Многие столетия люди работают с металлами. Большинство материалов – прочные и твердые, требующие приложения усилий для изменения размера и формы. Для обработки металла используют разные станки и характерные приемы.
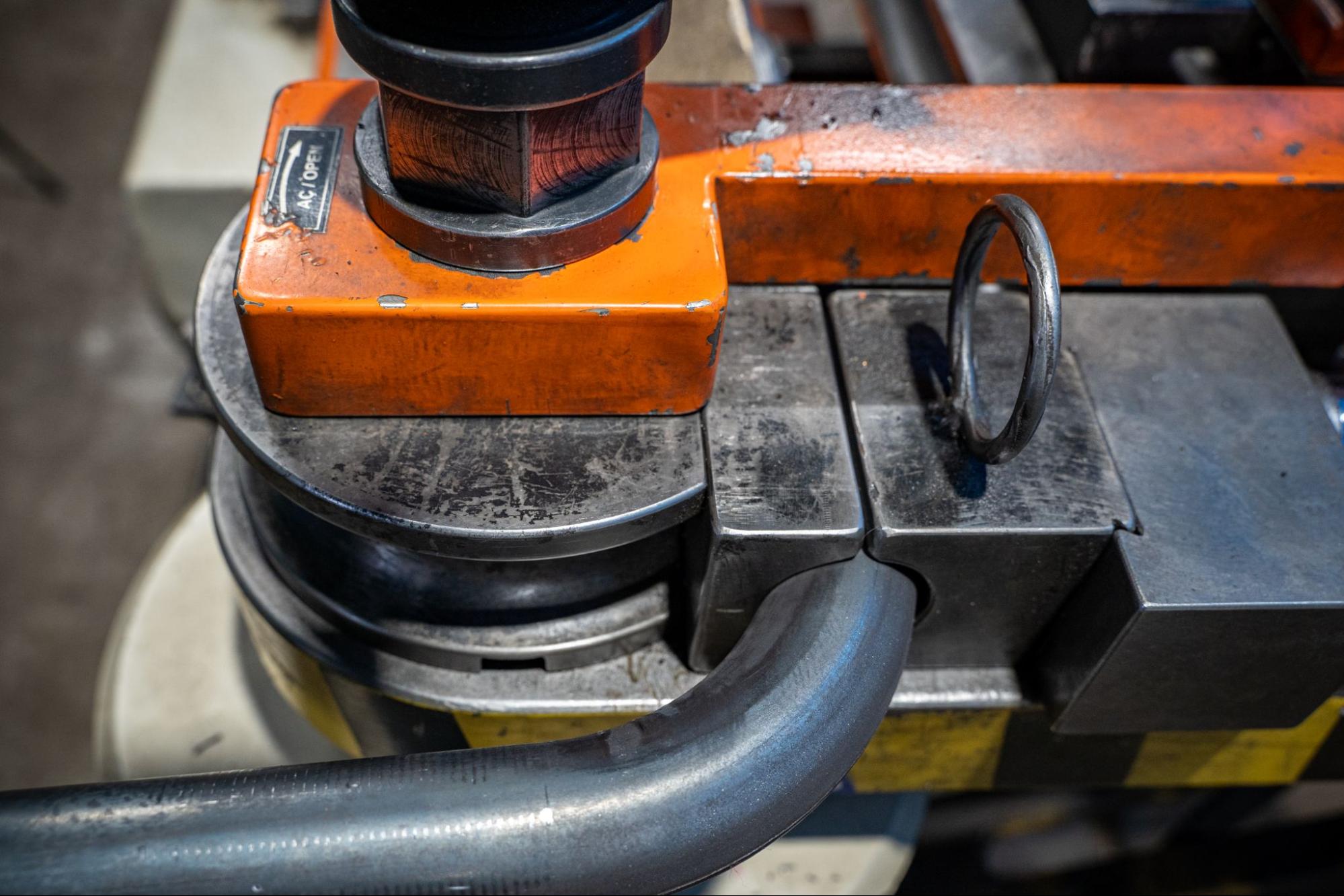
Что такое металлообработка и для чего это нужно?
Обработка металла – технологический процесс, смысл которого заключается в физическом воздействии на материал: меняются характеристики, физические и механические свойства и размеры. Благодаря такому взаимодействию удается получить готовые детали.
Основные виды обработки
Принципы металлообработки важно знать и профессиональным литейщикам, и неопытным мастерам. Знания о том, как реагируют материалы на тот или иной способ, помогают избежать ошибок во время технологического процесса.
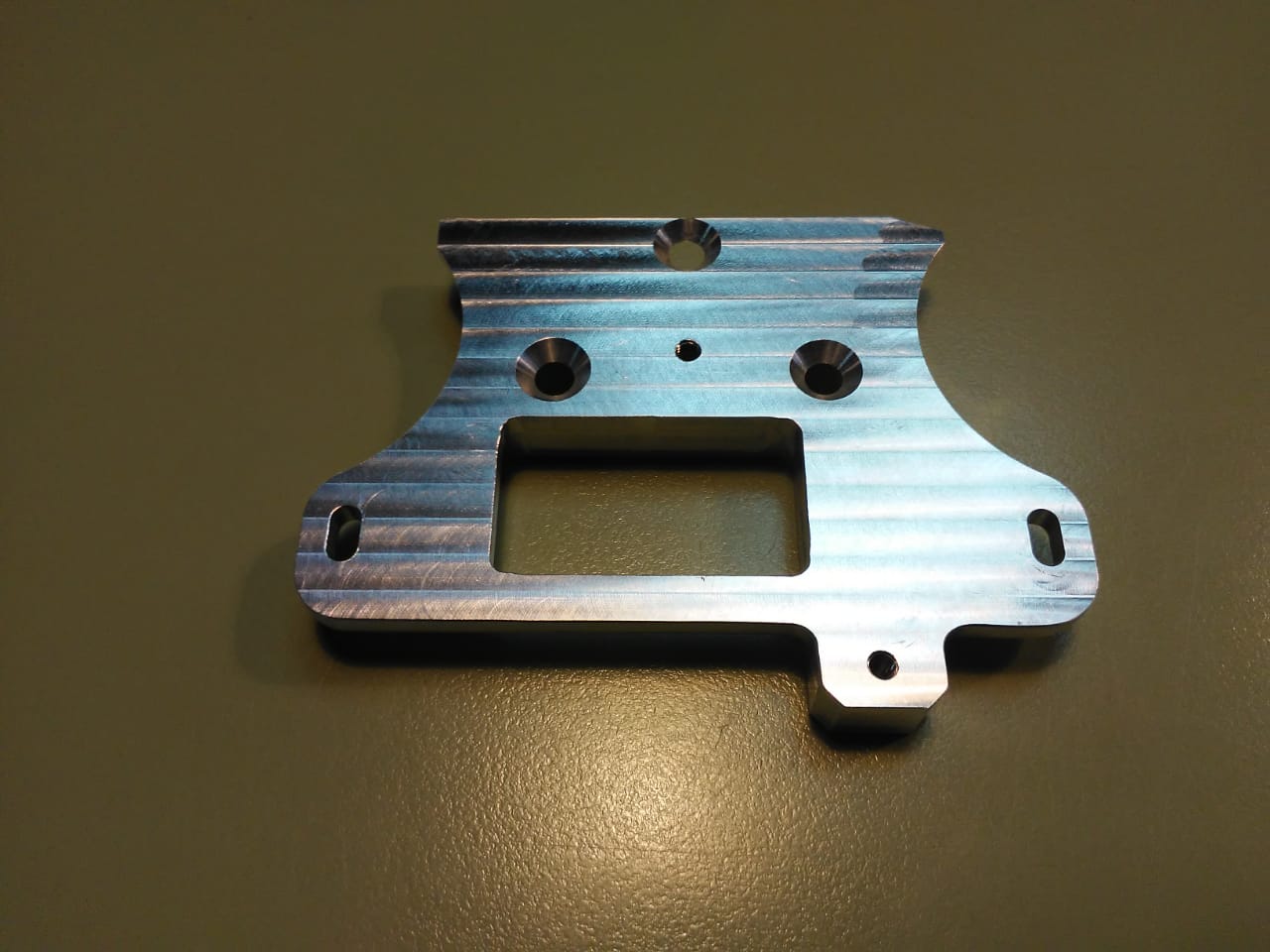
Есть несколько направлений:
- Механическая – широкая группа различных методик работы с заготовками при помощи профессионального прибора;
- Работа с давлением. Устройства, создающие давление, позволяют менять конфигурацию заготовки без нарушения ее целостности. При взаимодействии с твердыми сплавами следует сначала их хорошо разогреть;
- Термическая – для улучшения технических характеристик заготовки высокой температурой;
- Химическая – щелочи, кислоты и другие компоненты позволяют создать химическую реакцию;
- Электрическая – этот прием помогает сделать отверстия. Это нужно при работе с твердой сталью.
