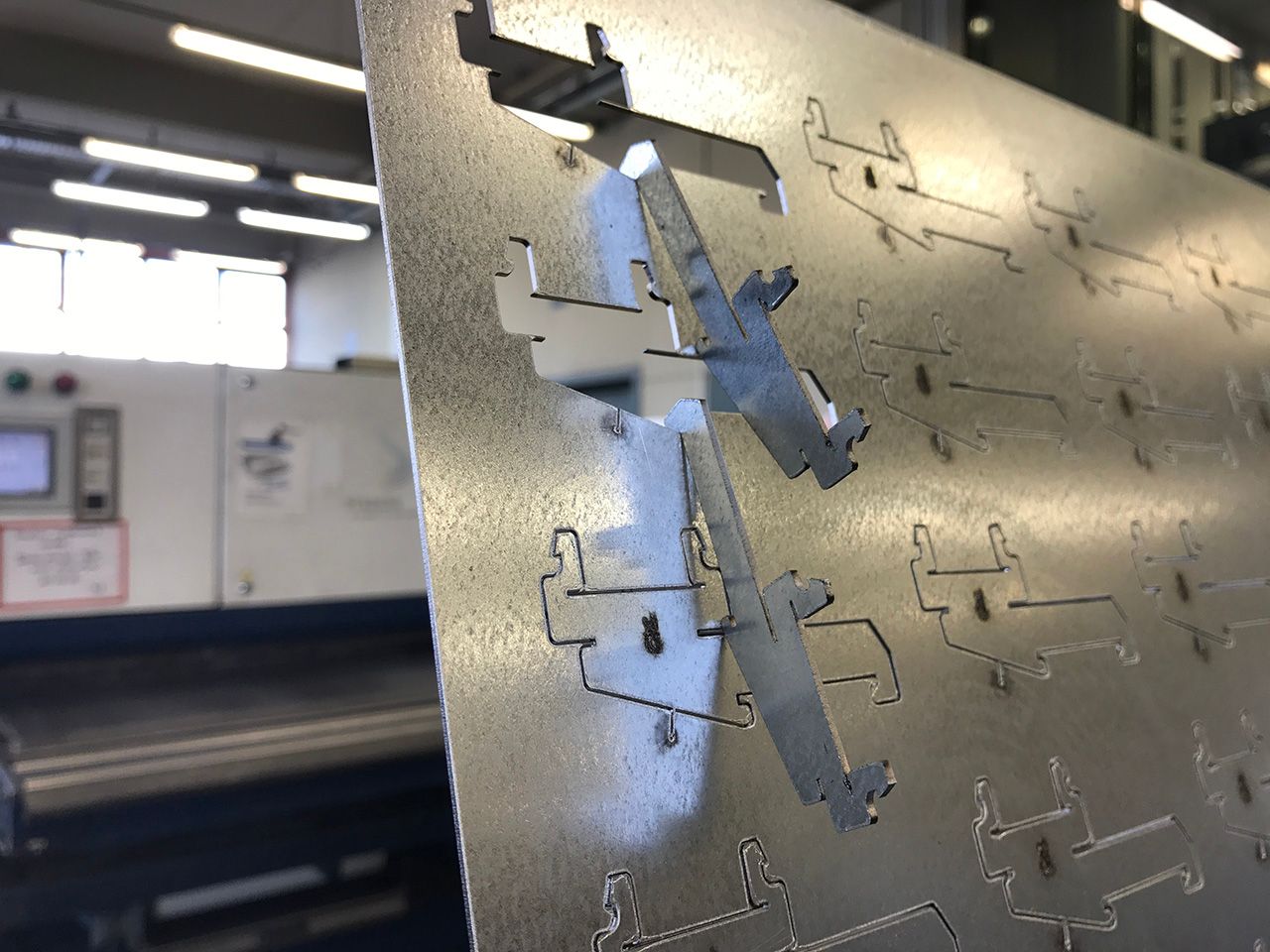
Особенности использования для разных металлов
Разные металлы имеют особенности, которые нужно учитывать при подборе подходящей технологии. Важный параметр – мощность. Например, для цветных металлов и сплавов подходят значения не ниже 1 кВт. А чёрные можно резать при мощности 500-600 Вт.
Обычно применяется газолазерный способ, и выбор газа тоже влияет на качество. Так, для нержавеющей, высоколегированной, оцинкованной стали подойдёт азот, давление подачи струи которого может достигать 20 атм. Так как эти сплавы очень прочны, иногда резка лазером становится единственной действенной методикой.
