Расточка отверстий – разновидность механической обработки определённых металлоизделий. Она проводится на специальных станках с целью доведения деталей до заданных параметров, соответствующих стандартам, технической документации или другим требованиям. Узнайте, как растачиваются отверстия в металлических изделиях, какие технологии для этого применяются, и каких ошибок следует избегать.
Зачем нужна расточка отверстий
Операция расточки необходима для финишной доработки, достижения нужных параметров и качества поверхностей отверстий. Она может потребоваться для увеличения внутреннего диаметра, корректировки конфигурации, получения нужного направления или соосности нескольких отверстий в одной детали, восстановления корректного расположения оси изделия по отношению к его плоскости.
Обычно растачивание выполняется на последних этапах производства в качестве завершающей, чистовой металлообработки. Но иногда оно используется для устранения дефектов и исправления ошибок, допущенных при изготовлении.
Растачиваются обычно детали, изготавливаемые методами ковки, литья, штамповки. Первичные отверстия получают сверлением, газоплазменой резкой, отливкой, с помощью пластической деформации.
Технология растачивания отверстий
Растачивание осуществляется на токарных станках, оснащаемых особыми резцами, которые называются расточными. За счёт механического воздействия снимаются поверхностные слои материала. Операция схожа со сверлением, так как тоже предполагает использование рабочего режущего инструмента, имеющего заострённые кромки, которые частично срезают металл. Это достигается благодаря вращению оснастки на определённой скорости.