Сфера металлообработки не стоит на месте и развивается. Появляется не только инновационное оборудование, но и возникают разные эффективные технологии обработки.
От чего зависит тип взаимодействия?
На выбор приема влияют твердость сплава и ряд других особенностей. У каждого материала свои химические характеристики, что требует особого подхода. При выборе методики учитывают показатели, к которым относятся:
- Прочность при изменении точения и резания;
- Температура закалки и плавления (если необходима температура).
Выполнение определенной задачи зависит от прочности и твердости материала. Это такие задачи, как распиловка, формирование поверхности конкретной фигуры, шлифовка, штамповка. Отталкиваясь от запланированного результата, выбирают инструменты и технологию.
Механическая обработка
Это самая широкая группа металлообработки: применяется различное оборудование. В основе – снятие слоя с заготовки.
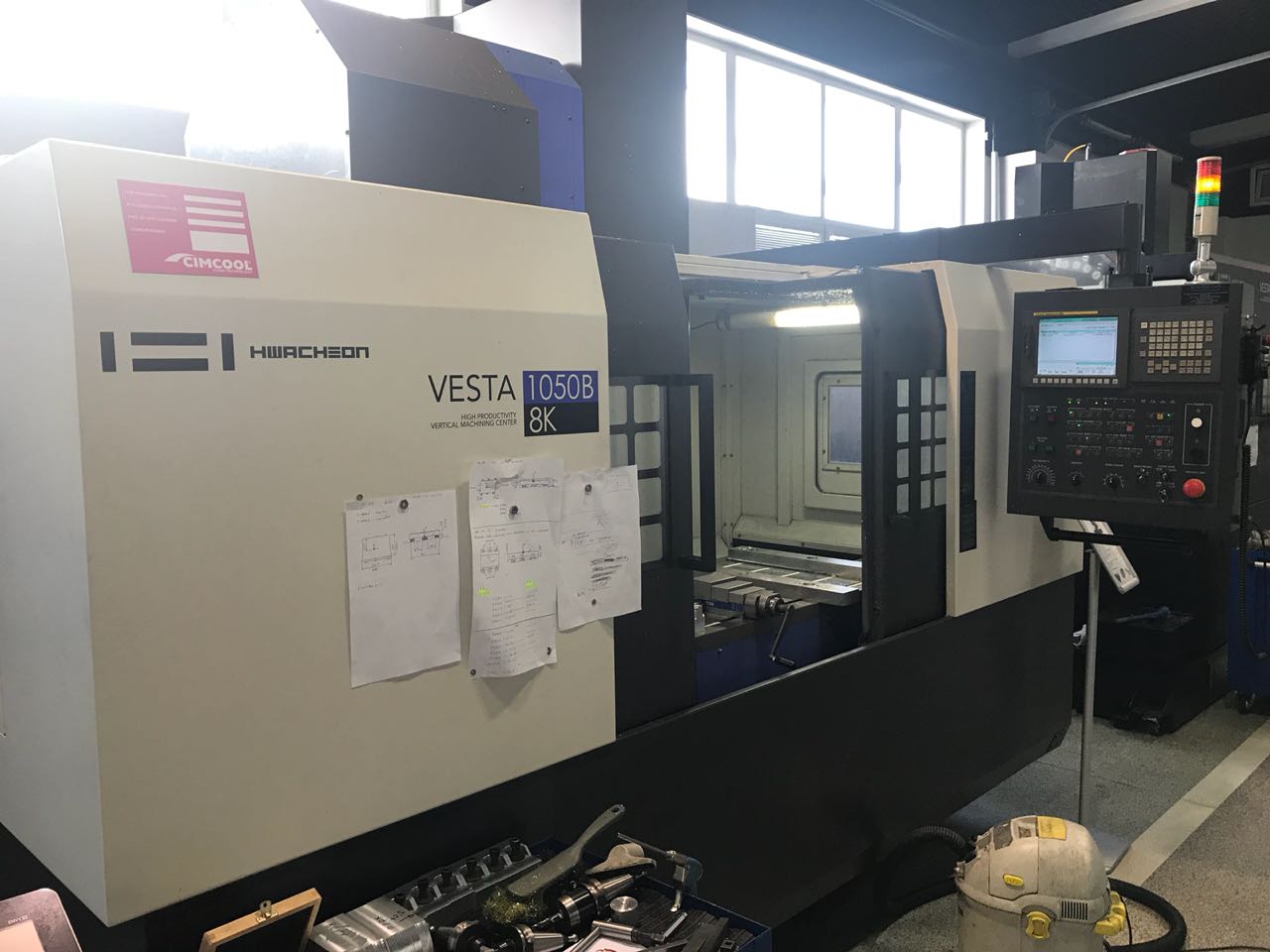
Сверление и точение
Сверление – метод обработки металла, состоящий из этапов:
- При помощи тисков и струбцин заготовку закрепляют на столе;
- В патроне закрепляют оснастку для создания резьбы;
- После запуска электрического двигателя шпиндель выкручивает патрон, за счет оснастки в заготовке образуется отверстие оптимального диаметра.
Поскольку сверла выдерживают различные нагрузки, при выборе оснастки ориентируются на свойства обрабатываемого сплава.