Для цветных металлов применяют установки с высокой мощностью, обычно твердотельные. Алюминий, латунь, алюминиевые сплавы совместимы с разными инертными газами, к примеру, гелием, аргоном, азотом. Их оптимальное давление – десять атмосфер.
Есть ограничения для максимальной толщины (минимальная составляет 0,2 мм):
- для алюминия – не больше 25 мм;
- для меди – максимум 16 мм;
- для сталей – до максимальных 30 мм (до 40 для нержавейки);
- для латуни – не более 12,5 миллиметров.
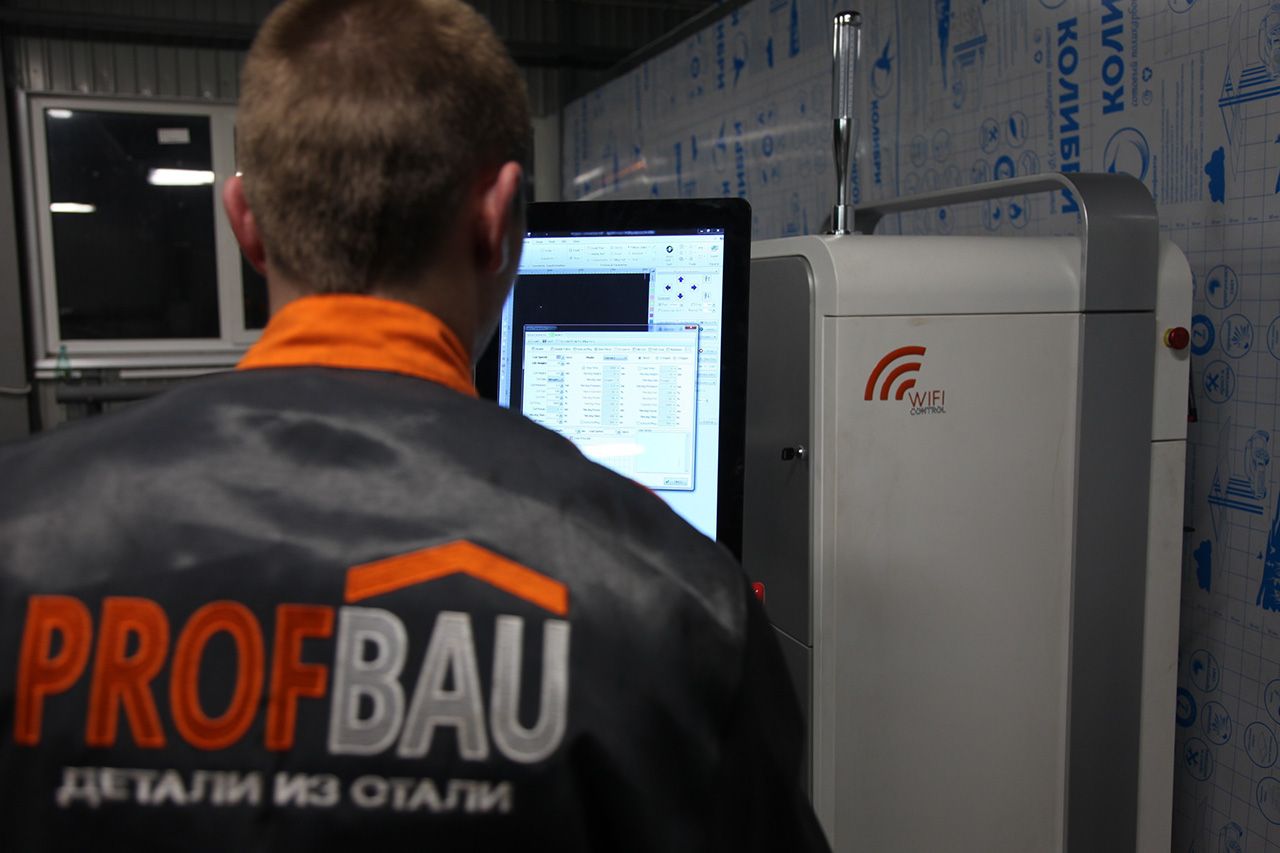
Заключение
Лазерная резка позволяет получать соответствующие чертежам и требованиям металлические изделия. Но чтобы их качество было высоким, важно доверить процесс профессионалам. В предприятии полного цикла Profbau работают опытные мастера, владеющие всеми применяемыми технологиями и знающие особенности разных материалов.
Мы используем высокоточное современное оборудование, со 100% результатом обрабатываем практически любые металлы. Изготавливаем штучные образцы, крупные и мелкие партии деталей. Добиваемся максимального соответствия конечных размеров и геометрии изделий заданным характеристикам. Оказываем услуги по честным ценам, с соблюдением сроков.