При чистовом растачивании стали добиваются высокой точности, которая соответствует квалитетам в пределах 8-9. При этом степень шероховатости (Ra) стальных металлоизделий обычно составляет от 12,5 микрометров до 50. Для деталей из цветных металлов показатели отличаются. Для уровня точности это 6 и 7 квалитеты, а Ra – от 0,32 мкм до 12,5. При этом применяются резцы из твёрдых сплавов.
Растачиваться могут любые конические и цилиндрические отверстия, независимо от их глубины, диаметра, формы. Но важно подобрать подходящую технологию и оборудование, которое решит поставленные задачи.
Факторы, влияющие на выбор оборудования и метода
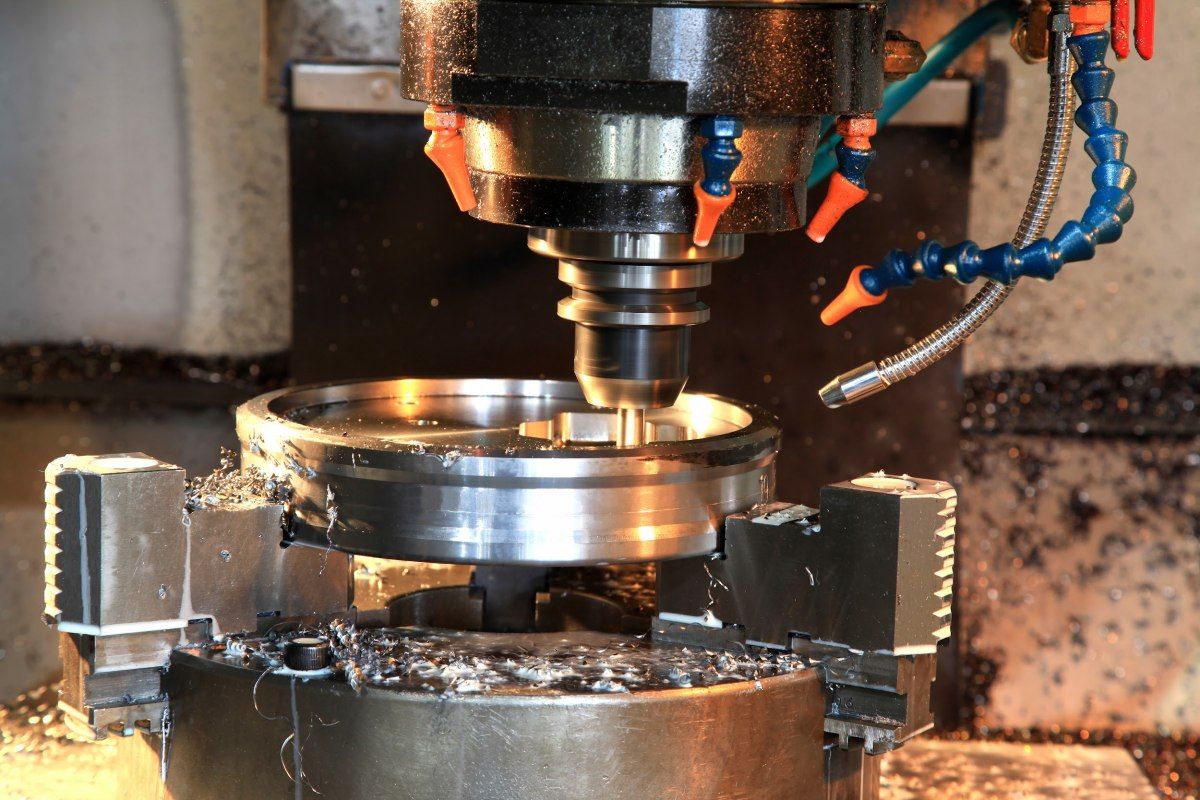
Существует различное оборудование, которое может применяться разными способами. От выбора станков, оснастки и режимов работы агрегатов зависят результаты: соответствие заданным параметрам, гладкость. Инструменты и методы их использования подбираются с учётом нескольких факторов. Главными являются:
Нужно учитывать и вид отверстий. Они бывают:
Растачивание может осуществляться в два этапа:
При выборе технологии и оборудования обязательно учитывают и свойства изделий:
При выборе станка, обрабатывающего цилиндрические отверстия, учитываются такие моменты:
При определении технологии и инструментов тщательно изучаются чертежи, техническая документация и действующие стандарты, а также характеристики детали и свойства её материала.
Виды резцов
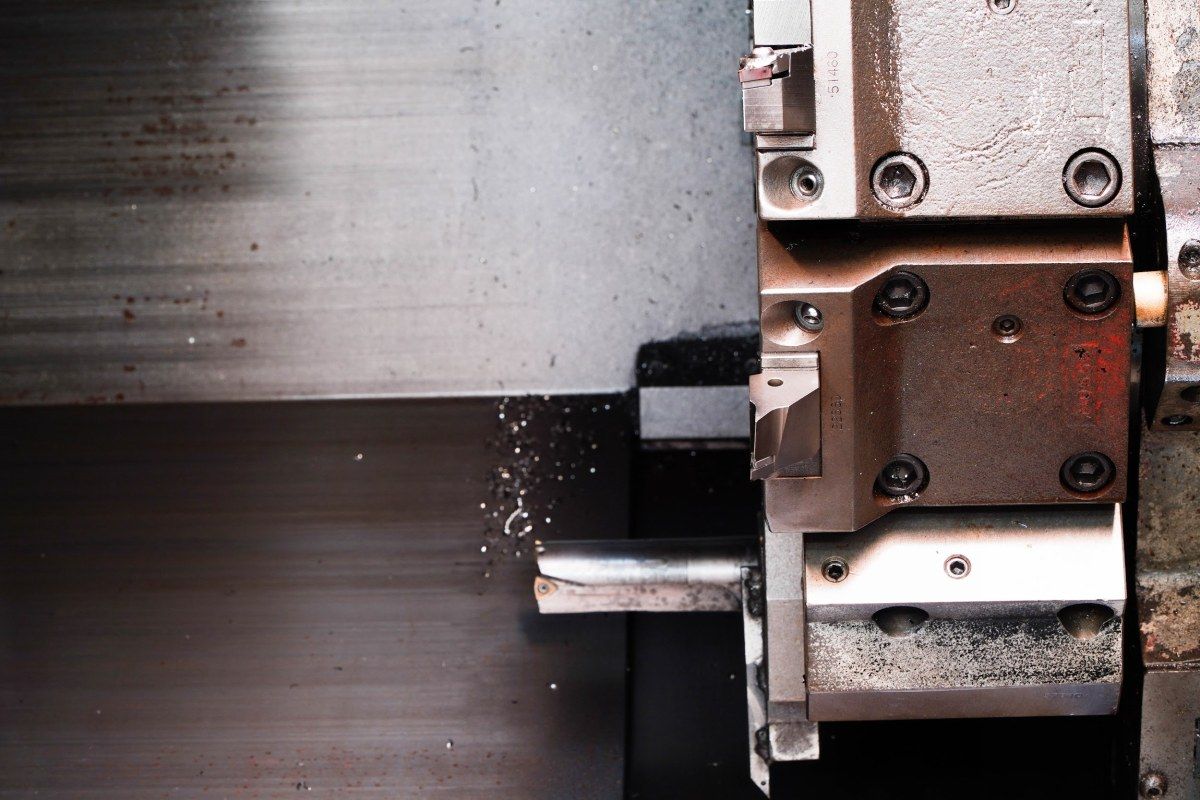
Есть разные виды расточного режущего инструмента. Так, по конструкции он может быть цельным или же составным, имеющим твердосплавные съёмные части – пластины. Также выделяют группы по назначению.
Если глубина отверстия больше трёх его диаметров, то можно пользоваться только державочными резцами, потому что жёсткость цельных обычно недостаточная. Для работ с отверстиями больших диаметров и глубины больше 3 сантиметров выбирают инструменты со сменными головками из твёрдых сплавов. Пластины в державке могут крепиться двумя способами.
Если пазы сквозные, то для них подходят резцы, которые в державке фиксируются прямо. Для глухих отверстий применяют оснастку с косым креплением. Режущая насадка в державке фиксируется с помощью лысок – опорных специальных плоскостей.
Цельные расточные резцы делятся по конструкции на два типа. Для отверстий малого диаметра, не превышающего 10 мм, применяют варианты со стержнями круглого сечения. Для диаметра до 40 миллиметров используют инструменты со стержнями прямоугольного сечения.
Стандартами предусматривается два типа исполнения. Это резцы со стандартным размещением головки и с опущенным. В последнем случае режущая кромка проходит вдоль оси, что обеспечивает повышенную жесткость. Используя такие резцы, можно выбирать стержни с удвоенными диаметрами, потому что приспособления в отверстиях могут располагаться рационально.
Резец закрепляется в хвостовике, в его держателе. Режущая кромка в норме занимает параллельное положение относительно оси вращения изделия. Вылет при этом должен быть минимальным. Вершина грани располагается на уровне с центровой осью. В некоторых случаях её немного приподнимают (всего на 0,02 диаметра), чтобы компенсировать прогиб.
Растачивание сквозных отверстий
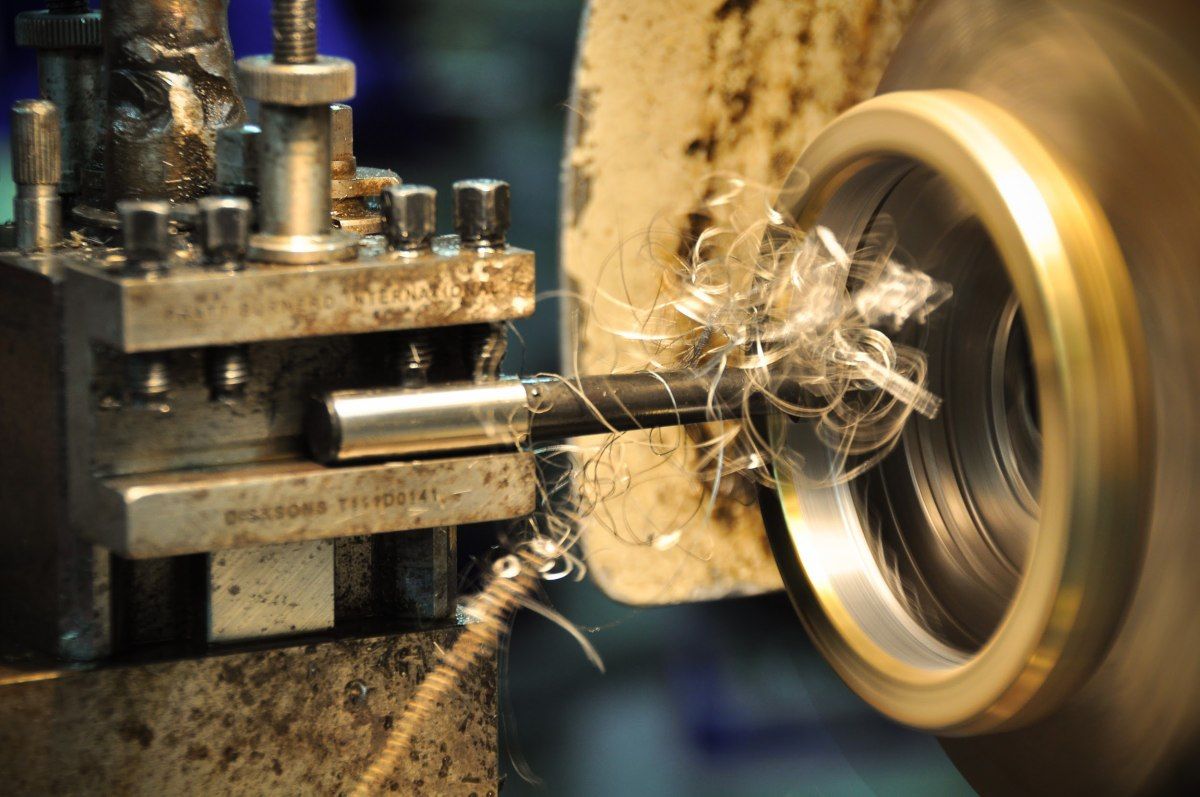
По диаметру и глубине отверстия для сквозной расточки подбирают оправки, резцы проходного типа или борштанги для фиксации на них головок или блоков инструментов. Проходные резцы имеют некоторые особенности и отличаются от оснастки для токарных станков. Их задний угол заточен таким образом, чтобы рабочая зона подходила для габаритов обработки. Передняя часть имеет вытянутую форму с сужением.
В токарном станке резец фиксируются либо в суппорте на резцедержателе (направление продольное), либо на задней бабке в оправке, оснащённой конусным хвостовиком. Если выбран специализированный расточной агрегат, то в нём рабочие инструменты крепятся в специальных оправках.
Также для растачивания сквозных отверстий подходят многолезвийные оправки, которые различаются по конструктивному исполнению. Они представляют собой длинные толстые цилиндры для крепления нескольких режущих рабочих пластин. Такой вариант дороже резцов, зато отличается высокой точностью и более значительным углублением.
Расточные штанги, называемые борштангами, используют для значительных глубин, для обработки нескольких соосных отверстий и для достижения высокой точности. Такие элементы имеют вид длинных стержней цилиндрической формы с точным диаметром в пределах 30-200 мм и длиной от 100 до 300 см. Борштанга имеет выемки (окна), расположенные по всей длине с определёнными интервалами. Они нужны для крепления режущих и контролирующих инструментов. Один край борштанги заходит в коническую оправку и помещается в шпиндель, а второй удерживается опорой или люнетом.