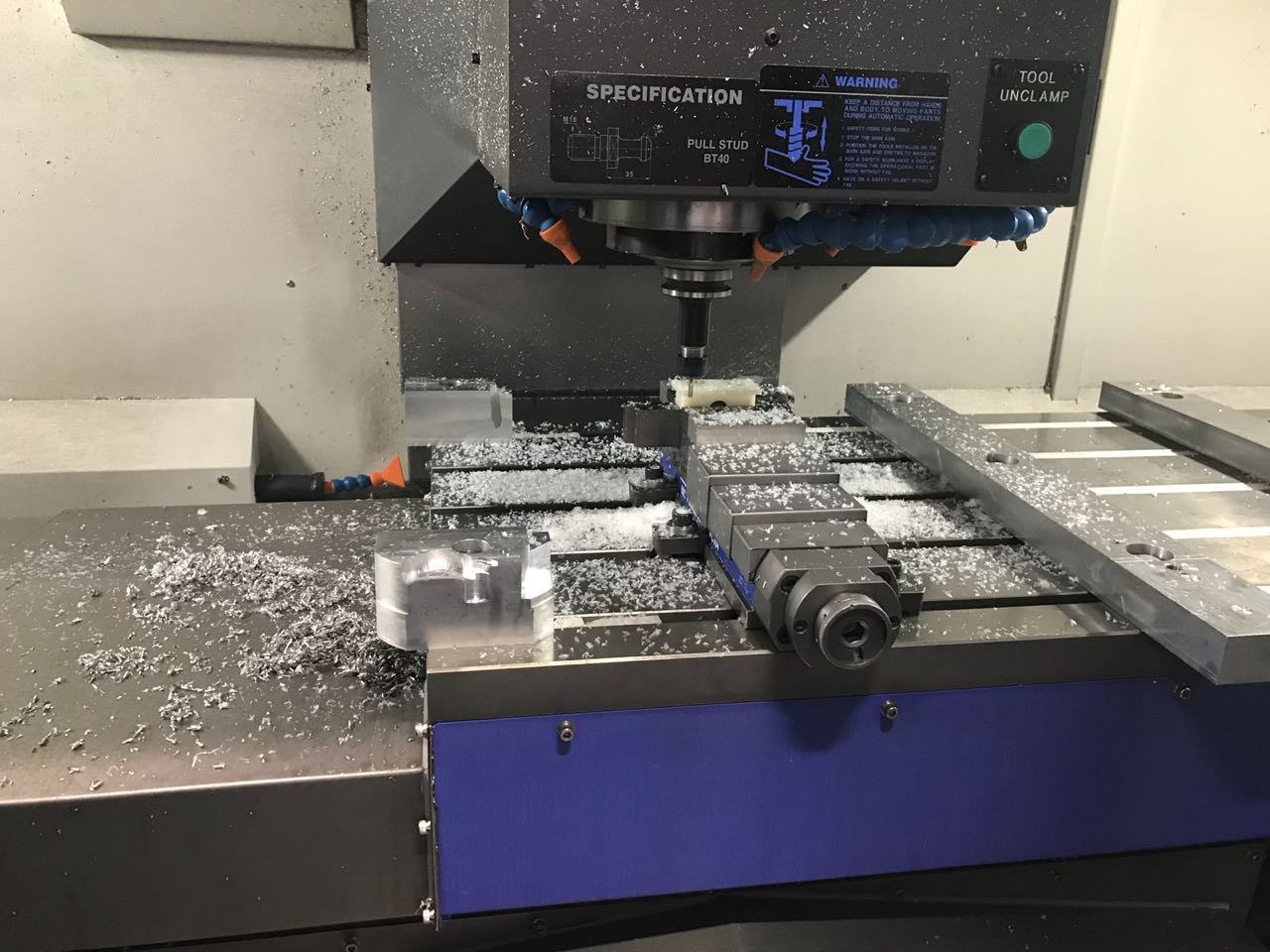
Не менее распространенный тип обработки – точение. Такой технологический процесс позволяет создавать заготовки в виде конуса или цилиндра. Технология такова:
- Закрепляют изделие в подвижном шпинделе;
- Включается двигатель, выкручивается элемент;
- Мастер при помощи резцов снимает слой.
При взаимодействии с токарными ЧПУ используют стандартный принцип работы с типами сверления. Такая методика позволяет сделать резьбу и изменить конфигурации изделия при помощи различных резцов. Чтобы не отравиться, мастера надевают защитные очки.
Шлифование и фрезерование
Один из популярнейших типов – фрезерование: он немного схож со сверлением. Фреза позволяет создать резьбу и углубления в поверхностях, обработать торцы элементов, во время вращения шпинделя снимается верхний слой.
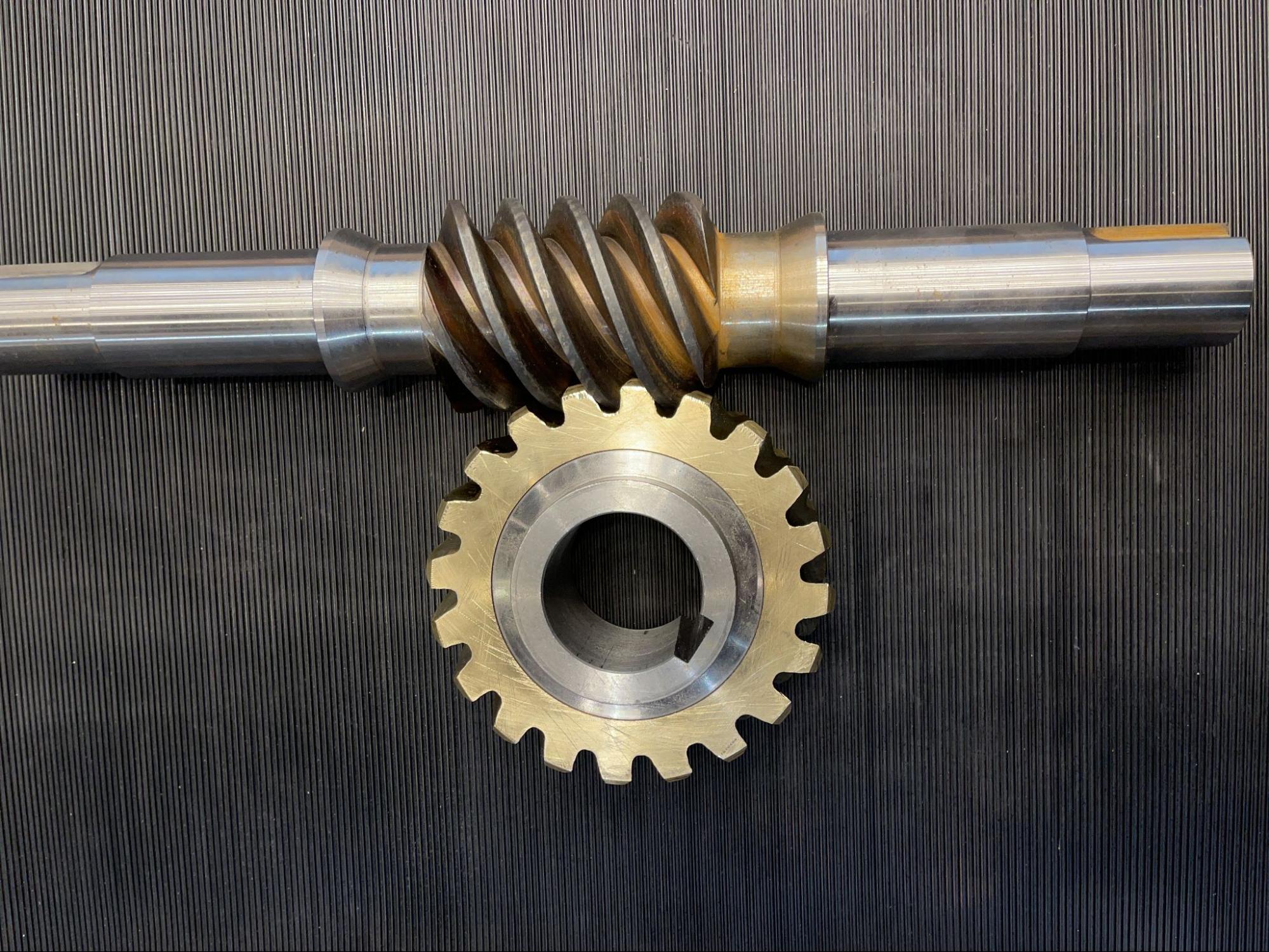
При обработке используют и абразивные материалы – метод шлифования: на подвижном валу фиксируют круг с напылением, электродвигатель ослабляет конструкцию. Тип работы зависит от абразива:
- Небольшая фракция предназначена для заключительных работ;
- Круги с большими частицами созданы для очищения поверхности от ржавчины.
Токарная обработка
С детали снимают тонкие слои, пока она не достигнет конкретной шероховатости. Для работы используют режущие инструменты и станки. Этот тип схож с расклиниванием слоя острой кромкой инструмента. За счет механического усилия она врезается в изделие, снимая припуск, превращающийся в стружку.
