Прокатка металла – это технология его обработки, при которой на заготовку оказывается значительное давление. Операции проводятся на специальных прокатных станках, в которых предусмотрены системы валков. При таком воздействии заготовки меняют конфигурацию, габариты, а также внутреннюю структуру. В этой статье расскажем, какие виды прокатки существуют, как протекает процесс.
Немного истории
Историки считают, что идея прокатки появилась ещё в средневековые времена. Но пик её расцвета в европейских государствах пришёлся на XIX столетие. Потребность в продукции возросла, когда активно строились железные дороги. Изначально рельсы изготавливали из чугуна, но в начале девятнадцатого века в Англии для этих целей начали применять сталь.
Первый полноценный прокатный стан был разработан и представлен в 1828 году. На нём прокатывали пудлинговое железо. И лишь спустя 29 лет обработке стали подвергать бессемеровскую сталь.
Именно рельсы изначально были основным продуктом. Позже технологию начали использовать для изготовления брони для морских судов, деталей паровозов. В 59-м году XIX столетия механик русского происхождения В.С. Пятов создал броневой прокатной агрегат. До него броню изготавливали путём соединения ковкой нескольких тонких листов. Но первые станы имели примитивную конструкцию. Их валки начинали вращаться усилием водяного колеса. Позже их приводила в действие паровая машина. А горячий металл передвигали вручную мастера, поэтому труд был тяжёлым.
Факт! Есть мнение, что прототип станка создал сам Леонардо да Винчи. Тогда валки были деревянными. В конце шестнадцатого века начали использовать агрегаты из дерева с валками из железа. В них прокатывали свинец для труб музыкальных инструментов органов, а позже – золото и серебро, из которых чеканили монеты.
Особенности
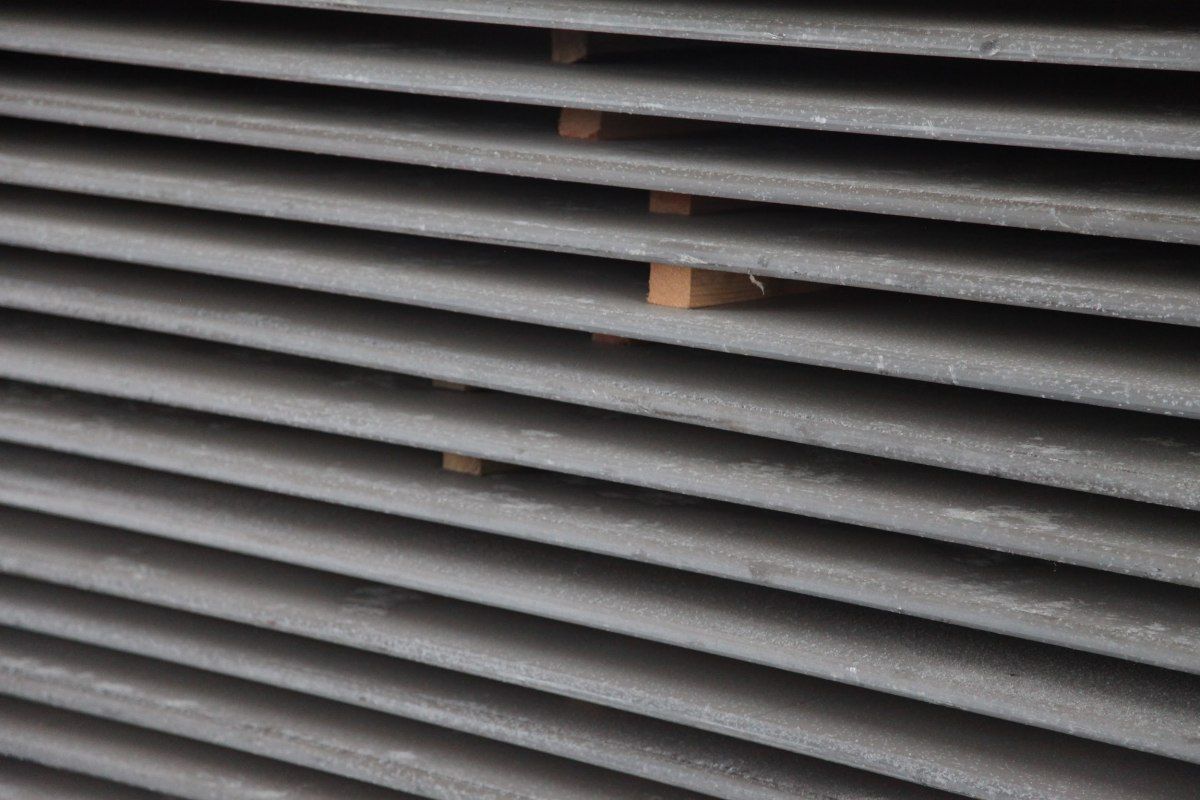
Принцип основан на пластической деформации, создаваемой валками. Такие элементы вращаются, а через оставляемый между ними зазор прокатывается, протягивается заготовка. В основе лежат две силы – трения и вращения. Первое начинается при контакте, в который вступают металл и крутящиеся вальцы. Благодаря такому трению изделия с заданной скоростью перемещается в стане. А давление, которое передают валки, задаёт нужную конфигурацию. Кроме того, из-за сжатия меняется и размер (фактически металлоизделие расплющивается).
Форма, которую в поперечном сечении обретает прокатываемая заготовка, называется профилем. Если по всей длине он одинаков, то является постоянным. Если же есть различия на разных отрезках, то профиль считается периодическим, то есть непостоянным.
Полезно знать! Еще один метод, по принципу схожий с прокаткой, – это вальцовка. При ней также происходит деформирование листовых или трубных материалов, но вдоль определённого направления, в том числе в отдельной зоне. Таким способом формируются изгибы конической, цилиндрической или другой конфигурации.
Виды
Для классификации основных способов используют разные критерии. Один из них – направление, в котором валки задают движение заготовкам. По такому критерию выделяют три вида прокатки:
По температурному режиму прокатку делят на:
Есть ещё одна классификация, в которой основной критерий – это наличие влияния внешних сил. Выделяют два типа прокатки:
Прокатные изделия, их применение
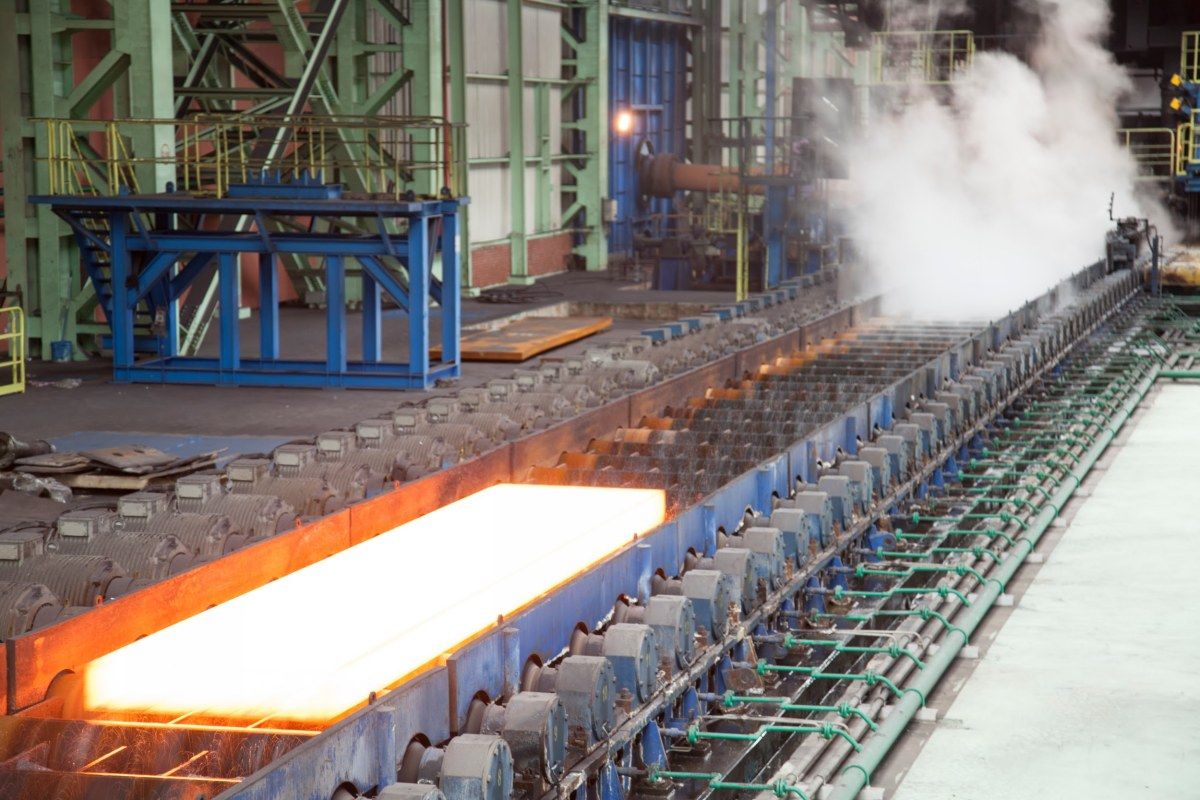
Получаемая при прокатке продукция – это прокат. А совокупность профилей, различающихся по размерам и геометрии, в металлургии называют сортаментом. Выделяют несколько таких групп:
Уголки, листы, трубы, тавры, рельсы, швеллеры, двутавры, прутья, специальные прокатные изделия – всё это используется в разных сферах. Это строительство (стены зданий, их фундаменты), прокладка трубопроводов и других инженерных систем, возведение тоннелей и мостов, а также промышленность. В автомобилестроении, машиностроении, судостроении, авиационной отрасли из проката изготавливают корпусы и другие элементы водного, наземного и воздушного транспорта, спецтехники, производственного и сложного оборудования.
Катаные изделия бывают периодическими и специальными. Первые – это промежуточная продукция, которая идёт на дальнейшее производство или используется для сборки конструкций. А специальные металлоизделия полностью законченные и могут вводиться в эксплуатацию.
Технология прокатного производства
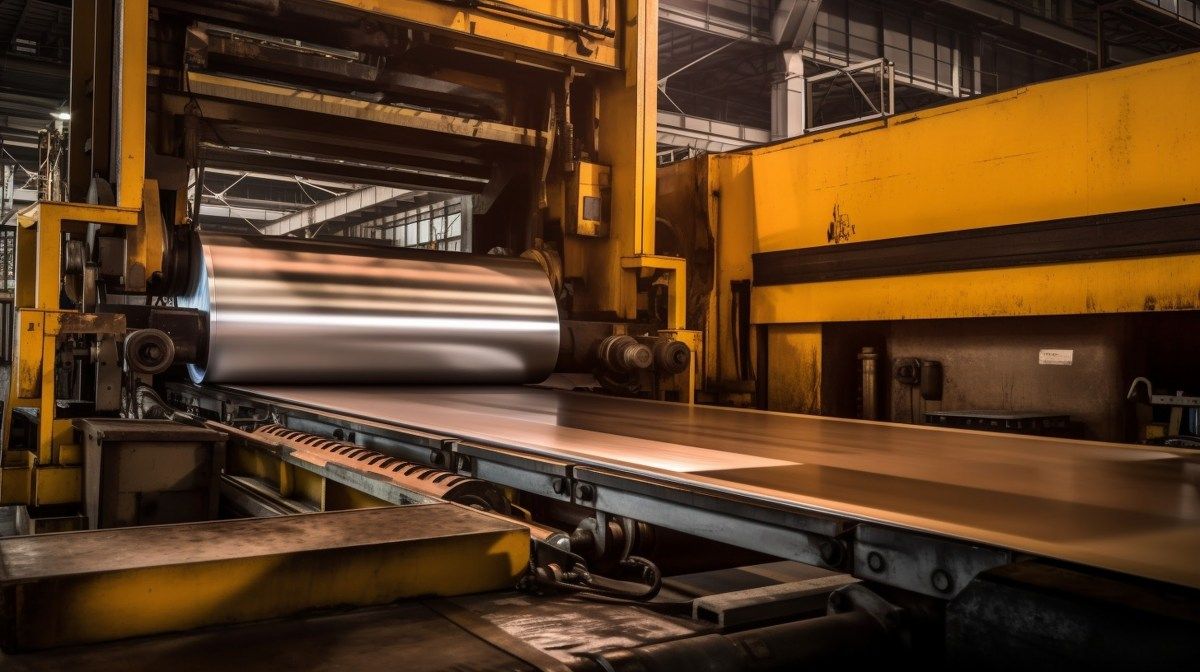
В прокатке выделяют два главных этапа. Первый – это формирование из первичного сырья (металлических слитков) полуфабрикатов (болванок, толстых прутов) или заготовок – листов, труб. На втором этапе заготовленные предметы производства превращают в полноценные изделия с необходимыми параметрами.
Весь цикл прокатки включает следующие операции:
Первичным сырьём обычно являются слитки либо другие полуфабрикаты: блюмы с сечением в виде квадрата с широкой сферой применения, слябы с прямоугольным сечением для получения листов, а также круглые толстые прутья (поковки).
Однократного прокатывания в большинстве случаев недостаточно. Для соответствия заданным параметрам обработку выполняют последовательно, в несколько этапов. И после завершения каждого из них сечение уменьшается в площади. Каждый проход приближает заготовку к готовому идеальному изделию.
Оборудование для прокатки металла
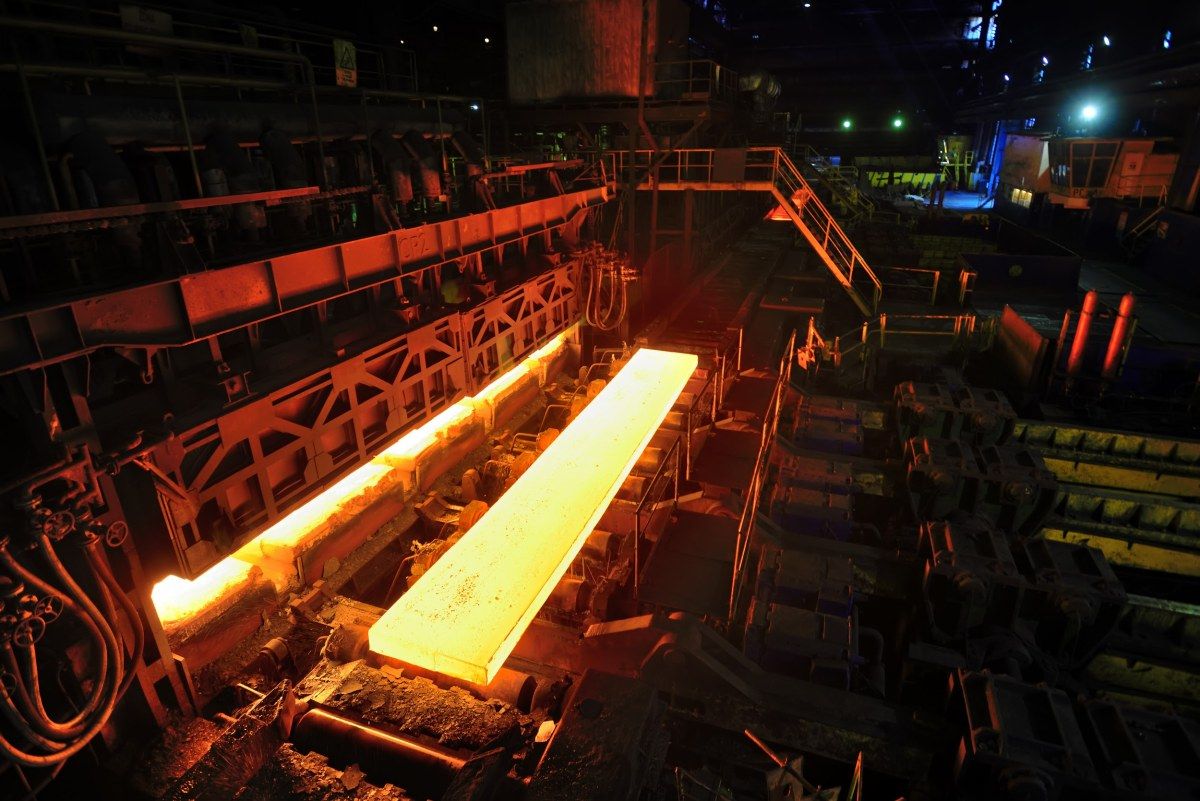
Для производства по данной технологии применяют прокатные станы. Их конструкция – это целый комплекс отдельных агрегатов с последовательным расположением. Среди частей не только непосредственно обрабатывающее оборудование, но и заготовительное, которое подготавливает пластически деформированные заготовки к транспортировке, финишной отделке, упаковке.
Станок – сложный, многокомпонентный агрегат. Его составляющие:
Одна клеть состоит из двух станин, объединяемых в единую установку с помощью металлической поперечины. Такая установка зафиксирована на основании. Движение валок запускается за счёт работы мотора. Его усилие направляется через оснащённую шестерёнками клеть, а также через шпиндели. В одной клети предусмотрена одна пара вальцов или несколько.
По количеству вращающихся рабочих элементов агрегаты бывают двух-, трёх, четырёх-, а также многовалковыми. Есть и универсальные станы, оснащаемые валками, объединяемыми в группы и располагаемыми вертикально и горизонтально.
Вальцы могут иметь разные формы. Так, для листов необходимы гладкие бочки. Они после каждого прохода сближаются до достижения требуемой толщины заготовки. Для фасонного и сортового проката общего назначения или специального подбираются бочки, имеющие по своей окружности канавки, то есть ручьи. Их название – ручьевые или калиброванные. Отрезок между канавками, находящимися на противоположных валках, – это калибр.
Горячая прокатка
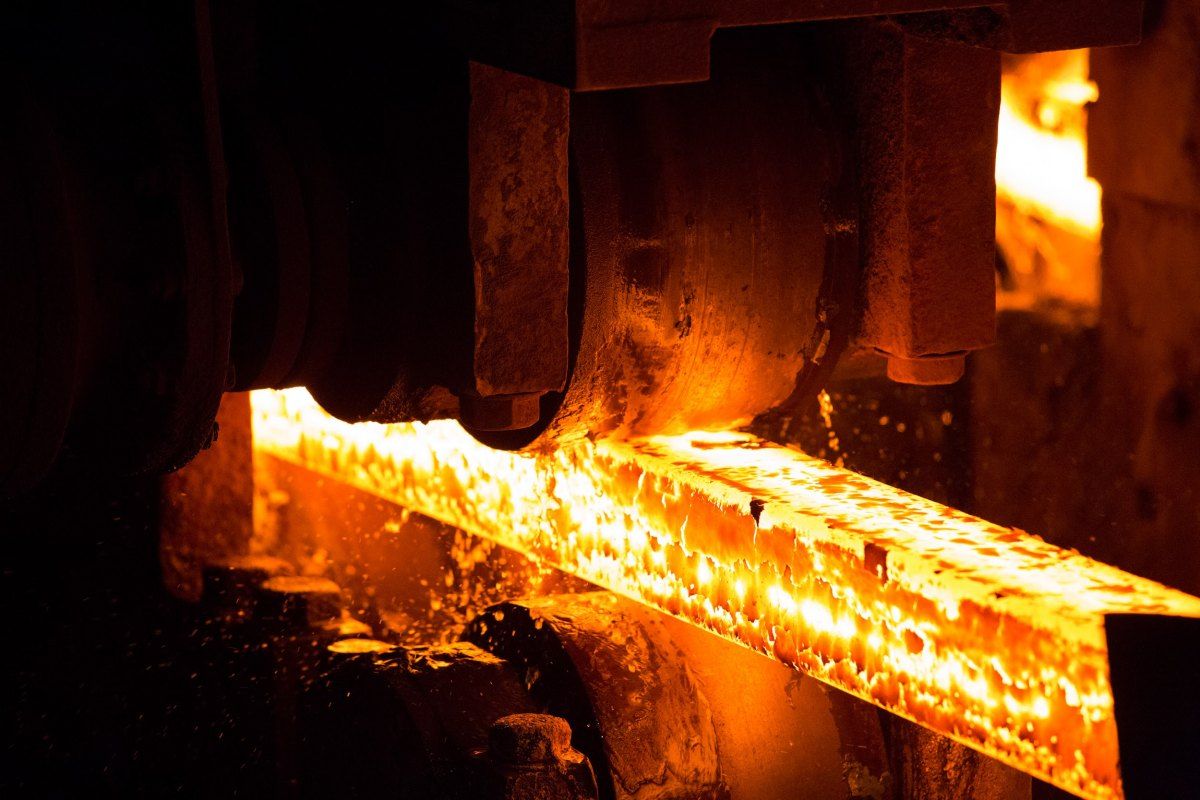
При такой технологии требуется поддержание определённого температурного режима – обычно более 920-950 градусов Цельсия. Для некоторых сплавов, таких как низкоуглеродистые стали, значения ещё выше – почти 1190℃.
Сегодня горячая прокатка – это порядка 80% всего объёма изготавливаемого металлопроката. При такой технологии производственные усилия небольшие, расход электроэнергии ниже, так как нагретые заготовки благодаря повышению пластичности всего за один или два прохода значительно уменьшаются в площади поперечного сечения и быстрее доходят до конечных заданных характеристик. Это снижает стоимость производства. Некоторые полуфабрикаты, например слитки, могут обрабатываться только с предварительным интенсивным нагреванием.
Но качество горячекатаных изделий обычно среднее. Так, на листах могут оставаться окалины, а в центре они часто прогибаются. Это требует правки: выравнивания, зачистки, шлифования.
Обычно горячекатаную продукцию используют там, где к качеству и внешнему виду не предъявляются жёсткие требования. Это возведение крупных объектов, установка ограждающих и больших опорных конструкций, сборка внутренних узлов крупногабаритной техники. Сферы применения – тяжёлое машино- и станкостроение, гражданское и промышленное строительство.
В прокатные станы заготовки подаются после нагрева в специальных печах. Но есть и другой вариант – использование машин непрерывного литья (МНЛЗ), из которых полуфабрикаты до их полного остывания передаются в прокатку. Получается практически непрерывное производство.
Холодная технология
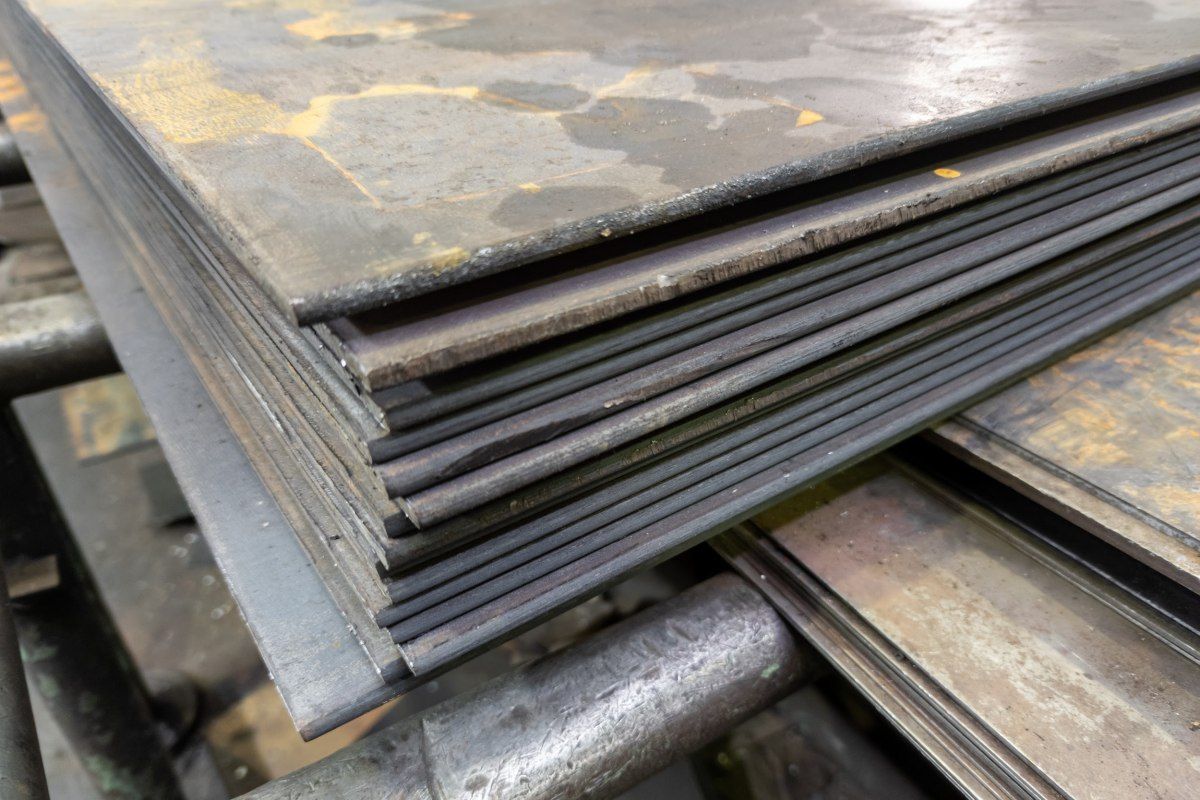
При холодной прокатке путь заготовок более длинный. Во-первых, они обычно подвергаются предварительному травлению, во-вторых, прокатываются многократно для достижения ожидаемых характеристик.
Так как температуры невысокие, внутреннее напряжение распределяется равномерно, не возникает окалина, которую перед завершающей отделкой нужно обязательно удалять. При сгибании холоднокатаный прокат не растрескивается, он имеет отличную прочность на разрывы и растяжения (в процессе прокатки механические свойства улучшаются). Толщина получается равномерной по всей площади, внешний вид эстетичен и не требует корректировок.
Для холодной технологии применяют обычно материалы с оптимальной пластичностью. Прежде всего, это низкоуглеродистые стали. Они хорошо сгибаются и принимают нужные конфигурации. Благодаря этому холоднокатаная продукция получила широкое применение в разных отраслях: судо-, машино-, приборо- и автомобилестроении, строительстве, облицовке фасадов. Из таких изделий производят металлические кровли, профнастил, элементы сэндвич-панелей. Холоднокатаные листы можно цинковать, красить для улучшения эстетики и усиления антикоррозионной защиты.
Сравнение
Сравним в таблице холодную и горячую прокатку:
Прокатка | Горячая | Холодная |
Напряжение | Неравномерно распределяемое. Но такой вариант подходит для машиностроения | Равномерно распределяющееся, что важно для автомобиле-, приборостроения |
Поверхность | С неровностями: вероятны прогибы, окалина | Ровное, соответствует строгим требованиям |
Использование | Производство тяжёлых агрегатов, больших машин | Судо-, машино-, автомобиле-, приборостроение |
Заключение
Прокатать заготовку качественно могут только профессионалы, обладающие нужными навыками и использующие современное оборудование. Именно такие мастера работают в компании Profbau.
Мы выполняем заказы любой срочности оперативно и качественно. Строго соблюдаем требования заказчиков и стандарты, знаем особенности всех существующих технологий и учитываем важные нюансы для максимального приближения геометрии и размеров заготовок к габаритам и форме конечных изделий. Обратитесь к нам удобным способом.