Растачивание глухих отверстий
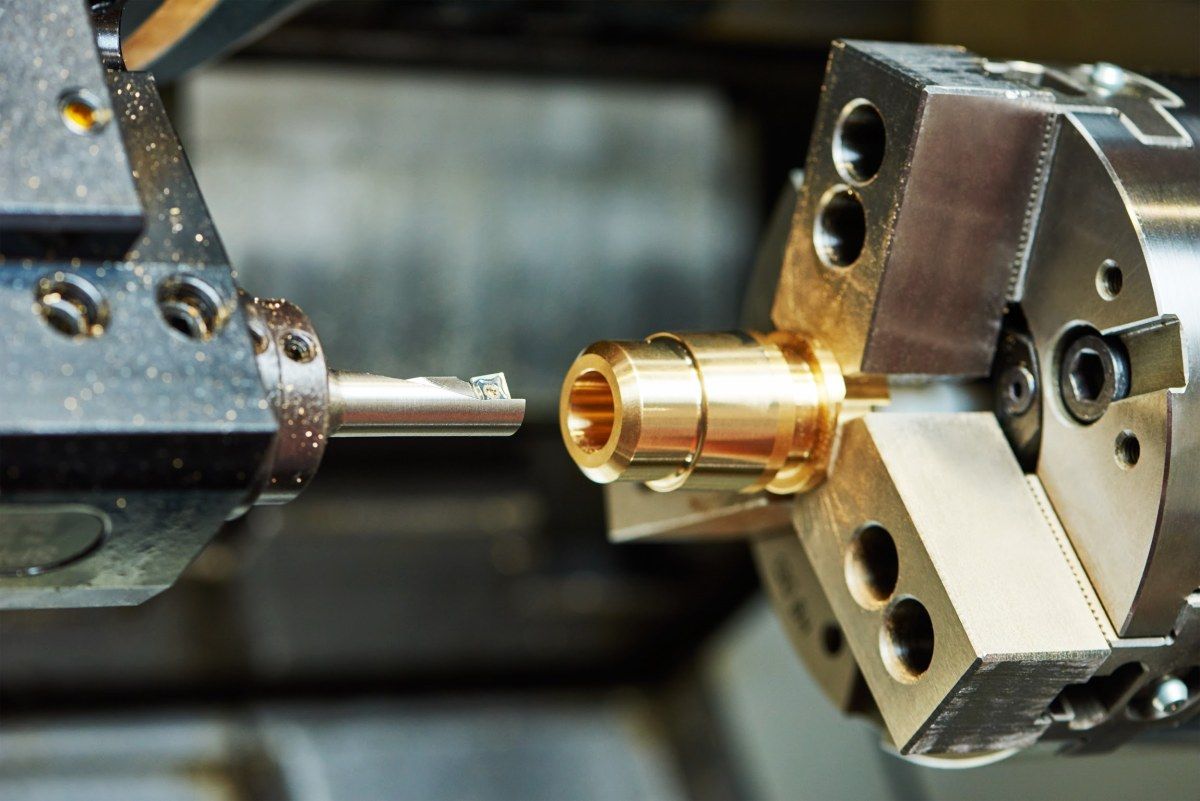
Как расточить глухое отверстие? С помощью оправки с режущими наклонными пластинами или упорного проходного резца. Но в обоих случаях мастера сталкиваются со сложностями при обработке внутренней торцевой зоны, то есть дна. В его центре остаётся незатронутый конический небольшой участок.
Чтобы добиться равномерной и полноценной обработки, соблюдают следующую последовательность действий:
При растачивании глухих отверстий важно тщательно обрабатывать зону дна. Для этого снижают подачу примерно за 5 миллиметров до конечной точки. А последний участок желательно растачивать вручную. Применение проходных резцов рационально, когда глубина не превышает 100-150 мм. В прочих случаях делают выбор в пользу расточных головок.
Технология восстановления расточкой
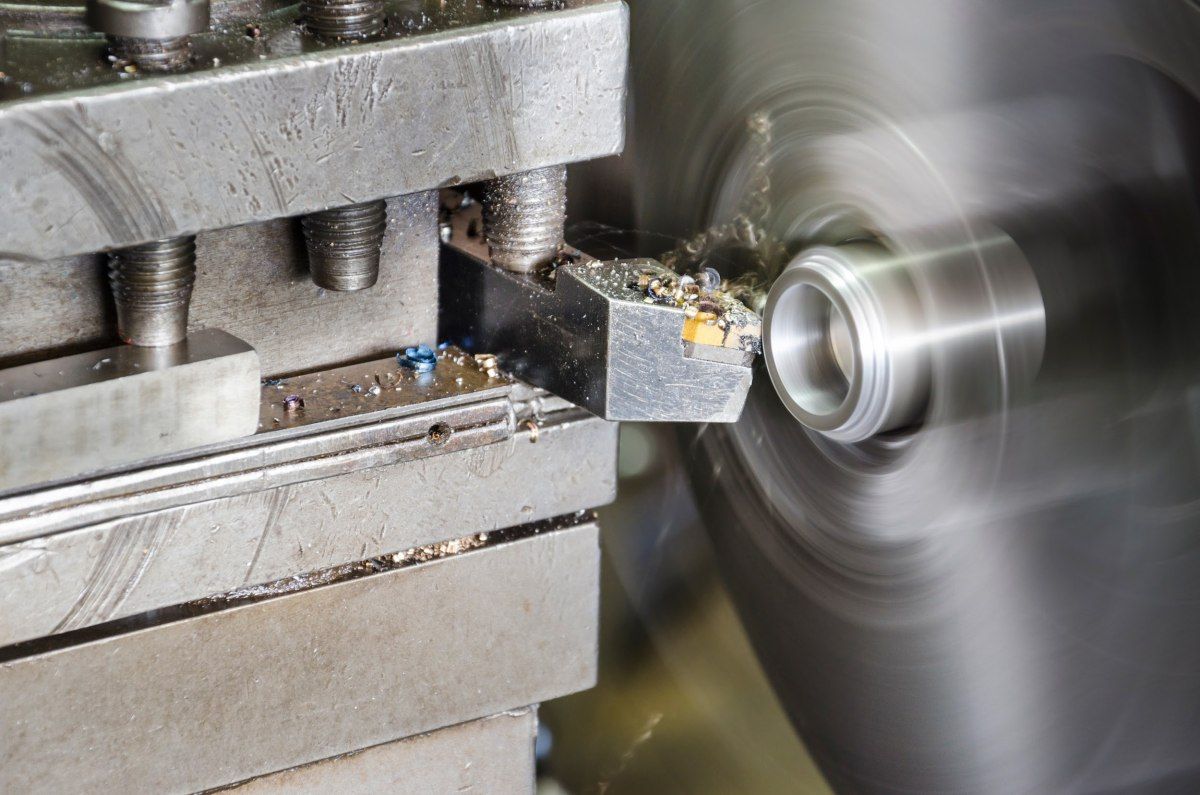
Расточить отверстие может потребоваться, чтобы восстановить его после интенсивной эксплуатации, приведшей к износу. Для этого применяют стационарные горизонтальные и вертикальные станки (расточные либо токарные), а также мобильные агрегаты.
Токарное оборудование используют, когда нужно точно восстановить соосные отверстия. Для крупногабаритных изделий и для высокой точности подходят расточные станы. Для обработки блоков цилиндров, входящих в механизм двигателей внутреннего сгорания, применяют вертикальные установки.
Мобильные приборы незаменимы, если технику невозможно транспортировать до обрабатывающего предприятия. Такие устройства состоят из мотора, оснащённой резцами расточной штанги, шпинделя и опорных деталей. Установка крепится прямо на ремонтируемом объекте, например, запорной арматуре или фланцах трубопровода, проушинах экскаваторных ковшей. Качество достигается за счёт соосного надёжного закрепления борштанги.
При восстановлении диаметр незначительно увеличивается, обычно на несколько миллиметров. Если речь идёт о блоке цилиндров ДВС, то устанавливаются подходящие по диаметру ремонтные поршни. В других ситуациях отверстия подготавливают, наращивая слой лужением, напылением или сваркой. Далее начинают расточку.
Восстановление отверстий наплавкой
Для сужения восстанавливаемого отверстия в различной технике исходный диаметр предварительно наращивается наплавкой. При ней на поверхность наносится слой металла. Для этого применяют лужение, сварку или напыление. А когда достигают нужного размера, переходят к расточке, чтобы получить заданный диаметр. Некоторые предприятия используют многофункциональные расточно-наплавочные комплексы.
Дефекты при растачивании
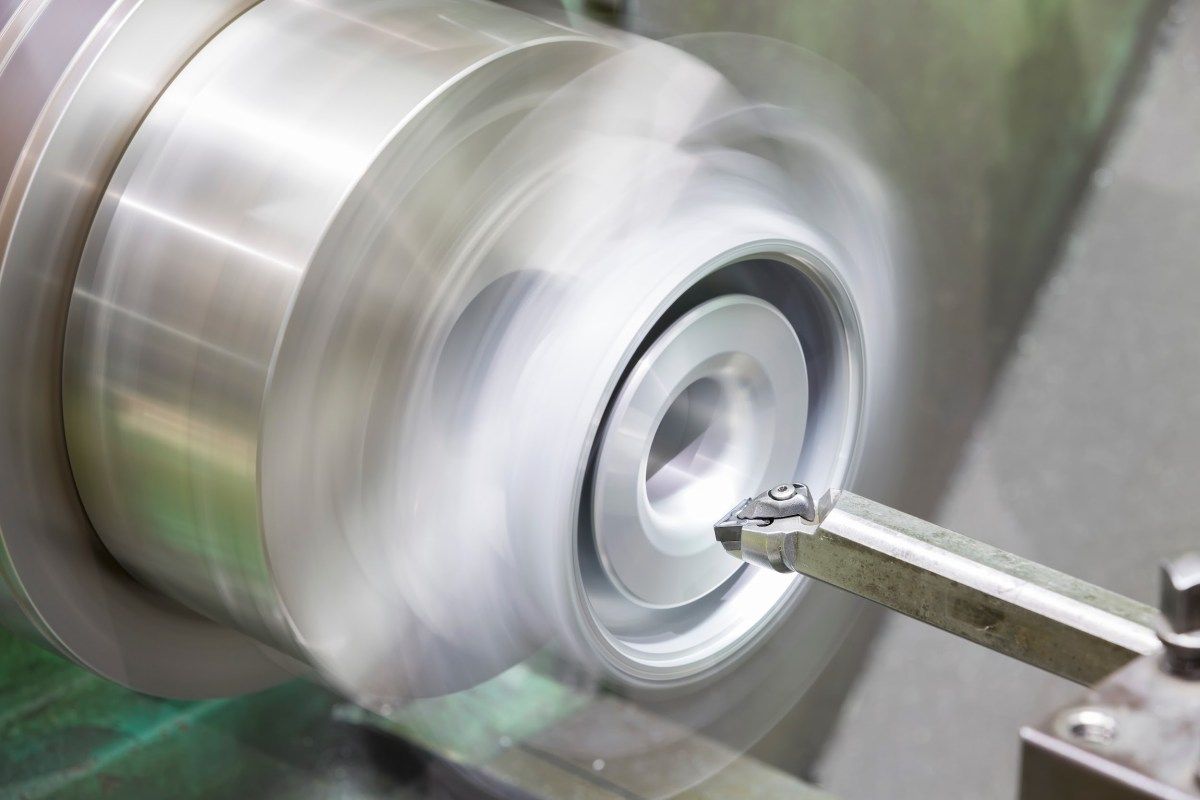
Вероятны такие дефекты:
Заключение
От качества расточки зависят характеристики деталей с отверстиями, поэтому доверять такую операцию следует только профессионалам. Компания Profbau предлагает различные виды металлообработки, в том числе растачивание.
Мы выполняем заказы любых объёмов и любой сложности оперативно, профессионально и по невысокой цене благодаря высокой квалификации сотрудников, использованию автоматизированного современного оборудования и строгому соблюдению технологий. Для получения информации о сотрудничестве позвоните или напишите нам.