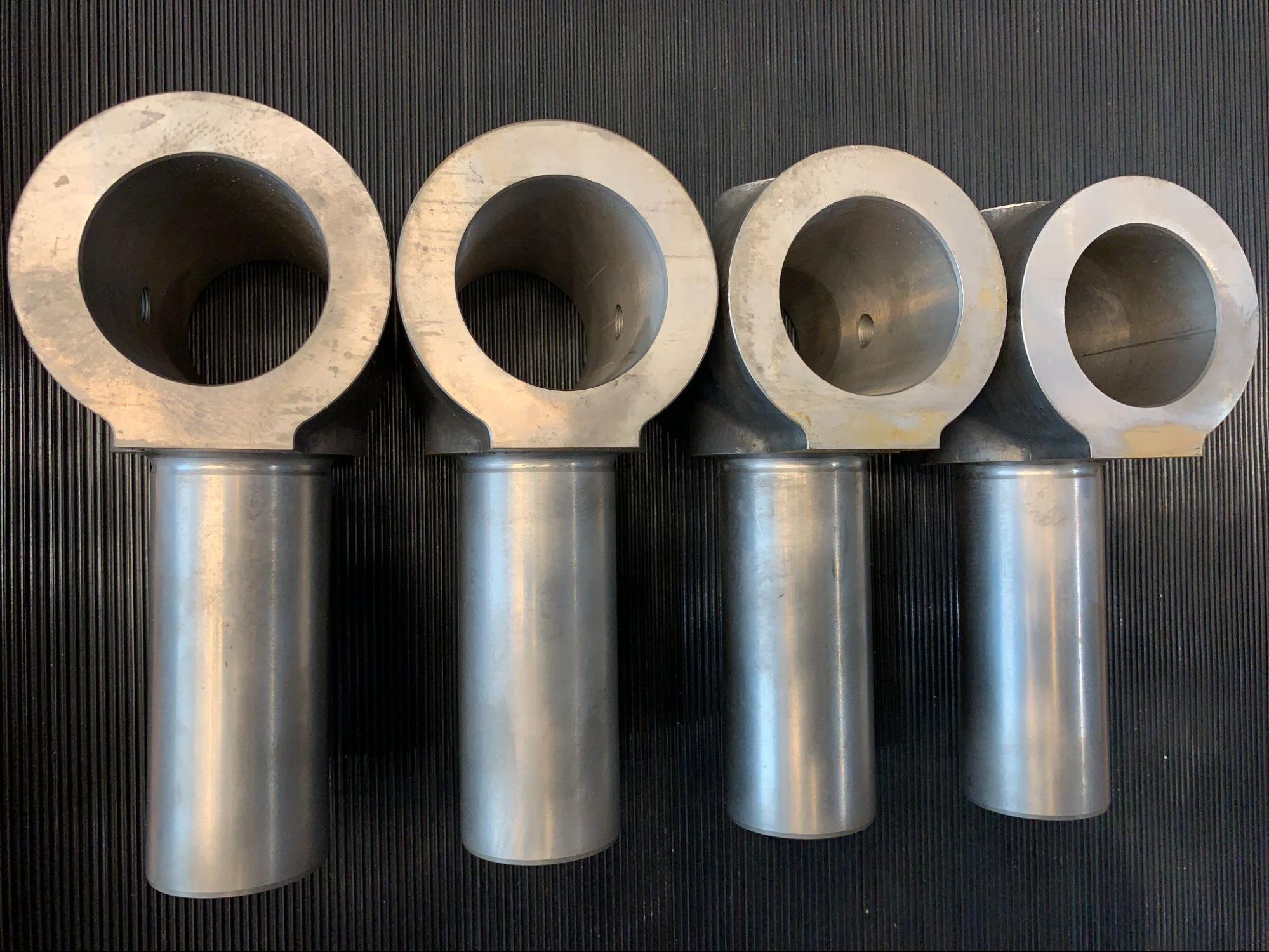
Повышенная скорость резки и непрерывность процесса позволяют сделать результат работы еще более качественным. Важный момент: скорость резки подбирается индивидуально. С помощью токарного инструмента изготавливают валы, втулки, гайки, зубчатые колеса, кольца, муфты, шкивы.
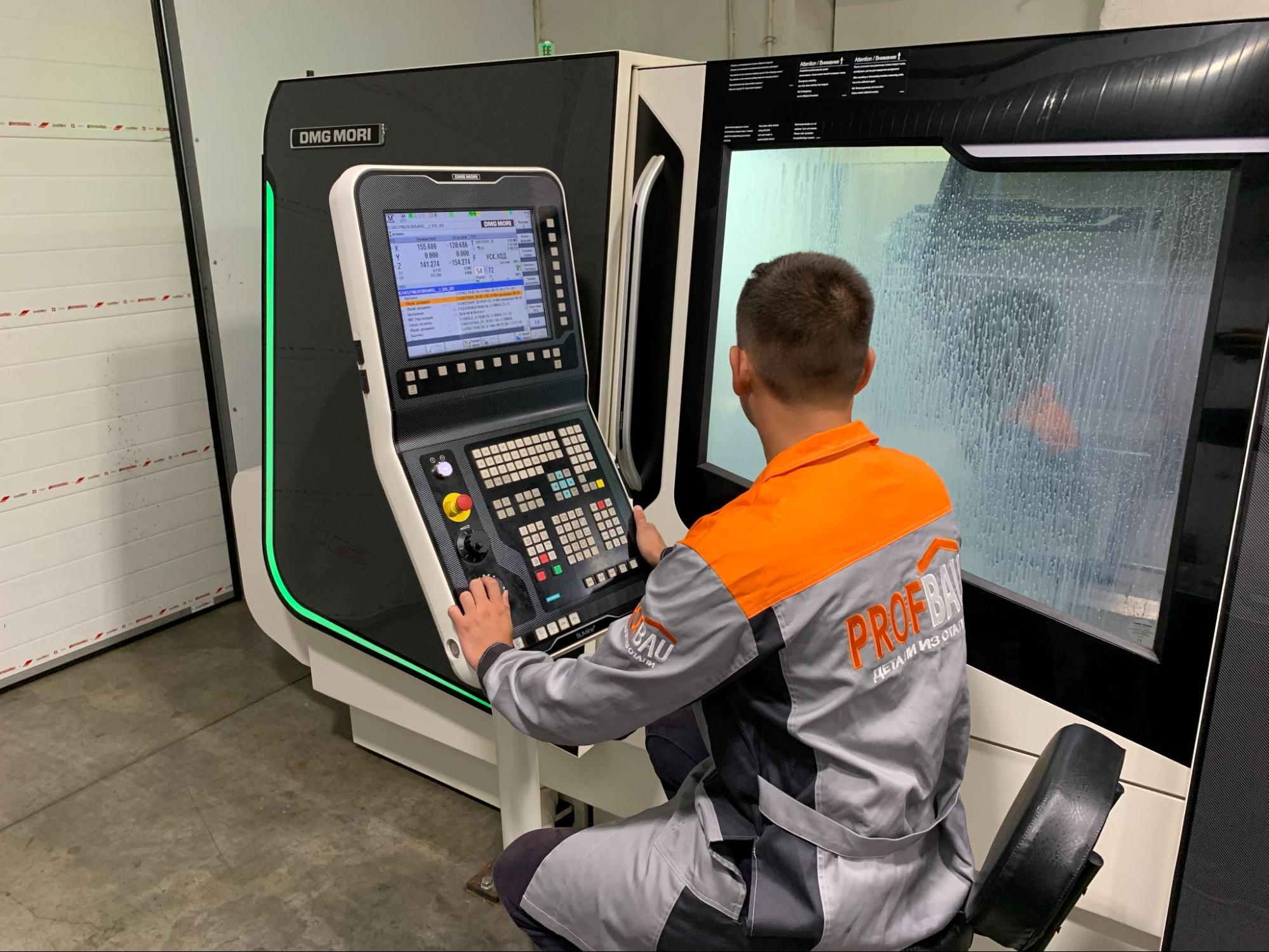
Обработка давлением
К этому типу люди прибегают уже не первое тысячелетие. Современные технологии сильно отличаются от старинных методик, но суть все та же: за счет давления или физической силы меняется размер изделия.
Среди основных методов данной группы:
- Горячая прокатка – для изготовления листового, сортового, трубного, фасонного проката. В дальнейшем такие заготовки подвергаются и холодному деформированию.
- Штамповка – один из самых старинных способов. Из-за минимальных затрат и простоты производства с его помощью на протяжении нескольких столетий создавали посуду. Штамповка бывает объемной и листовой. Объемная штамповка – это пространственное изменение конфигурации объемного элемента: из простых (кубы, параллелепипеды, цилиндры, шары) получают сложные изделия. С помощью листовой штамповки удается изготовить детали разных размеров: от корпусов транспорта до минимальных изделий.
- Холодная прокатка – методика помогает улучшить свойства горячекатаных элементов: повысить качество поверхности и добиться максимально точных размеров.
- Волочение – протягивание элемента через отверстие оптимальной конфигурации. Такой способ дает возможность задать поперечное сечение проката. В этом случае важно, что площадь сечения отверстия меньше аналогичных показателей изделия. С помощью методики создают прутки в виде квадрата, круга, многоугольника, тонкостенные трубы малого диаметра, фасонный прокат с минимальным сечением.
- Ковка – механизированный или ручной способ, заготовка в этом случае требует нагрева. К ручному методу прибегают, если изготавливают декоративные детали.
- Комбинированная обработка – использование сразу нескольких подходов, позволяющих достичь нужного результата.
- Горячее и холодное прессование. Технологию называют экструдированием. С ее помощью получают длинномерные профильные детали: заготовку выдавливают через каналы. Этот способ позволяет обрабатывать цветные мягкие сплавы (Cu и Al) и сплавы на их базе: можно отказаться от дополнительного нагрева.
Обработка металлов сваркой
Для соединения деталей в массовом и мелкосерийном производстве применяют сварку. При этом заготовки можно соединять углами, торцами, внахлест: предполагается нагрев материала до появления кромок или до температуры пластичности. Уже потом элементы соединяют в монолитную конструкцию. Существует три основных вида:
- Газовый – перед резкой или сваркой сталь нагревают газовой горелкой.
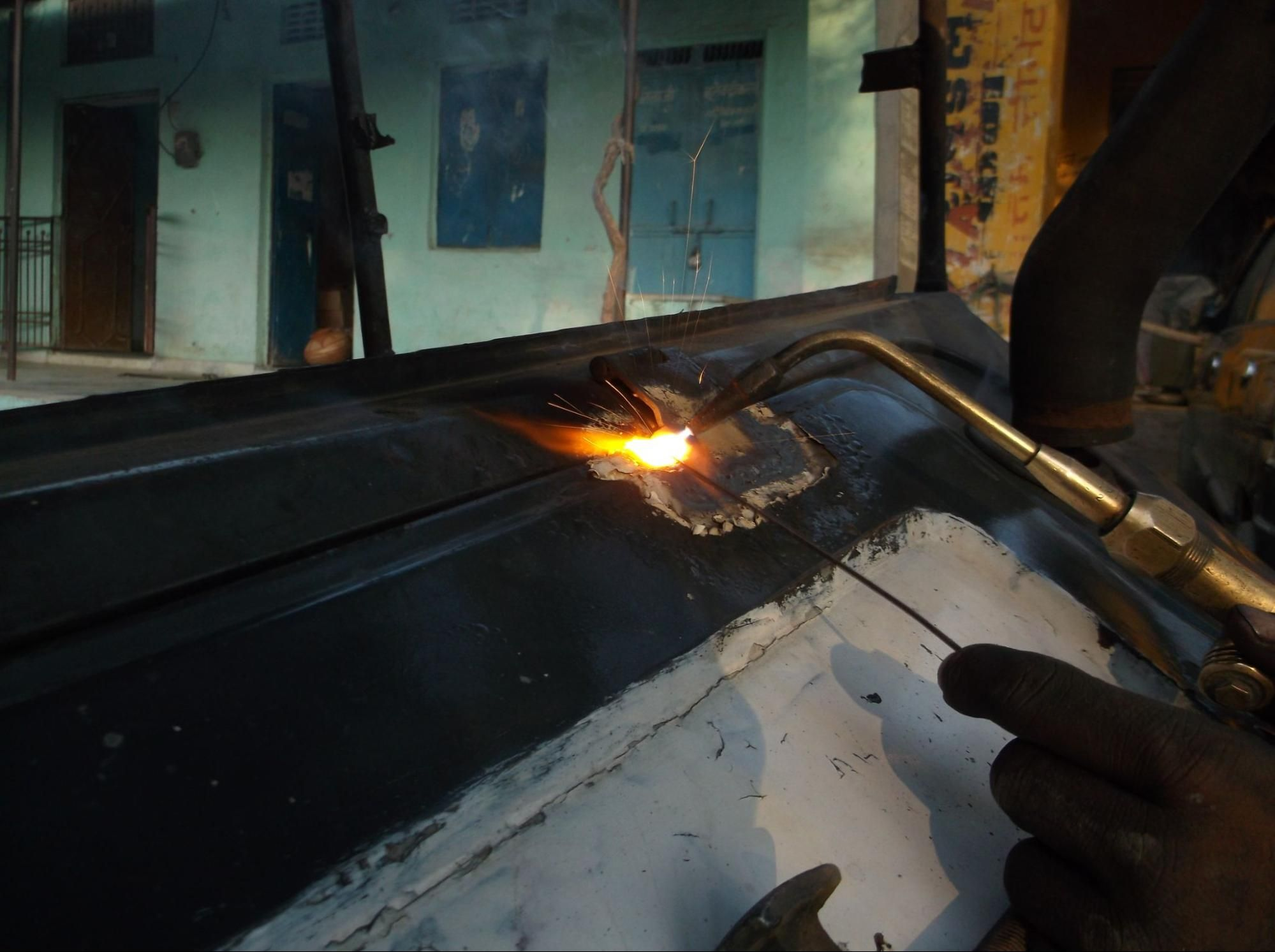
- Химический – температура повышается за счет химической реакции. Если нельзя использовать газовый баллон или электрическое оборудование, прибегают к этому виду.
- Электрическая сварка – самый популярный метод, с помощью которого сначала нагревают, а затем плавят материал для последующего соединения.
Последняя группа подразделяется еще на два вида:
- Контактная – бывает роликовая и точечная. В основе – нагревание электрическим током. При роликовом методе по поверхности стыка создают сплошной шов, при точечном детали соединяют в конкретных точках.
- Дуговая – использование тепла электродуги. Для работы используют электроды (среда инертных газов) и сварочное оборудование.
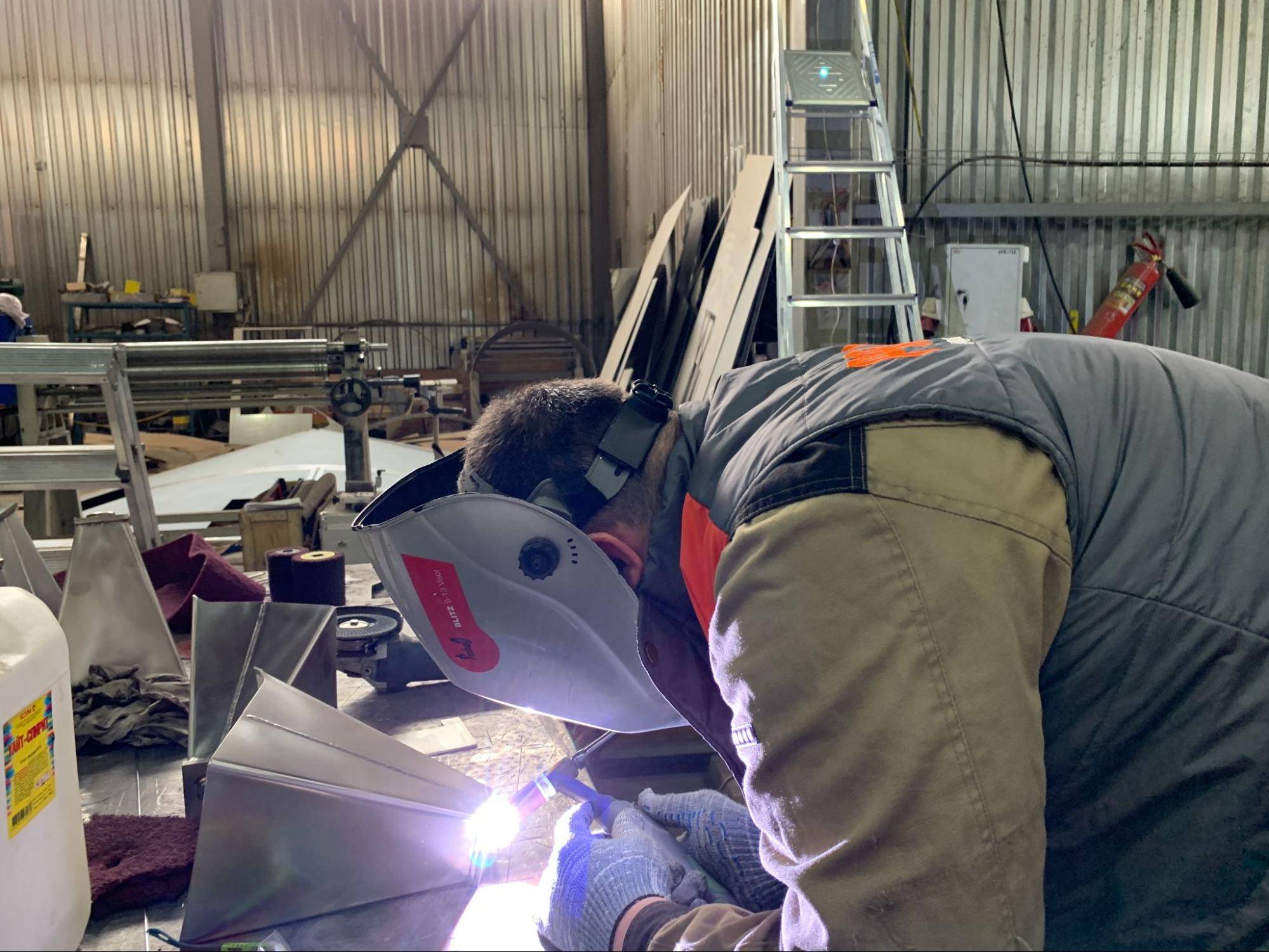
При помощи этой методики изготавливают кузова для машин и соединяют компоненты строительных конструкций и трубопроводов. Важно и то, что сварка совместима с другими методами.
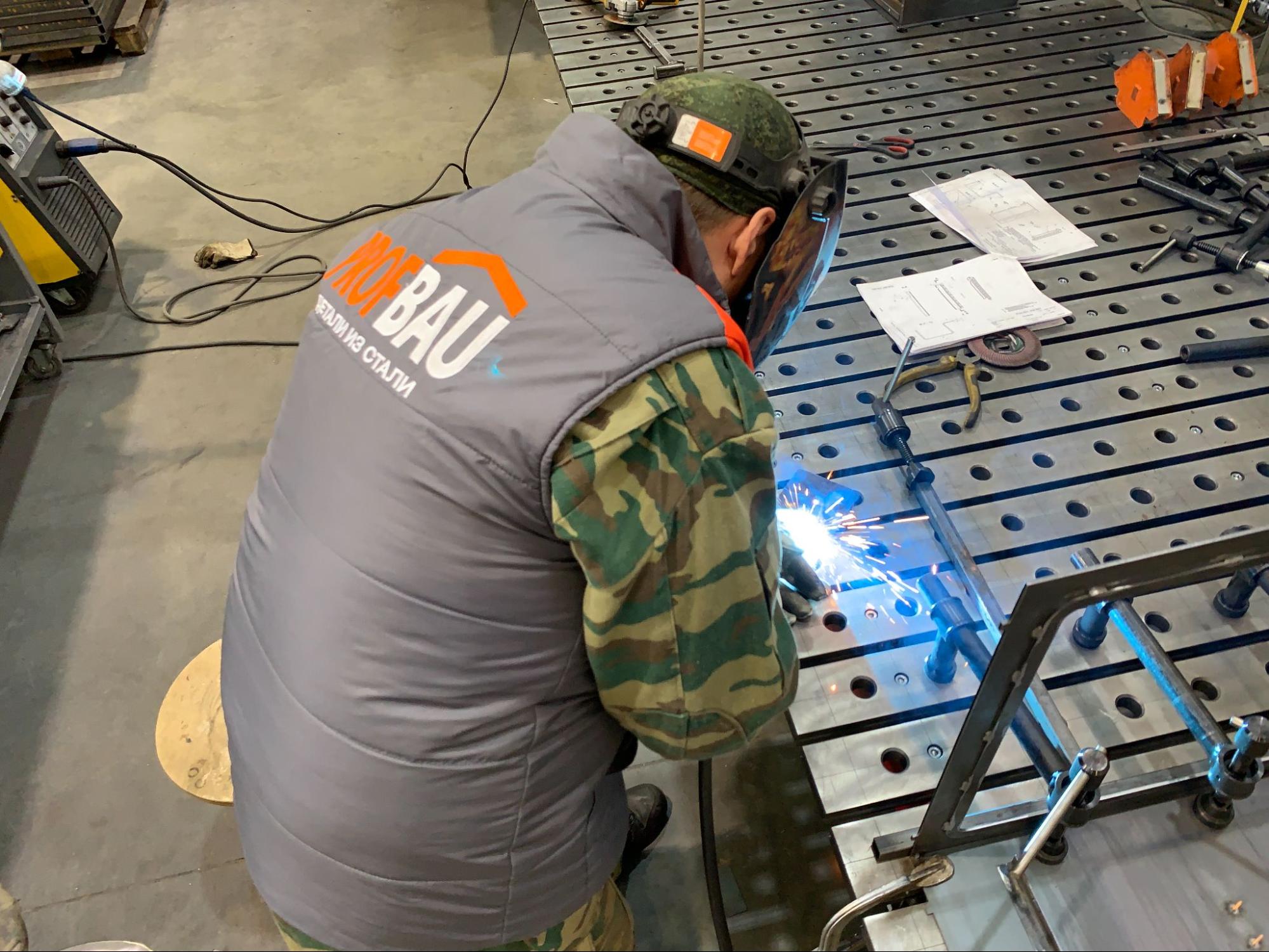
Технология литья
Работа с металлом сильно отличается от взаимодействия с другими сплавами. Например, для затвердевания воска, цемента достаточно комнатной температуры, тогда как олово плавится при температуре +231 градус, а железо при +1531 градусе. Поэтому потребуется не просто костер, но и печи, специальное топливо.
Для тугоплавких сплавов потребуется емкость из глины. Исключение – титан: литье производится в прочных формах. После заливки модель застывает, одноразовые матрицы ломают, а многоразовые разбирают. Теперь можно переходить к механической работе с отливом: иногда изделие бывает уже готово к эксплуатации.
Для литья подходят металлы:
- Черные – это 90 % имеющихся сплавов. Их используют для производства автомобильных деталей, техники, оборудования, станков, конструкций для строительства.
- Цветные легкие – Al, Mg, Ti. Это более дорогие виды, поскольку в природе встречаются редко. Цветные материалы используют в сферах, где необходимо снизить вес детали. Это аэрокосмическая промышленность, вычислительная техника, смартфоны, бытовые приборы, высокотехнологичное вооружение.
- Благородные – Au, Pt, Ag, Ir, Os, Pd, Rh, Ru. В доисторические времена первые три варианта использовались в качестве валюты, ритуальных принадлежностей, ювелирных украшений. Сегодня они также считаются отличным вложением капитала. Но из-за уникальных физических свойств их используют в медицине.
- Цветные тяжелые – Zn, Pb, Sn, Ni, Cu. Подходят для сфер, где нужны упругие и прочные сплавы, устойчивые к коррозии – электроника, электроматериалы, транспорт, химическая промышленность.
Выделяют несколько видов литья:
- Традиционный. Форму из стали или песка под действием силы тяжести наполняют материалом. Но у этой методики есть несколько недостатков: не отвечает современным требованиям, тяжелые условия труда, высокая трудоемкость.
- Под низким давлением. Формы для отливок и тигли помещают в герметичную камеру. Провод опускают в расплавленный металл: в камере должен быть низкий уровень инертного газа и давление воздуха. При максимальной скорости потока сталь попадает в матрицу, форма полностью, но аккуратно и равномерно заполняется. Этот способ позволяет получить качественные тонкостенные отливки. У методики есть немало преимуществ: автоматизированная система, хорошие условия труда, минимальные энергозатраты, экологичность, качественные поверхности.
- Инжекционное. Основное отличие состоит в том, что сплав попадает в стальную матрицу в состоянии порошка. Из-за повышенной текучести смесь заполняет любые формы и внутренние полости. Главное преимущество – высокоточная поверхность, поэтому можно отказаться от дополнительных манипуляций. Немаловажный плюс – физическая и химическая однородность изделия.
- Под давлением. Метод используют в цветной и черной металлургии для создания однородных отливок. На скорости 120 км/час сплав попадает и заполняет матрицу, финишная обработка не нужна. Методика позволяет отливать детали любой конфигурации – с резьбой, отверстиями, разными стенками.
- В землю. Стандартный тип обработки. Для него создают деревянную модель: из глины и песка делают матрицу. Для обеспечения газоотведения ее накалывают иглами, а после ждут остывания.
- В формы. Кокиль и разъемную форму создают из металлических частей. Если нужна точная передача размера и качественная поверхность, используют метод фрезерования или отлива. После покрытия емкости антипригарными составами проводят заливку. После остывания стали разбирают кокили, достают и очищают отливки. Такой матрицы хватит на 300 циклов.
- По газифицируемым видам. Материалом в этом случае выступает газифицируемый и легкоплавкий полистирол. При заливке модель оставляют в форме, а затем она испаряется. Методика дает возможность снизить трудоемкость моделирования, сделать непростые отливки, из матрицы модели можно не убирать. Эту методику обычно используют на металлургических заводах.
Резка металлов
Метод резки подходит для работы со сплошными, полыми элементами, металлическими листами. Если резать напрямую, будет достаточно ручных ножниц. Для фигурных процедур потребуются технологичные станки с ЧПУ.

Для резки используются:
- Болгарка – это для домашних работ;
- Гильотина – станок, в котором под давлением и на высокой скорости лезвие опускается на рабочую зону;
- Кислородная обработка – сплавы с минимальным содержанием легирующих элементов, оставшуюся оксидную пленку удаляют;
- Лазерная – температура воздействует на конкретное место распиловки, это самый прогрессивный и точный способ;
- Плазменная – наиболее точный метод: излишки вещества в месте плавления испаряются, и остаются чистые кромки;
- Ленточнопильный аппарат – за счет получения ровных кромок и разнообразных возможностей этот вариант считается одним из наиболее оптимальных;
- Циркулярная пила – большая трудозатратность и невысокая точность, но для дома подойдет.
Резку проводят на токарном устройстве. В зависимости от оборудования разнятся и режимы резания. Обычно это зубонарезка, сверление, точение, фрезеровка, шлифовка.
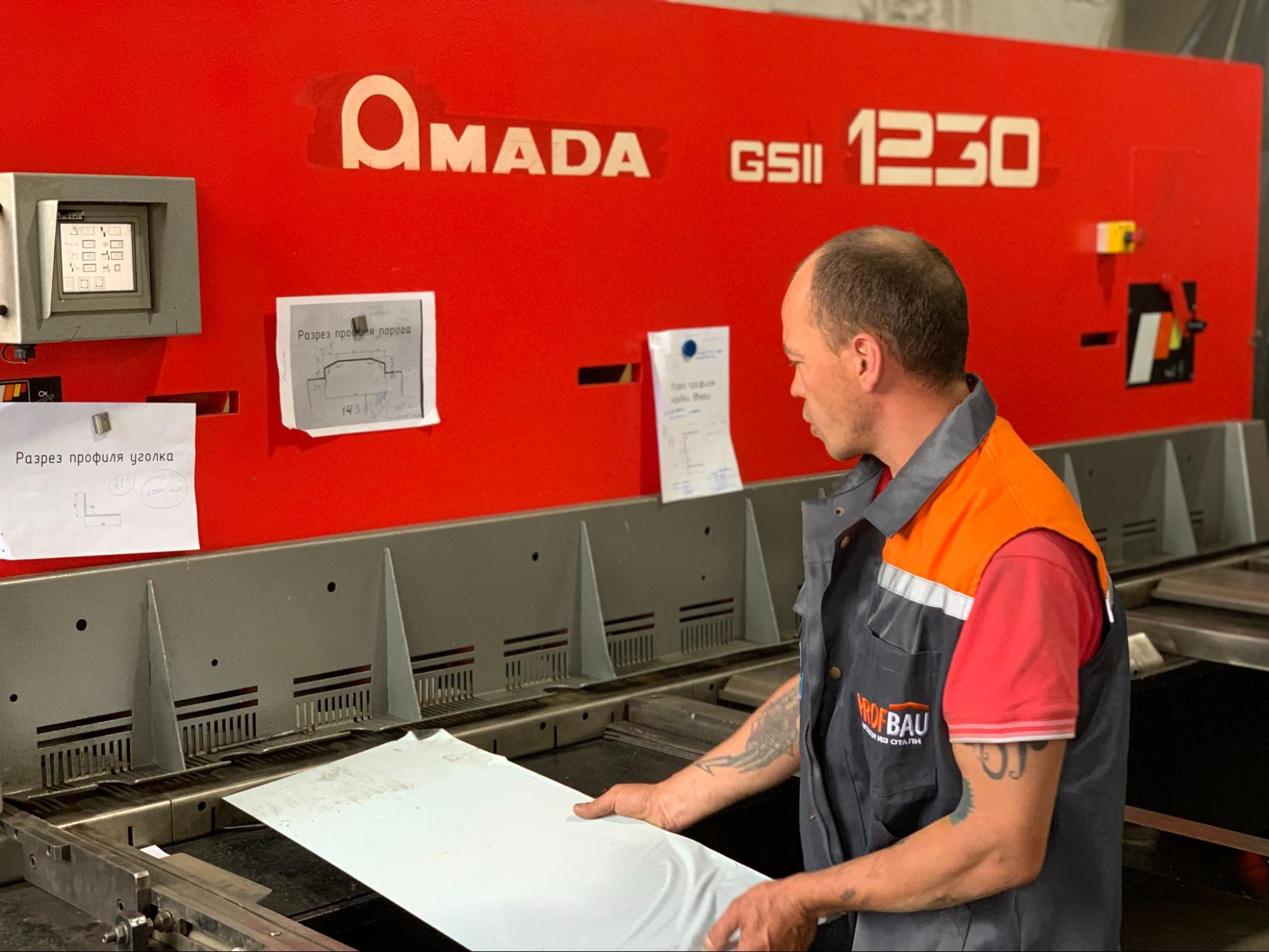
Химическая обработка
Если нужно подготовить поверхность к последующим операциям (гальванирование, оцинковка) или добиться эстетических показателей, прибегают к помощи химической обработки. В этом случае на металл воздействуют веществами, которые не только меняют его внешний вид, но и повышают стойкость к коррозии. Химические составы дают возможность очистить поверхность перед сваркой или окрашиванием.
Среди основных видов:
- Азотирование – повышает устойчивость материала к механическим повреждениям и влаге;
- Борирование – насыщение бором позволяет повысить износостойкость стали;
- Хромирование – насыщение слоев металла хромом не влияет на его прочность, но повышает устойчивость к образованию ржавчины;
- Цементация – насыщение материала углеродом.
Термическая обработка
Для улучшения характеристик заготовки мастера прибегают к использованию повышенных температур. При этом важно помнить, что у каждого металла есть границы, при которых изменится металлическая решетка или произойдет ее деформация: после остывания решетка становится прочнее.
Среди основных типов операции:
- Отжиг позволяет повысить ковкость и пластичность. Материал разогревают до конкретной температуры, остужают. К операции прибегают после литья для снятия напряжения.
- Закалка помогает повысить твердость изделия (но при этом оно становится более хрупким и менее вязким). Особенность процесса в том, что после нагрева еще некоторое время держится высокая температура, а охлаждение – в воде, масле – проходит быстро.
- Отпуск проводится после закалки. Материал нагревают до определенной температуры, сразу охлаждают. Как результат – снижение хрупкости изделия.
- Старение – метод декоративного оформления. Он позволяет получить красивую состаренную поверхность без влияния на ее основные качества. Заготовку медленно нагревают: удается добиться такого визуального эффекта, словно деталь старела в естественных условиях долгие годы.
- Нормализация. Изменение зернистости материала (с крупной на мелкую) позволяет увеличить его ковкость.
Электрическая обработка
Процесс такой:
- На латунный или графитовый электрод подают высокое напряжение;
- Происходит соприкосновение с обрабатываемой поверхностью;
- Из-за появившейся искры металл плавится и приобретает нужную форму
Чтобы частицы не разлетались, заливают масло, позволяющее их улавливать. Из преимуществ – полное отсутствие обрезков и остатков и чистота среза. Для создания блестящей поверхности используют электрохимический метод.
Художественная обработка
Поскольку металлические конструкции создаются еще и для изготовления предметов интерьера и декора зданий, мастера прибегают к их декоративной обработке. Повысить эстетичность изделий помогают такие методы, как литье, сварка, фигурная резка, чеканка, а для нанесения узора – травление.
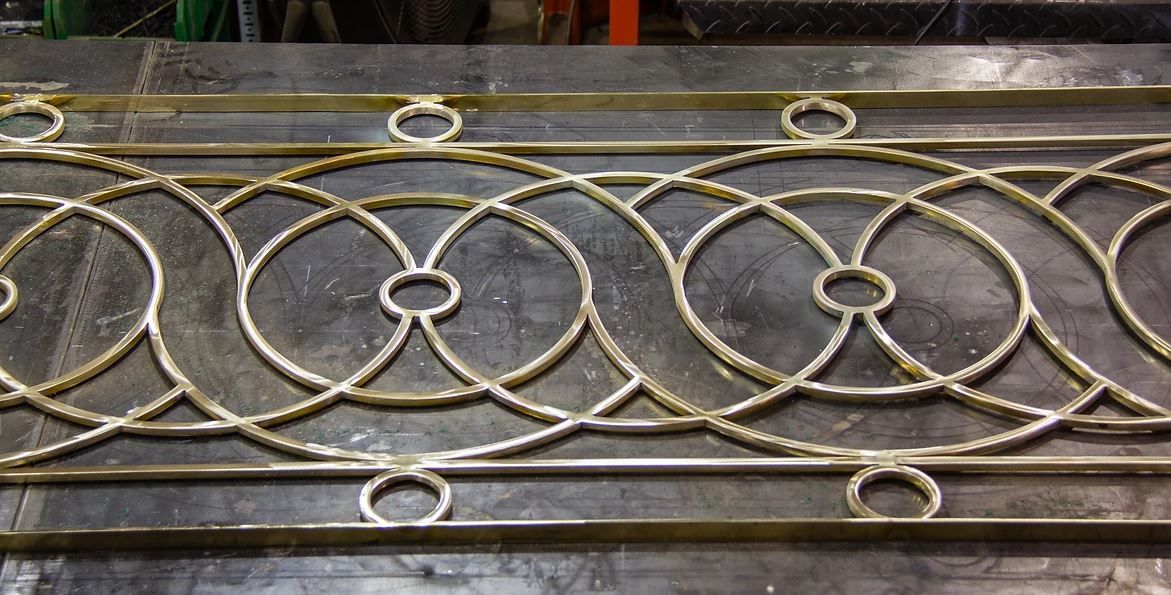
Покраска металла
Порошковая покраска металла наиболее современный и флагманский способ финишной обработки металлоизделий.
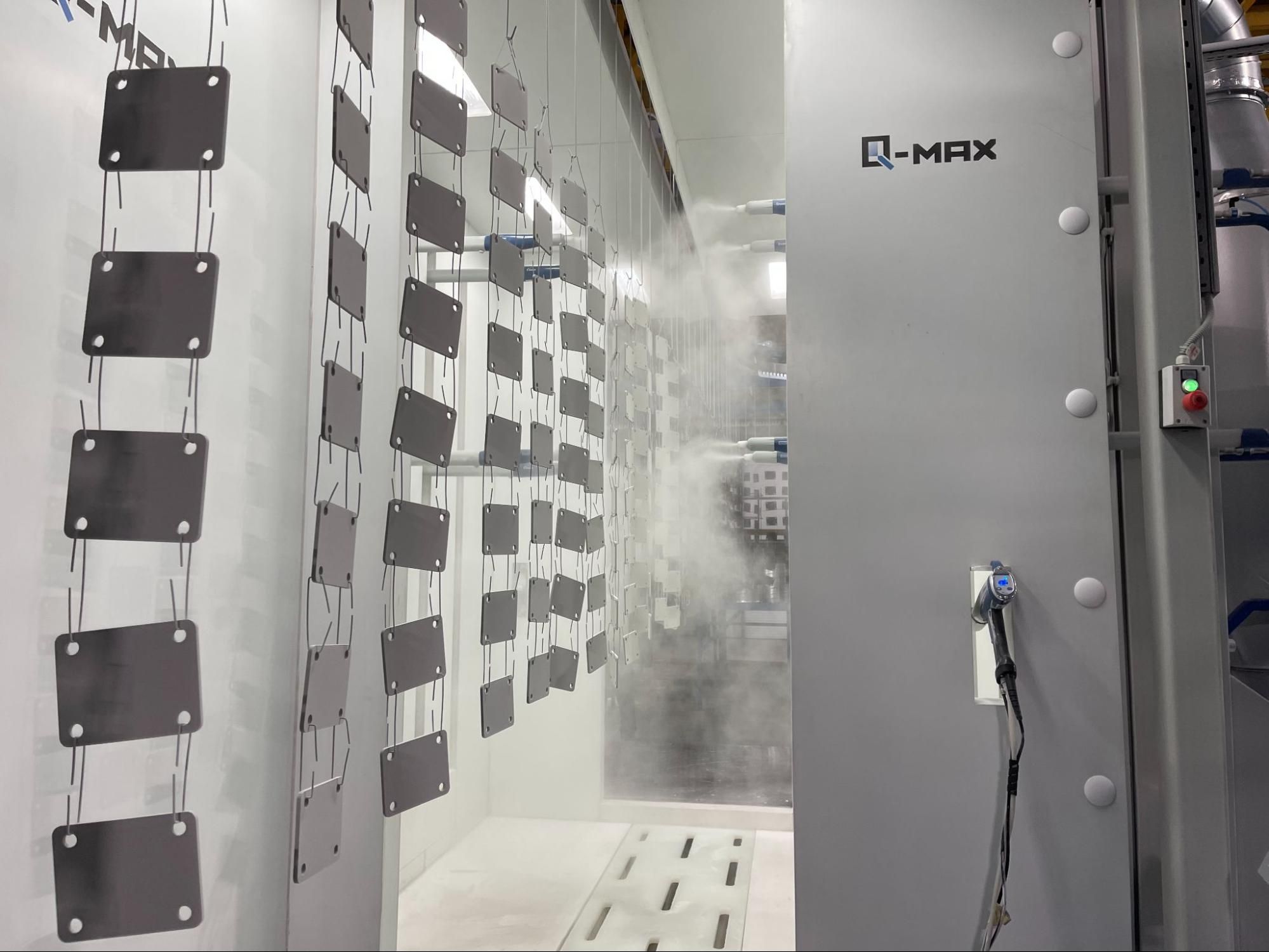
Компания «ПрофБау» проводит все типы обработки металла. Вы можете смело обратиться к нам из-за ряда преимуществ компании. Это:
- Инновационные технологии и традиционные способы;
- Современные приборы и инструменты;
- Быстрое исполнение заказов;
- Строгое соблюдение дедлайнов;
- