В настоящее время технология газовой резки разных категорий металлических сплавов считается эффективным и востребованным методом. Ее популярность в разных сферах промышленной деятельности обусловлена отсутствием строгих требований к месту, на территории которого проводят работы. В этой статье эксперты Profbau подготовили информацию об особенностях, возможностях, преимуществах и недостатках процесса.
Резка газом — что это такое?
Процедура представляет собой техническое решение, широко используемое в производственных и промышленных целях разной направленности. В процессе обработки не требуется наличие сложного оборудования, дополнительных приспособлений и комплектующих. За счет этого технология востребована в масштабном производстве, а также среди предприятий среднего и малого бизнеса. Способ актуален при выполнении строительных, ремонтных, сельскохозяйственных работ разной степени сложности. Современные устройства характеризуются сравнительно небольшим весом, расширенным функционалом, возможностью режимной регулировки основных параметров, легкостью транспортировки и удобством эксплуатации.
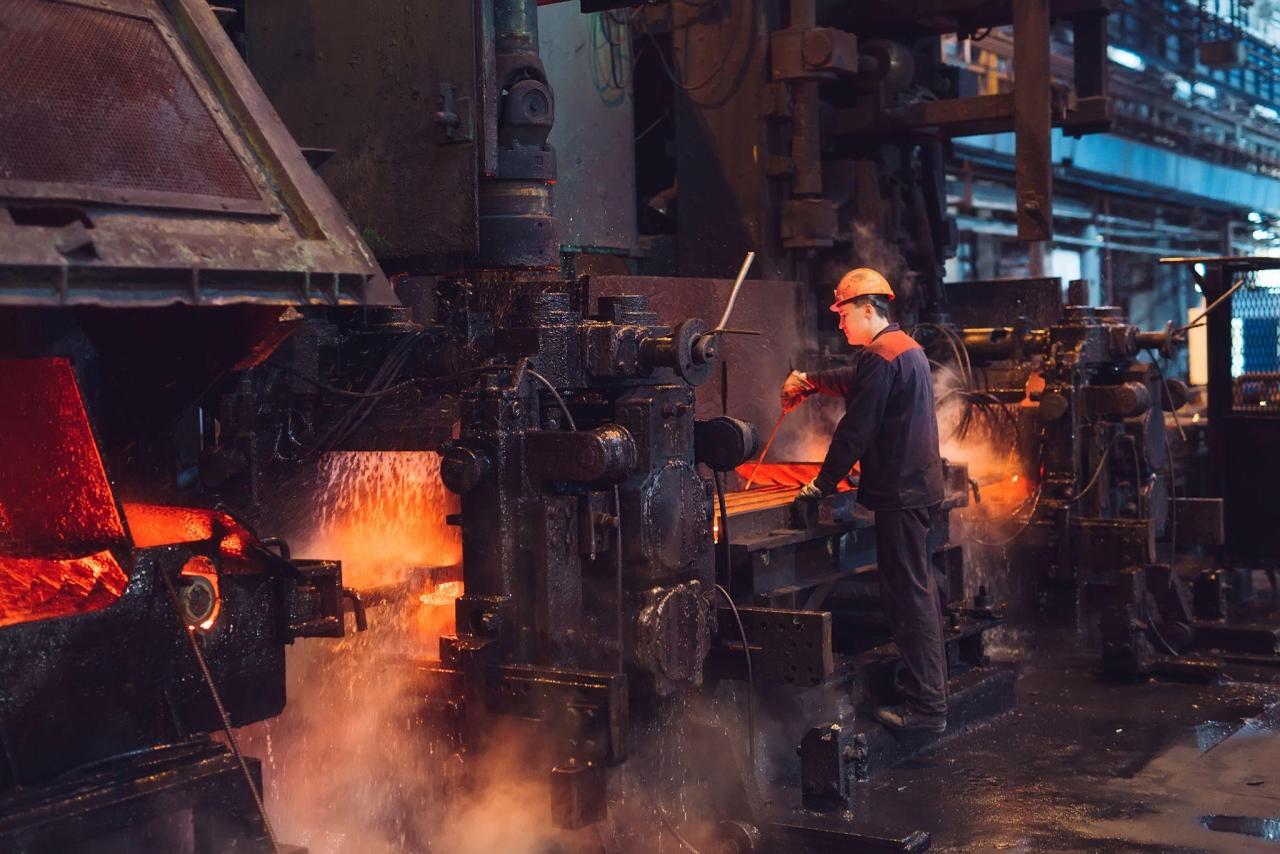
Технология газовой резки металла выглядит так:
Основной рабочей частью оборудования является резак. Предназначение модуля заключается в точной дозировке рабочей среды с целью ее равномерного смешивания с кислородом в единое газовоздушное соединение.
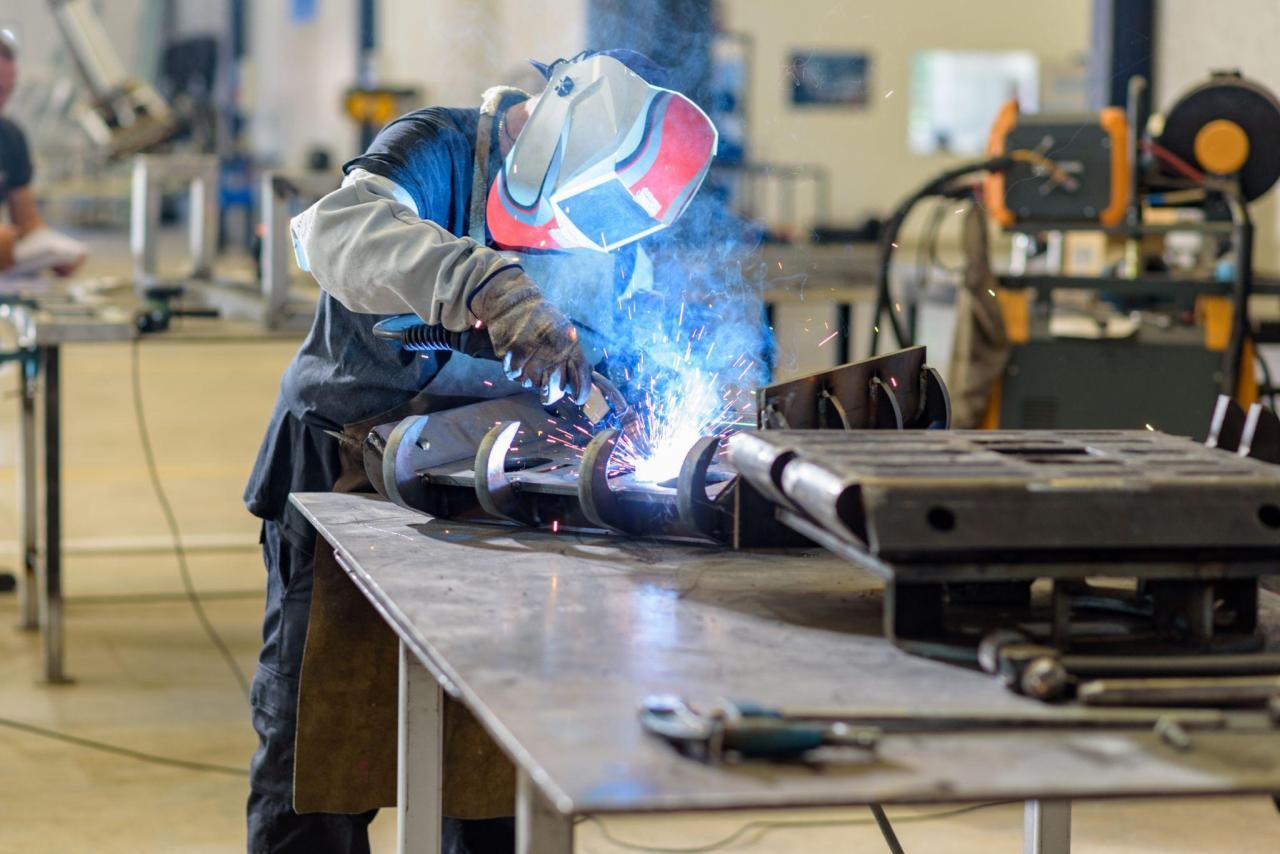
Преимущества и недостатки технологии
Газокислородый способ характеризуется сравнительно большим количеством положительных сторон применения. Каждая из них делает технологию проще, доступней и практичней с экономической точки зрения.
Достоинства:
Для полноты понимания общей картины озвучим существующие недостатки, которые можно устранить путем соблюдения утвержденного регламента.
Качество материала может пострадать в связи с чрезмерным термическим воздействием на его поверхность. В результате возникает деформация. Наиболее частыми ее проявлениями являются изгибы под непредусмотренными чертежом углами, кручение, коробление. Риск деформации металла особенно велик при раскрое листовых заготовок. При демонтаже возведенных ранее конструкций вероятность отрицательных изменений не настолько существенна.
Виды резки металла газом
Классификация газовой резки различных видов и сортов металлических сплавов включает в себя несколько утвержденных методов. Принцип и формат выполнения обработки с применением бесконтактной режущей оснастки зависит от используемых газов, а также ряда других особенностей. Выбор конкретной технологии основан на том, какие именно задачи необходимо выполнить. При возможности подключения к постоянному источнику электроснабжения воспользуйтесь кислородно-электрической дуговой резкой. Для изделий и заготовок из низкоуглеродистых сталей, подойдет газовоздушная смесь на основе пропана.
Резка пропаном
Метод с использованием кислородно-пропановой комбинации является одним из наиболее распространенных способов выполнения работ. При всей простоте реализации технология имеет ряд ограничений, пренебрежение которыми недопустимо. Операция рассчитана на выполнение задач, связанных с обработкой титановых сплавов, изделий и конструкций из низкоуглеродистых и низколегированных сталей разных марок. Главное условие, которым руководствуются при выборе данного способа, заключается в процентном содержании углерода или легирующего компонента в обрабатываемом материале. Если параметр превышает 1%, от технологии стоит отказаться в пользу другого метода.
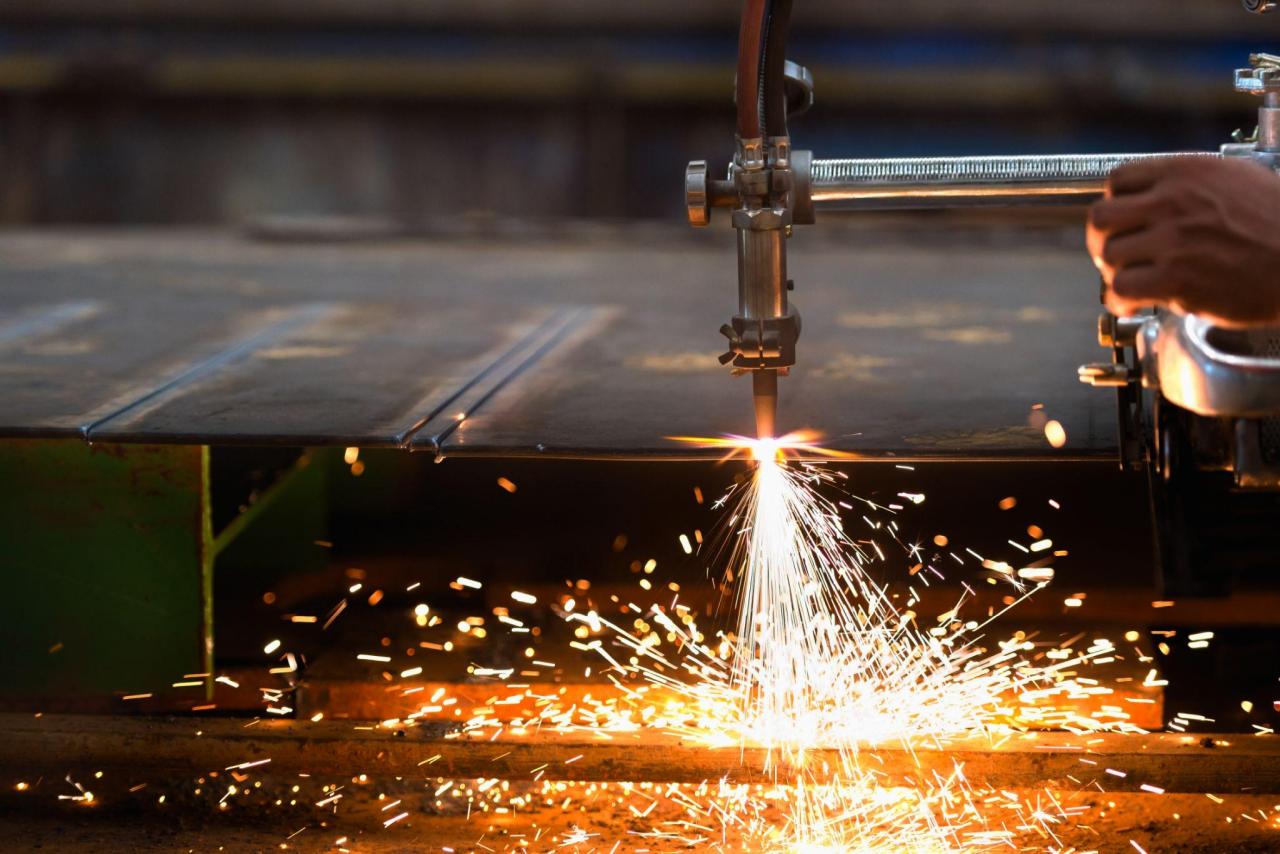
Воздушно-дуговая резка
Представляет собой эффективную разновидность обработки металла с применением кислородно-электрической дуговой резки. Процесс плавления достигается при помощи электрической дуги, получение которой происходит при подключении рабочего инструмента к стабильному источнику электричества (стационарным розеткам или электрогенераторам). За удаление остатков расплавленного состава с поверхности отвечает воздушная струя. Рассматриваемый способ предполагает направленную подачу газа непосредственно вдоль электрода. При выборе такого способа стоит учесть, что воздушно-дуговая резка рассчитана на выполнение резов небольшой глубины. При этом их ширина может быть любой — все зависит от мощности оборудования и концентрации струи.
Кислородно-флюсовая резка
Особенностью технологического процесса является создание дополнительного теплового эффекта, а также использование специального компонента — феррофосфора. Высокая степень теплопроводности меди, латуни или бронзы затрудняет их раскрой привычными способами. На помощь приходит кислородно флюсовая резка цветных сплавов с применением активного вещества, предназначение которого заключается в обеспечении особой податливости материала. Метод получил широкое применение для быстрого и аккуратного разрезания материалов на основе твердоплавких окислов. Подходит для раскроя чугунных заготовок, легированных сталей, продукции из меди и алюминия, зашлакованных металлов и железобетонных конструкций.
Копьевая резка
Высокотехнологичная разновидность методики, используемая для ускоренного демонтажа габаритных стальных массивов, качественной разделки производственных отходов, а также металлургических аварийных скрапов. Отличие технологии кроется в увеличенной скорости выполнения операции. Принцип работы оборудования заключается в генерации высокоэнергетичной струи, которая при взаимодействии с поверхностью обрабатываемого материала снижает расход стальных копьев. Увеличенный скоростной режим и отсутствие остаточных образований обеспечивается за счет полного сгорания металла.
Расход газа
На показатель взаимосвязи количества расходуемой газовой среды от объемов выполняемых задач непосредственное влияние оказывает конкретный метод. Например, нормы обработки металлических сплавов газом при выборе кислородно-флюсового метода предполагают более экономичный расход газовой смеси по сравнению с воздушно-дуговом аналогом.
Кроме способа обработки на окончательное значение показателя влияют дополнительные факторы:
При соблюдении табличных данных и технологии производства ожидаемый результат гарантирован.
Резка толстого металла
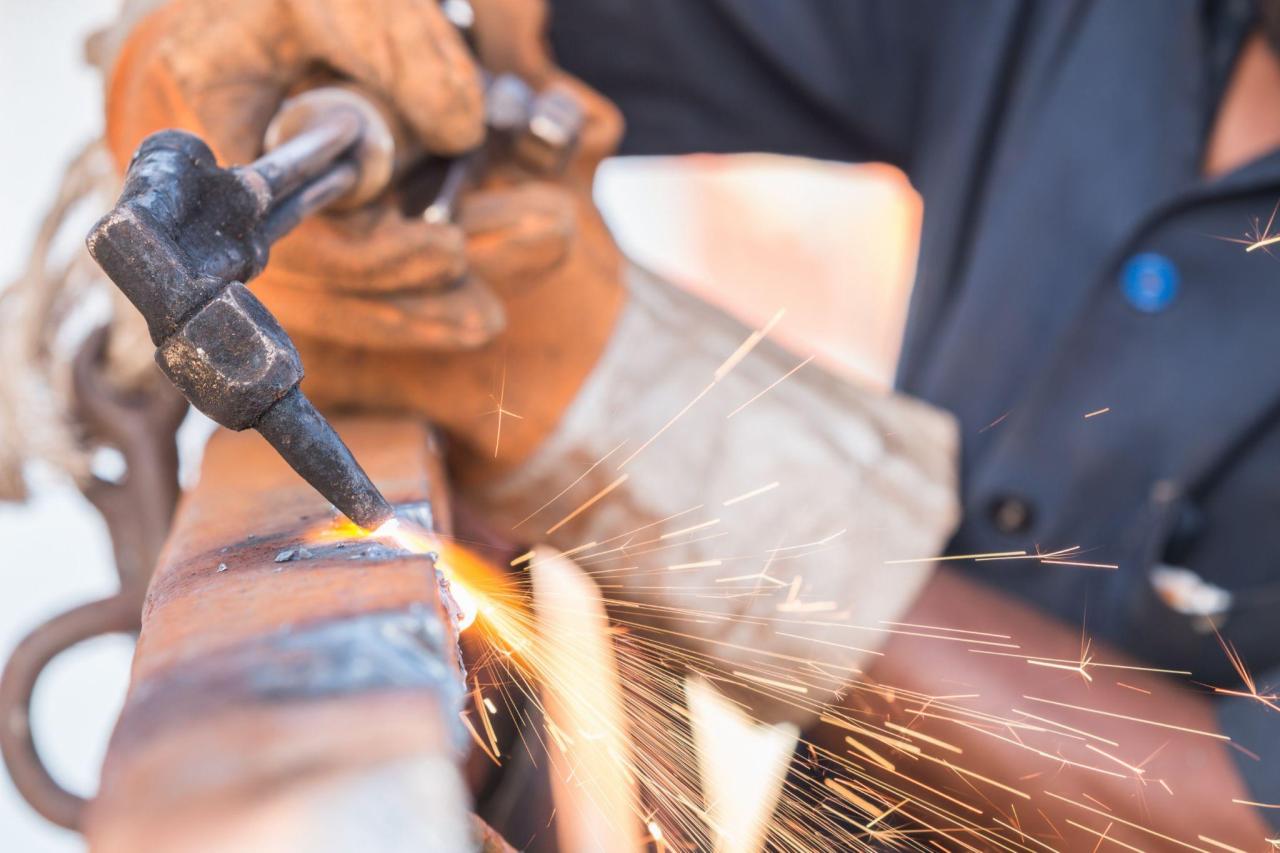
Газорезка — способ, применяемый для раскроя листовой стали и изделий из других видов металла толщиной от 0,5 до 6 см включительно. Выделяемое оборудованием тепло образуется вследствие реакции окисления. Именно оно отвечает за нагрев и плавку металлических поверхностей в точке реза. Удаление остаточных продуктов сгорания из зоны проведения работ происходит под воздействием направленного потока газа.
Ряд требований, соблюдение которых является обязательным:
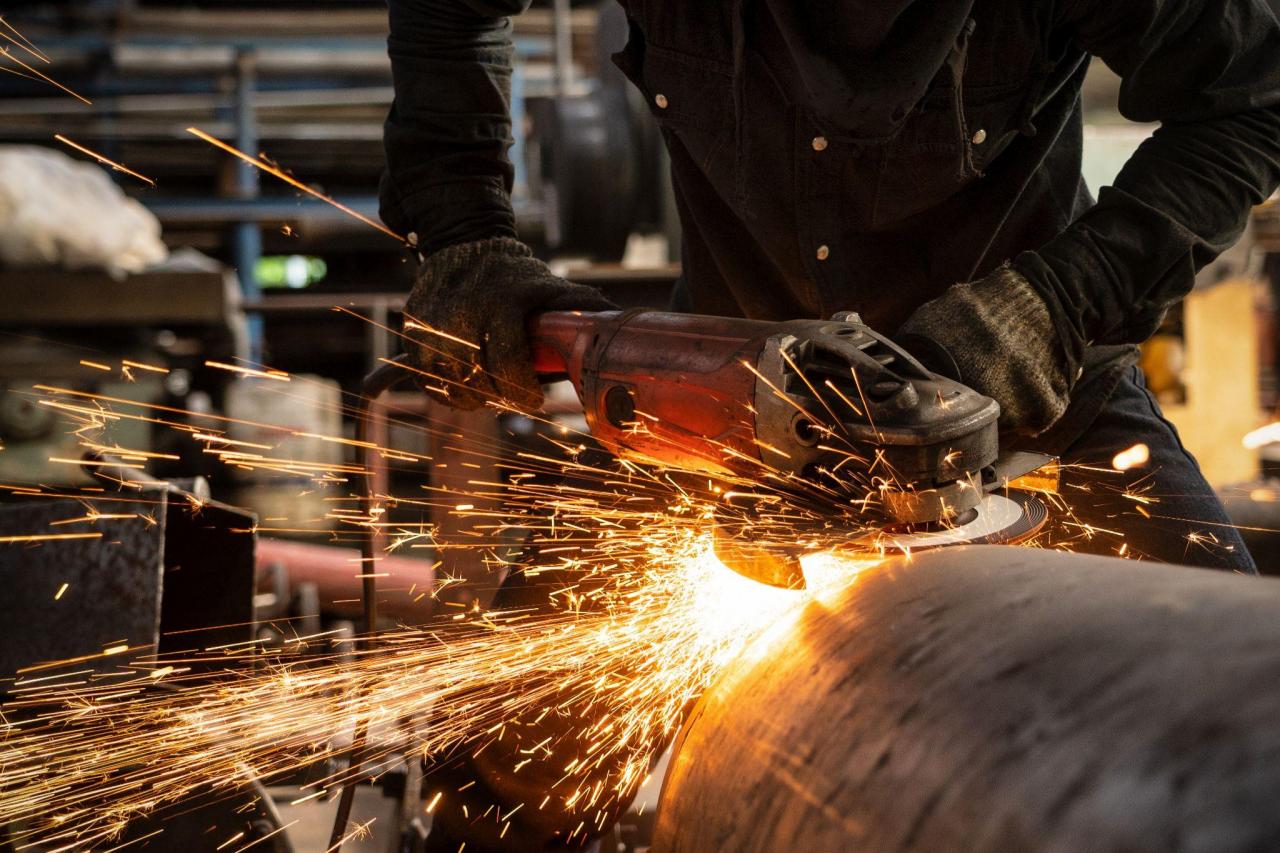
На рукоятке инструмента располагаются три патрубка с разъемами. Их предназначение заключается в доставке смеси на зону обрабатываемой поверхности металла. Первый патрубок отвечает за подачу ацетилена или пропана, второй — кислорода, третий — охлаждающей жидкости. Для регулировки рабочего давления используют выносной редуктор, установленный на баллоне. Значение этого показателя не должно превышать 12 атмосфер.
Деформация материала
С применением бесконтактной технологии выделяется большое количество тепловой энергии. Чрезмерный нагрев металлической поверхности в зоне среза становится главной причиной нежелательного изменения формы и потери полезных качеств.
Уровень деформации зависит от габаритов детали, толщины листа и материалу, из которого он выполнен. Аккуратного обращения требуют длинные узкие заготовки, а также тонколистовые материалы. Готовые изделия нуждаются в дополнительной правке. Для минимизации деформационных погрешностей в начале и конце будущего среза оставляют небольшие перемычки. Их удаление происходит после того, как поверхность полностью остынет.
Обратный удар
Под данным определением понимают процесс горения в обратную сторону относительно направления потока. Об обратном ударе свидетельствует характерный хлопок, сопровождаемый следующими признаками:
Наиболее опасным проявлением является второй вариант. Здесь возникает существенная угроза взрыва, предотвратить которую можно следующим образом:
При одновременном появлении двух и более хлопков необходимо проверить целостность рукавов, а также герметичность разборных соединений. При использовании любого газового оборудования требуется неукоснительное соблюдение требований безопасности, в том числе использование средств индивидуальной защиты.
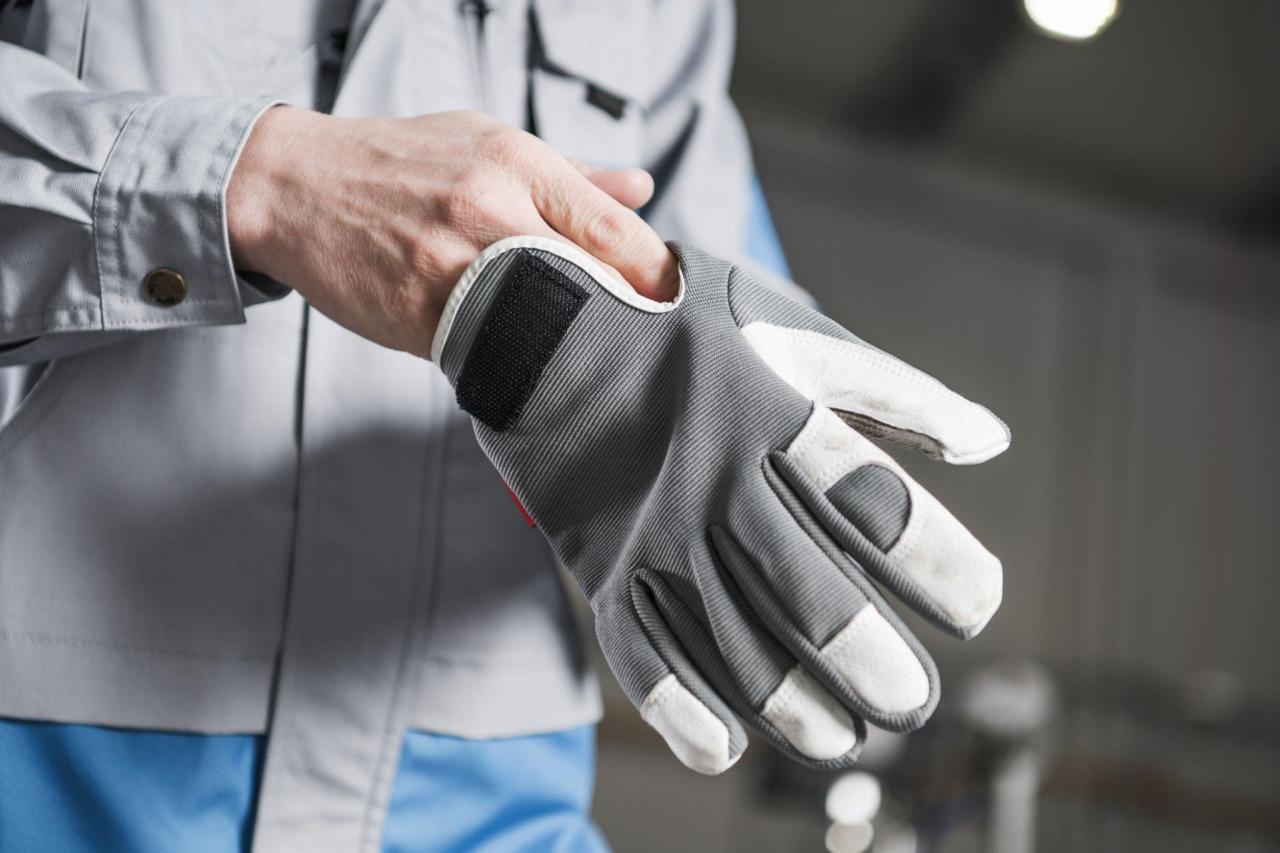
Условия для успешной обработки изделий:
Заключение
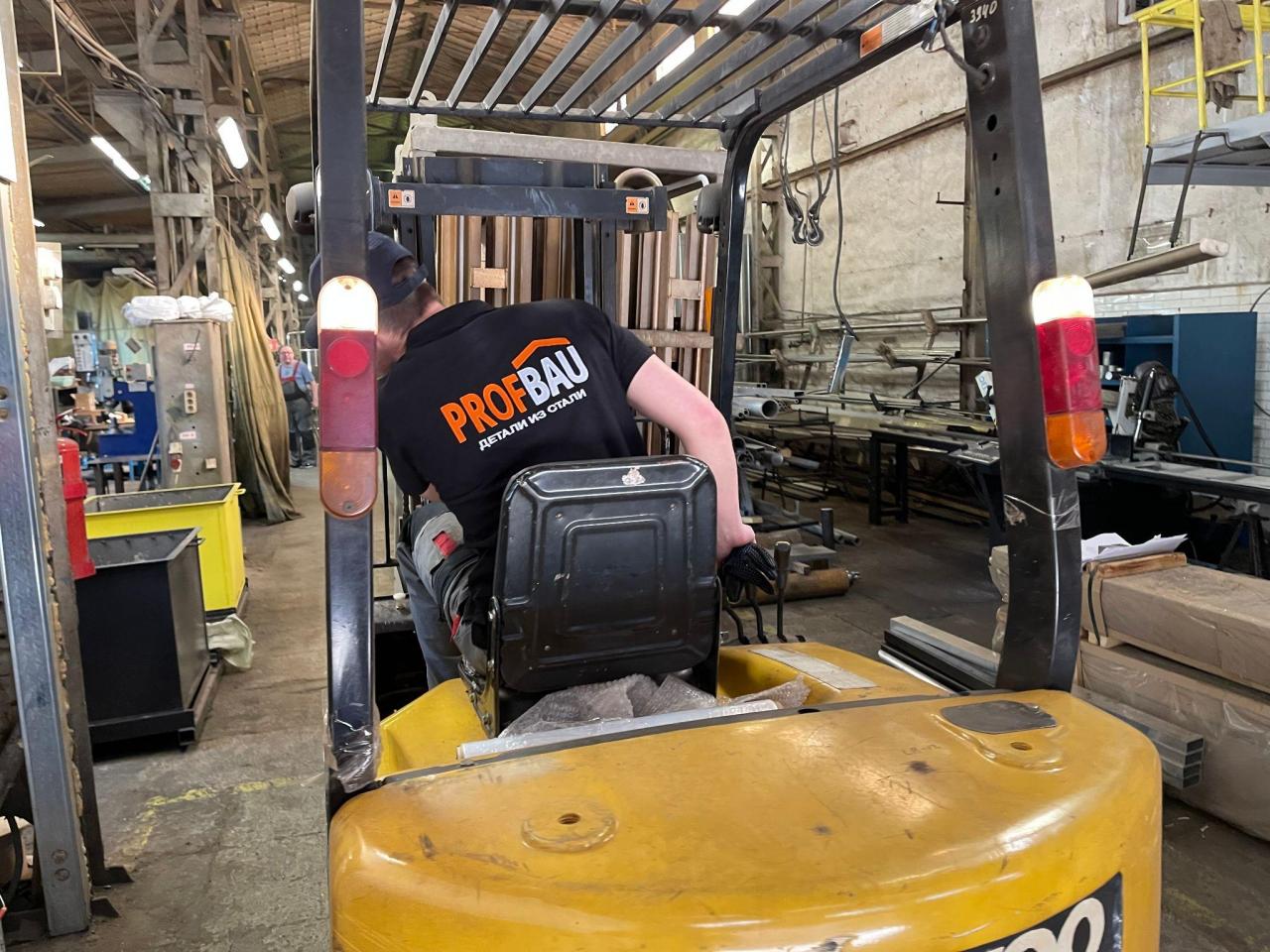
Компания Profbau оказывает услуги, связанные с газовой резкой металлических элементов разной сложности исполнения. Мы используем профессиональное оборудование высокой точности. При обращении в нашу организацию, вы получаете:
- Консультацию и информационную поддержку на всех этапах производства.
- Соблюдение правил, норм и рекомендаций, влияющих на получение результата.
- Контроль качества на всех этапах процедуры.
- Сдачу готового заказа в точно оговоренные сроки.
Заключаем договора с разными категориями заказчиков, предлагаем вариативные решения для обработки металлов. Подробности уточняйте по телефону: +7 (495) 138-25-25. Будем рады помочь!