Резьба – формируемые на конических и цилиндрических телах вращения впадины и выступы, чередующиеся друг с другом и располагающиеся по винтовой линии. Это элементы зацепления в зубчато-винтовых и винтовых передачах, а также главные составляющие резьбовых соединений.
Для нарезания резьбы используют различные инструменты. От выбора технологии зависят результаты, а также соответствие характеристик изделий заданным параметрам, действующим международным или государственным стандартам. В этой статье расскажем подробно, как нарезается резьба на токарном станке.
Типы резьбы
Основные виды:
- Метрическая. Часто встречается в метизах, измеряется в миллиметрах, имеет острую либо скошенную вершину и треугольный профиль, а также грани с углом наклона, равным 60 градусам. Подвиды – цилиндрическая, коническая. Для последней характерны боковые поверхности с незначительным наклоном для минимальных рисков самопроизвольных раскручиваний, для надёжности и лучшей герметичности соединений. Цилиндрическая отличается гранями, сходящимися под 60-градусным острым углом. Радиус впадины увеличен, что усиливает жаростойкость, усталостные характеристики.
- Дюймовая. Для измерений используются британские стандарты с целыми или дробными дюймами. Гребни, по сравнению с метрической модификацией, удлинены, а грани сходятся с углом 55 градусов. Дюймовые резьбы применяют для производства крепёжных деталей, для разъёмных соединений частей трубных систем. Выделяют два подвида – конический и цилиндрический. Их отличие – форма поверхности, на которой нарезаются впадины и выступы. В первом случае это конус, а во втором – цилиндр.
- Питчевая. Передаёт движения (обычно в зубчатых, червячных передачах), измеряется в питчах. Одна такая условная единица соответствует 3,14 дм. Витки выполняются с эвольвентной, трапециевидной формой или в виде архимедовой спирали. Они наклоняются под сорокаградусным углом.
- Упорная. Профиль трапециевидный. Его первая сторона находится под небольшим 3-градусным углом. А вторая наклонена на 30 градусов. Соединения благодаря этой конструкции выдерживают осевые большие нагрузки.
- Круглая. Это вариант со скруглённым, плавным профилем, выступы и углубления которого состоят из сегментов окружностей. Данные соединения часто используют в запорной арматуре.
- Трапециевидная. Конфигурация профиля – трапеция, усиливающая стойкость к критическим нагрузкам, сокращающая обусловленные трением потери. Есть способность к самоторможению для лучшей фиксации.
- Трубная. Используется в трубопроводах, нарезается на концевых стыкуемых зонах труб разных инженерных систем (водо-, тепло-, газоснабжения). Есть два подвида: цилиндрический, конический. Последний используют в деталях с коническим краевым сужением для крепления с качественным уплотнением. Боковые кромки по форме конусообразные, с углами вершин, равными 55 градусам. Цилиндрические трубные резьбы наносятся на стандартные трубы с продольным сечением в виде цилиндра.
Есть классификация по расположению чередующихся впадин и выступов: снаружи детали либо внутри неё. По такому признаку есть два вида: наружный и внутренний. По форме продольных сечений изделий выделяют цилиндрическую и коническую разновидности. Классификация по профилю предполагает несколько типов: прямоугольные, трапецеидальные, треугольные, круглые.
По функционалу резьба бывает преобразующей вращательные движения в перемещения по возвратно-поступательной траектории, ходовой, а также крепёжной, используемой для формирования разъёмных соединений в разных конструкциях. По направлению выделяют левые резьбовые поверхности и правые. По количеству заходов есть два варианта: однозаходный или более сложный многозаходный.
К главным параметрам относят её шаг, вершину и угол профиля, сам профиль, а также внутренний, средний и наружный диаметры.
Нарезание резьбы с помощью токарного станка
Резьбы нарезают на оборудовании, оснащаемом режущими элементами с заострённой концевой частью – вершиной. Технологическая операция нарезки может осуществляться на токарно-винторезномстанке или на универсальном многофункциональном токарном.
Заготовка фиксируется в устройстве, во время его функционирования с определённой скоростью вращается вокруг собственной оси. Сюда подаётся рабочий инструмент. Он со стабильной заданной скоростью движется по направлению вдоль оси крутящегося изделия и своей заострённой вершиной формирует винтовую углублённую линию.
На наклон, с которым винтовое углубление размещена относительно плоскости, расположенной перпендикулярно к центральной оси подвергающейся обработке детали, влияет соотношение скорости кручения шпинделя (вала, на котором закрепляется заготовка) к скорости движения рабочей части станка. Это угол подъёма или увеличения нарезаемой винтовой линии. Он определяется двумя параметрами:
- подачей оснастки, движущейся в продольном направлении относительно оси детали;
- частотой, с которой обрабатываемая деталь вращается.
Другой параметр, свойственный винтовой линии, – это шаг, определяющий расстояние между находящимися рядом витками и измеряемый по оси. Поверхности, где формируется рельеф, бывают коническими, цилиндрическими. Винтовая линия может быть единственной. Тогда резьбовая поверхность называется однозаходной. Другой вариант – многозаходный с несколькими винтовыми нитями. Они относительно друг друга находятся с равными удалениями.
Контур сечения в перемещаемой через ось вымышленной плоскости, называемый профилем, бывает трапецеидальным, круглым, прямоугольным, упорным, треугольным. Такой параметр сильно влияет на назначение, на эксплуатационные характеристики.
Для нарезания внутренней/наружной резьбы, левой или правой пользуются токарными станками, дополняемыми разной оснасткой. Это режущие инструменты типа резцов, метчиков, резьбонарезных головок, плашек. Ниже рассмотрим подробно все технологии нарезки.

Резцы
Нарезка резцами на данный момент – востребованная технология. Такие инструменты выполняются из быстрорежущих сталей и должны отвечать требованиям, которые регламентируются действующими ГОСТ. По конструкции все резцы делятся на стержневые, призматические и дисковые, называемые также круглыми.
Винтовые наружные канавки формируются резцами прямой конфигурации или с отгибом. А внутренние создаются изогнутыми или прямыми инструментами, закрепляемыми в станках с предусмотренными оправками. Вершина резца полностью соответствует достигаемому профилю резьбы.
Нарезая канавки этим методом, нужно учитывать его особенности:
- Передний угол режущего инструмента находится в широком диапазоне от 0 до 25°, подбирается по свойствам обрабатываемого металла. Если нарезание осуществляется на обычной стали, то угол равен нулю. Если обрабатывается высоколегированная термостойкая сталь, то величина переднего угла находится в диапазоне 5-10 градусов. По мере увеличения вязкости материала угол растёт. И, наоборот, чем металл более хрупкий и твёрдый, тем ниже значение.
- Боковые задние углы подбираются так, чтобы поверхности режущего инструмента не тёрлись о формируемые канавки. Они обычно идентичные с двух сторон резца. При значении угла подъёма меньше 4° боковой задний угол имеет величину от 3 до 5 градусов. При показателе более 4 градусов задний боковой угол подбирается в пределах 6-8°.
- Формирующая винтовую углублённую линию вершина резца по форме полностью идентична профилю создаваемой резьбы.
- Если резьба внутренняя, то для её нарезки сначала подготавливают отверстие способом рассверливания или расточки.
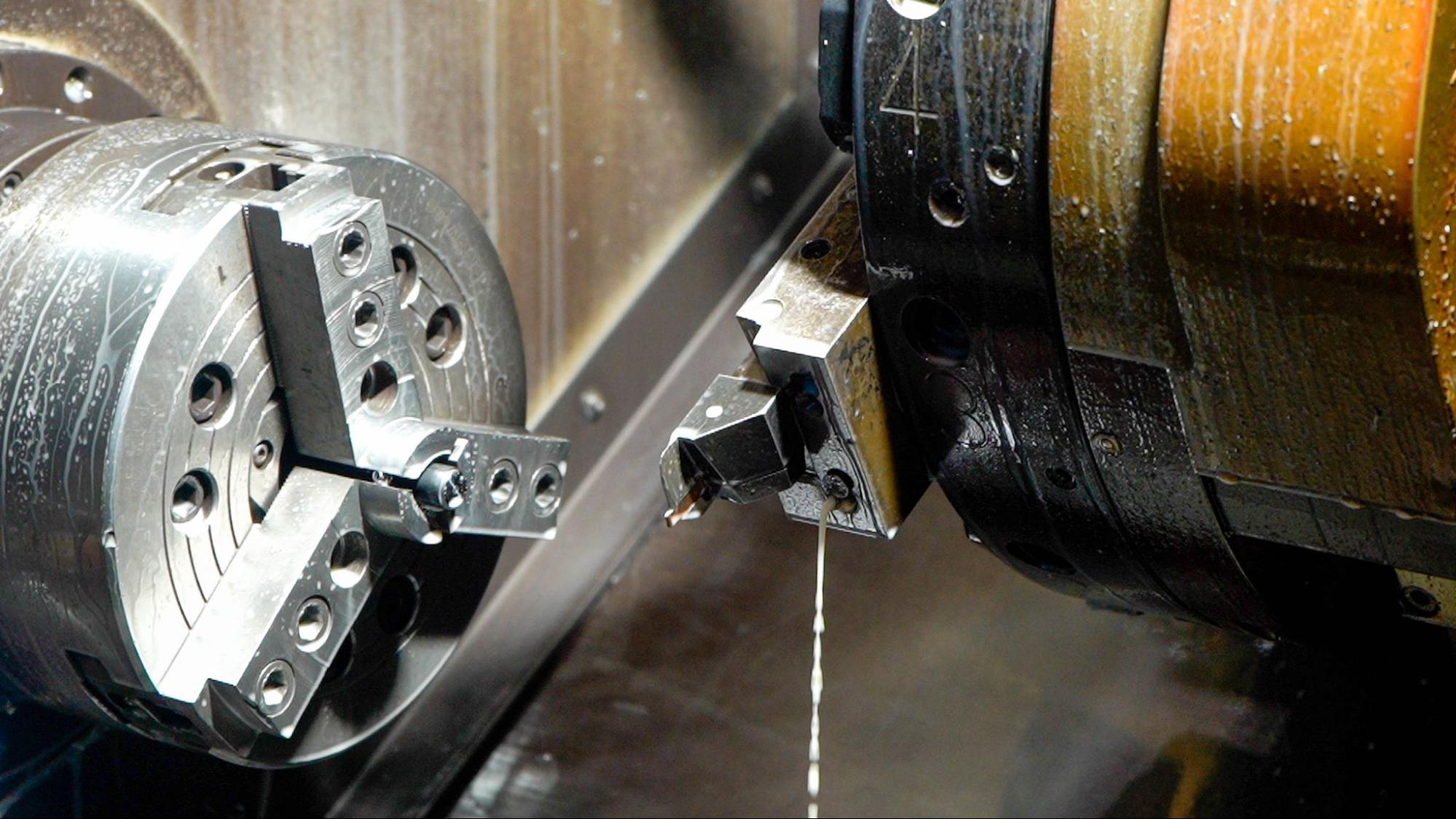
Метчики
Метчик – это винт, оснащённый несколькими расположенными продольно канавками, образующими заострённые кромки. Он может быть гаечным, ручным или машинным, используется обычно для метрических внутренних резьб в малых отверстиях, способствует лучшему отведению из зоны обработки стружки.
При применении машинных метчиков для успешных операций необходим единственный проход. Такие инструменты от стандартных отличаются наличием в конструкции двух составляющих – калибровочной и заборной. При использовании обычных метчиков подбирается комплект. Обычно это три метчика: рассчитанный примерно на 60% объёма работ черновой, решающий задачу на 30% получистовой, а также подходящий для завершающей нарезки чистовой, на долю которого приходится порядка 10% обработки.
Есть наборы из чернового инструментария и чистового. Первый нарезает примерно 75%, а второй – оставшиеся 25%. Заборная зона чернового метчика гораздо длиннее, чем такая зона у чистового варианта. Двух инструментов достаточно для несложных резьб, к которым не предъявляются жёсткие требования точности.
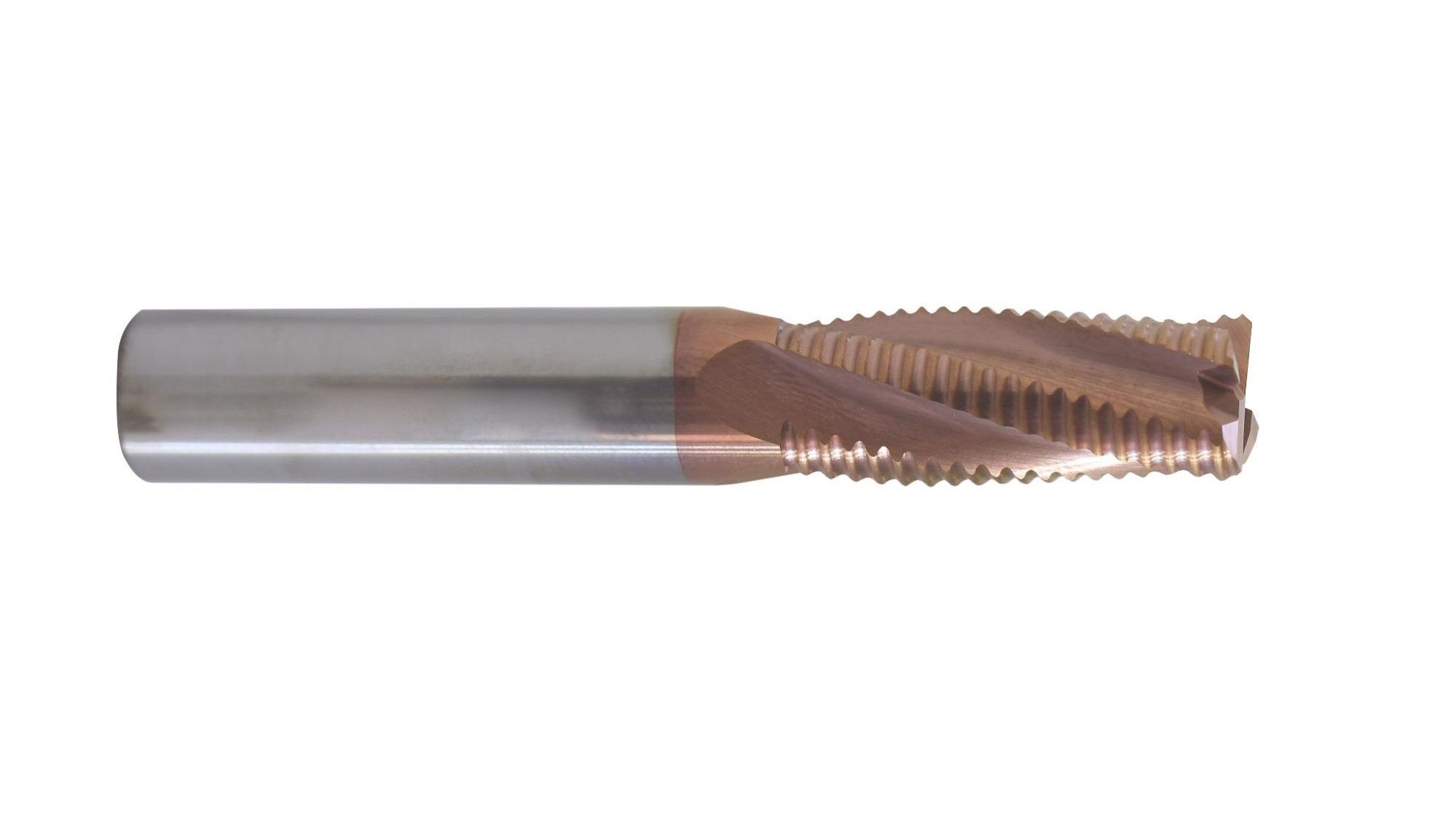
Плашки
Плашка является кольцом, в котором предусмотрены расположенная внутри резьба и канавки для удаления стружек. Такие инструменты с отличными результатами создают наружные резьбовые элементы на применяемых для крепежа болтах, шпилях, винтах. Поверхности предварительно подвергаются обтачиванию до требующегося диаметра. Для последнего предусматривается допуск, составляющий:
- от 0,14 мм до 0,28 для диаметральных величин от 20 до 30 мм;
- от 0,12 мм до 0,24, если диаметр равен от 11 до 18 миллиметров;
- от 0,1 мм до 0,2 при диаметре, составляющем от шести до десяти мм.
Плашка должна закрепляться в патроне, именуемом плашкодержателем. Он находится в пиноли бабки, входящей в конструкцию станка. Плашками нарезание проводится с такими скоростями:
- от 10 до 12 метров в минуту применительно к латуни;
- два-три м/мин для чугунов;
- от 3 до 4 м/мин, если обрабатывается сталь.
От правильности подбора скоростного режима также зависит степень износа. Грамотная настройка продлевает срок службы режущих инструментов. А для беспрепятственного и мягкого захода плашки с торца детали осуществляют снятие фаски, которая по высоте должна быть идентичной профилю образующейся резьбы.
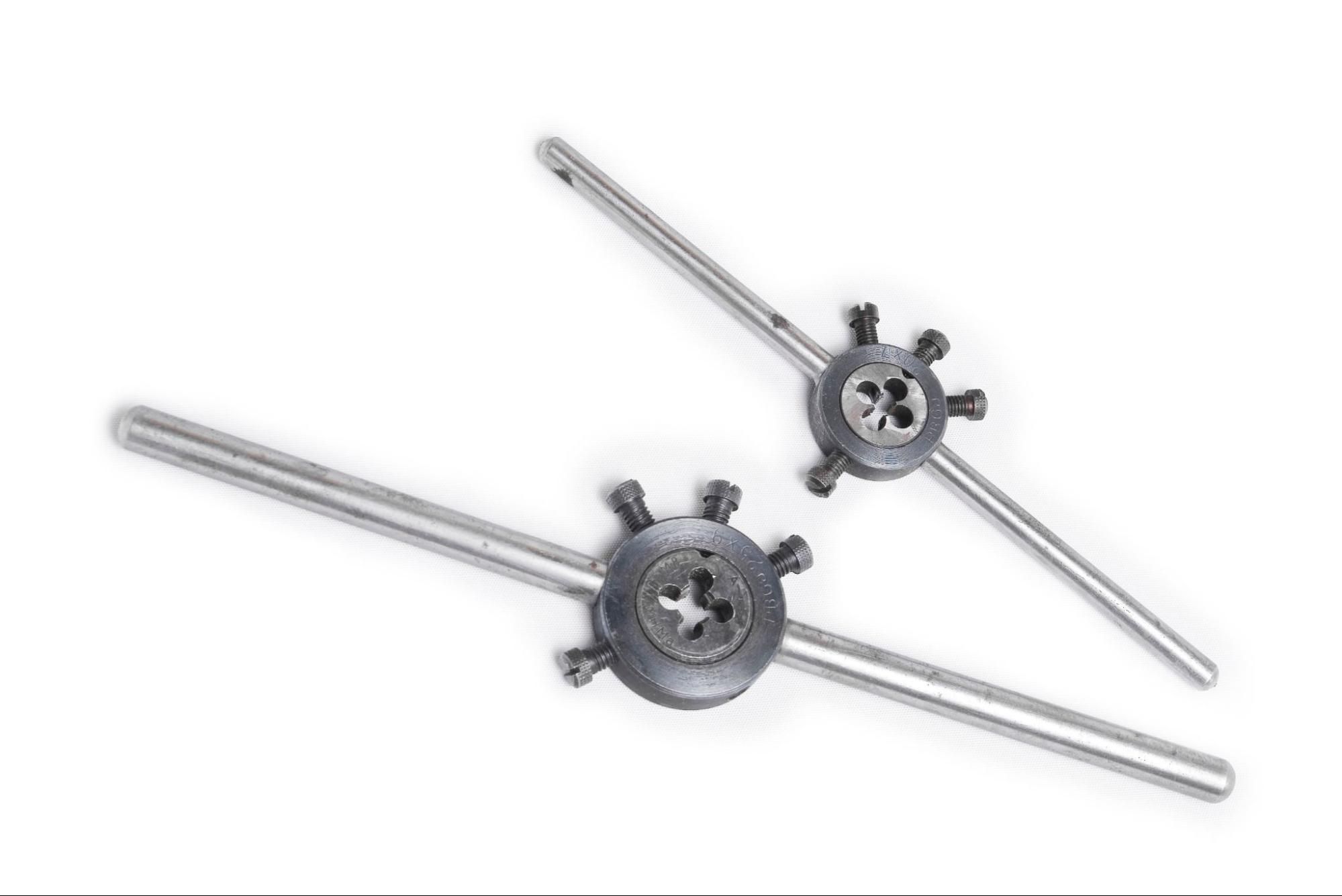
Резьбонарезные головки
Резьбонарезными головками устройства оснащаются не очень часто. Но они подходят для создания разных резьбовых рельефов. В конструкции предусмотрены гребёнки. Для наружной металлообработки пользуются круглыми, радиальными и тангенциальными, а для внутренней – призматическими. Головки имеют исполнение, при котором их рабочие зоны на обратном ходу отдаляются самостоятельно, не задевая только что получившуюся резьбу, не повреждая её.
Гребёнки, которыми нарезают внутренние резьбы, оснащаются заходным конусом. Количество таких рабочих зон может быть разным, зависит от условий эксплуатации, характеристик материала. Круглые гребёнки больше подходят для наружного нарезания. Они просты по конструкции, хорошо решают поставленные задачи, а также обладают стойкостью, за счёт которой возможна многократная переточка для доведения геометрии до исходных параметров.
Если винтовая зона нарезается на длинном винте или червяке, то резьбонарезная головка надёжно монтируется на суппорте обрабатывающего оборудования. Это увеличивает производительность работ. Для оснащения головок применяют стандартные резцы или чашечные элементы.
Получение внутренней резьбы
Такие резьбы формируются резцами, метчиками, а также рассмотренными в предыдущей части статьи резьбонарезными гребёнками, устанавливаемыми в головки. При металлообработке метчиком материал частично срезается и в поверхностных слоях удаляется в виде стружки. Происходит увеличение диаметра отверстия. Для его точного определения следует из наружного диаметра используемого инструмента вычесть шаг резьбы. Ещё эту особенность нужно учитывать при подборе подходящего метчика. Необходимо предусматривать припуск.
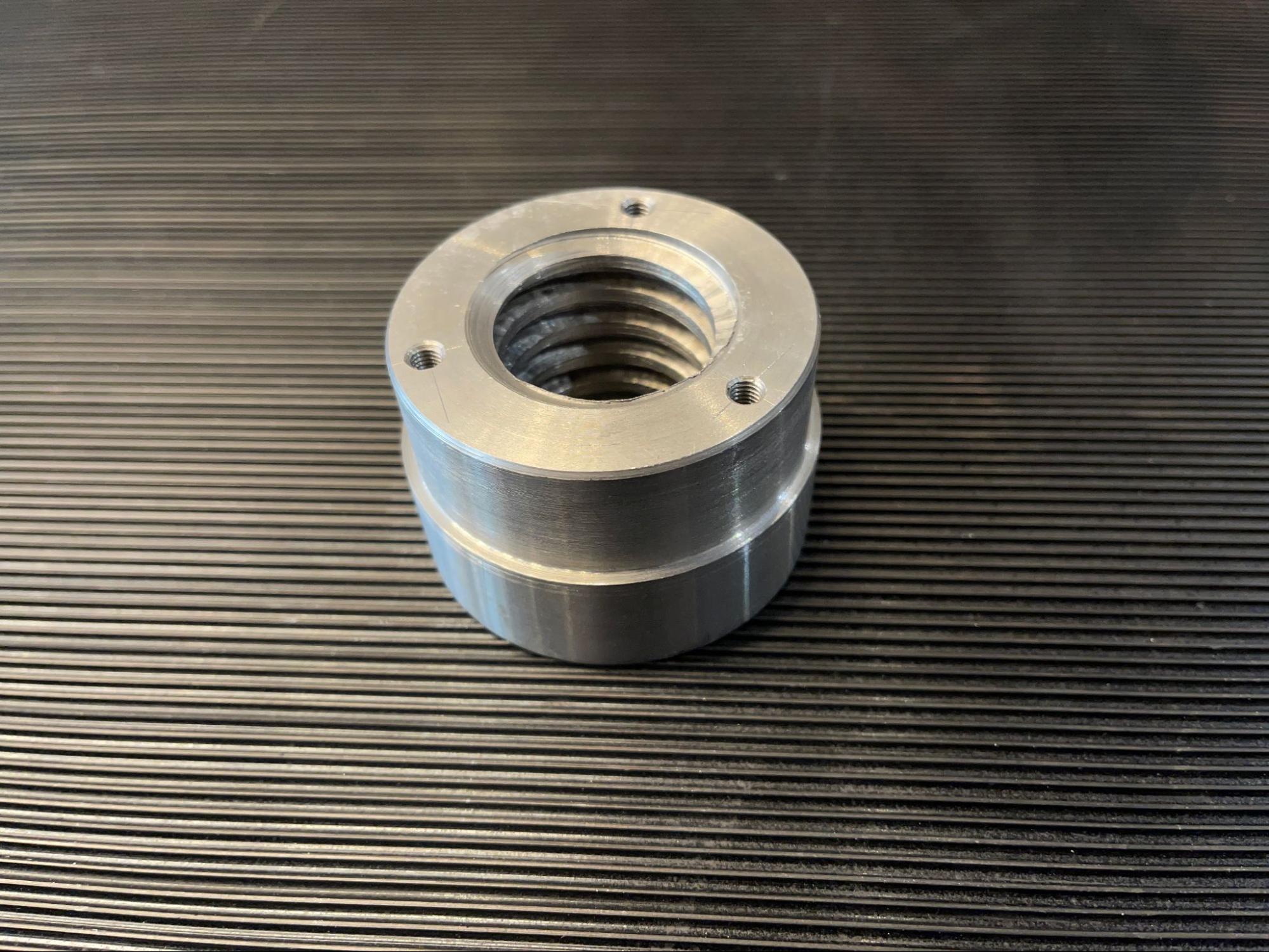
Получение конусной резьбы
Востребованной конической разновидностью считается стандартная, то есть с профилем, являющимся симметричным нормали к оси конуса. Для нарезания подходят те же способы, применимые для получения более распространённых цилиндрических резьб.
Когда нужна конусообразная наружная резьбовая поверхность, заготовка снаружи обтачивается на конус. Этого легко добиться с помощью токарно-винторезного оборудования с установленными резцами, с копировальной линейкой. Но этот метод имеет невысокую производительность.
Если используют токарно-револьверный станок, то его оснащают плашкой. А для высокой точности применяют резьбонарезные головки, снабжаемые различающимися по конфигурации плашками. Последние в ходе технологического процесса раздвигаются в автоматическом режиме.
Коническую резьбу можно получить, используя накатные ролики. Они работают по технологии накатывания. Для внутренней резьбовой конической поверхности подойдёт и метчик, но имеющий специальную конструкцию, адаптированную к данному виду операций.
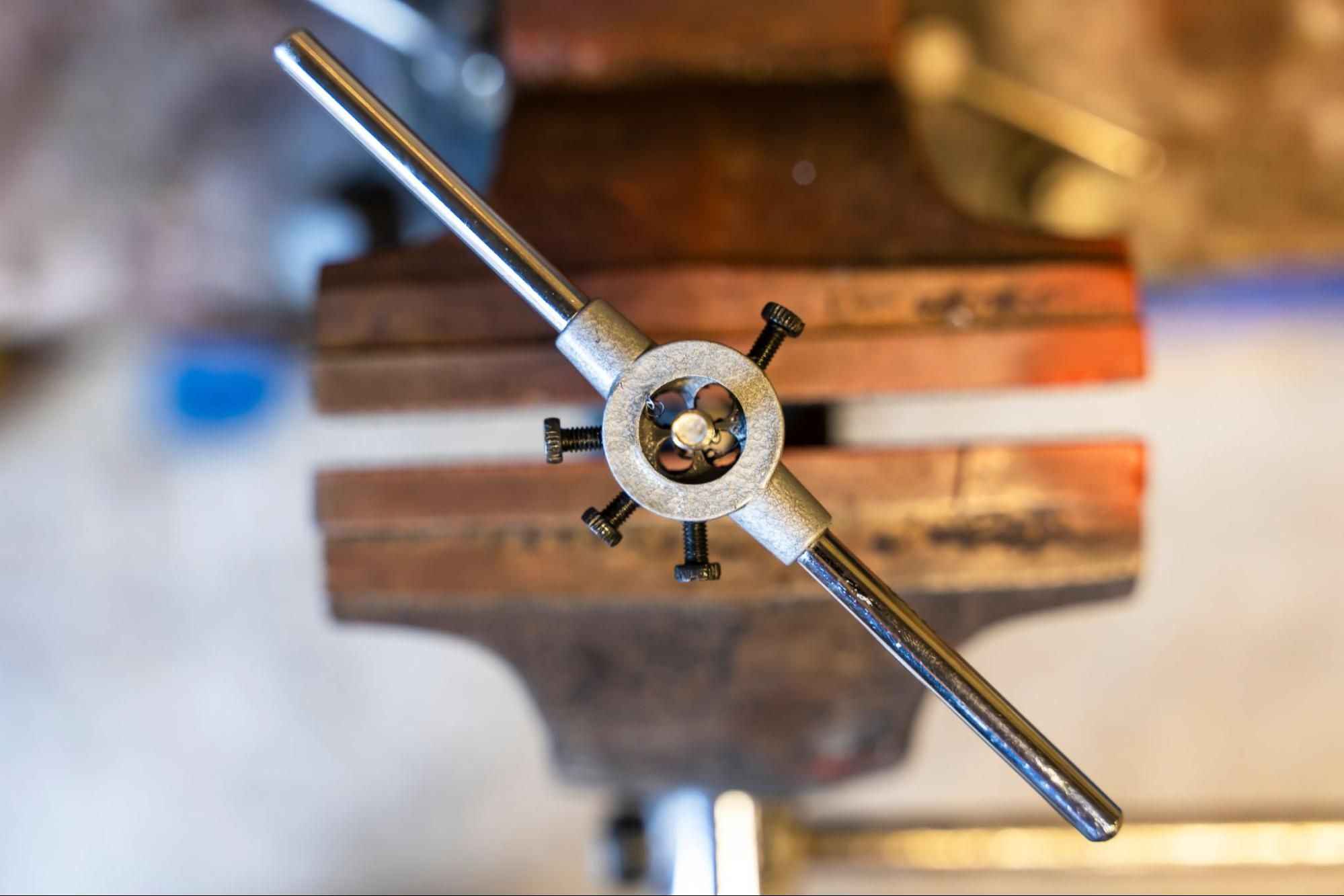
Правила нарезки
Независимо от того, какими способами нарезается резьба, при таких технологических операциях учитываются факторы:
- Вероятность получения рваной, дефектной поверхности. Риски значительно возрастают при увеличении скорости, затуплении режущих кромок инструментов, при некорректном подборе смазочно-охлаждающей жидкости.
- Возможные погрешности. Увеличение или увеличение стержней и отверстий обусловливает получение витков с неполной высотой, несоответствующей техническому заданию, чертежу или стандарту. Разница в высотах по длине возникает из-за изначальной конусности поверхности.
- Растяжка витков. Она возникает из-за того, что самовыдвижная оправка станка тормозит.
- Усадка гайки или иной подобной детали по среднему диаметру. Такие ситуации возникают из-за применения сильно изношенного режущего инструмента.
- Разбивка гаечного элемента по его среднему диаметру. Это возможно от чрезмерно увеличенного переднего угла, который способствует тому, что перья метчика отжимаются.
Чтобы избежать всех этих проблем, необходимо соблюдать правила:
- Подбирать корректно технологию нарезания, а также оснастку для токарного оборудования.
- Использовать оптимальные в конкретных случаях режимы, а также применять подходящие охлаждающие и смазочные материалы.
- Предварительно подготавливать детали, соблюдая данные из справочных таблиц, действующие ГОСТ или иные стандарты, а также технологические планы и прочие документы.
- Контролировать, проверять степень заточки режущих инструментов по шаблонам.
- Отслеживать все настройки станка при каждом рабочем цикле, корректно рассчитывать и собирать гитару.
- Внимательно осматривать первые готовые изделия, чтобы обнаруживать дефекты, несоответствия, неточности. Если они выявлены, требуется корректировка настроек. При серийных производствах контроль должен быть регулярным, так как заданные исходные параметры во время работ могут сбиваться.
- Отслеживать исправность используемых станков, их оснастки. Инструменты нуждаются в регулярных подточках, в своевременных заменах по мере износа.
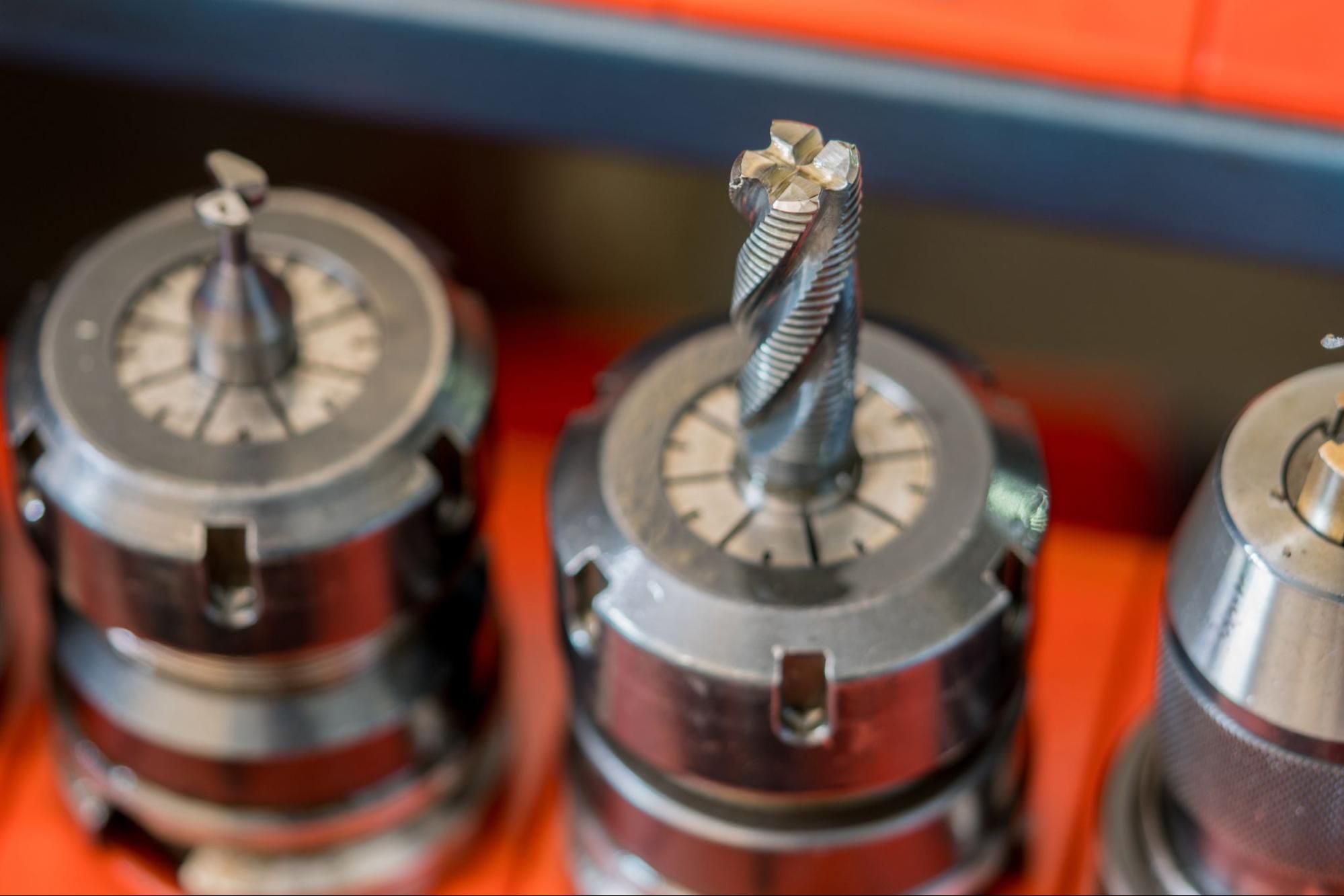
Мониторинг качества
Чтобы соединение резьбового типа было контролируемым, качественным и соответствующим эксплуатационным и техническим требованиям, нужно анализировать соответствие заданным конечным параметрам шага, угла профиля, а также внутреннего диаметра, наружного и среднего. Для проверки таких величин используют разные способы контроля:
- Калибры. Их применяют на серийных производствах.
- Резьбомеры, называемые резьбовыми шаблонами, а также измерительные приборы микрометры в комплексе с заменяемыми вставками. Резьбомером контролируют шаг. С помощью микрометров и устанавливаемых в них сменных вставок проверяют средние диаметры. Такие методы контроля подходят для мелкосерийных производств.
- Три тонкие проволоки и оптиметр или микрометр. Этот способ подходит для высокоточных замеров средних диаметров винтов.
- Инструментальные микроскопы. Их выбирают, если выполняемые работы прецизионные, то есть требования к точности очень строги. Микроскопы помогают оценивать углы, шаги, диаметры.
Важность настройки станков
Чтобы добиваться требуемых параметров, следует грамотно настраивать оборудование. Обязательно связываются вращательное движение шпинделя и перемещений суппорта. Подача в продольном направлении, осуществляемая при каждом обороте шпиндельной детали, должна соответствовать шагу резьбы.
В токарно-винтовых установках настройка подачи выполняется посредством сцепления зубчатых колёс – их коробки подачи с гитарой. Вариаций доступных комбинаций очень много, поэтому можно установить практически любые параметры.
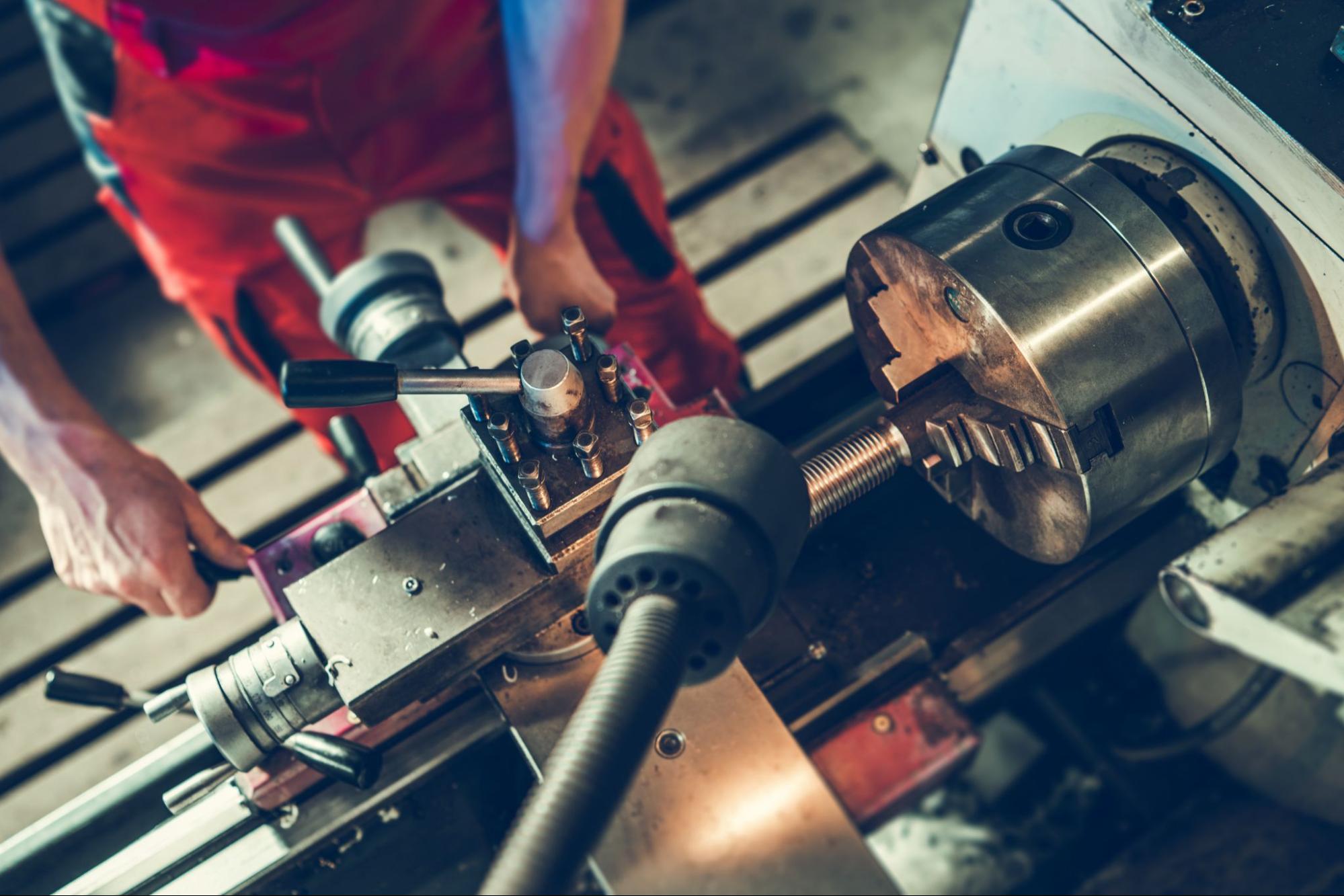
Заключение
Результаты работ зависят, во-первых, от вида и степени автоматизации станка, во-вторых, от мастерства оператора. Компания Profbau выполняет металлообработку профессионально, оперативно и недорого.
Мы используем современное оборудование и доверяем оказание услуг квалифицированным мастерам, которые знают все тонкости технологий и особенности металлов, а также с высокой точностью добиваются соответствия геометрии и размеров заготовок габаритам и формам конечных изделий.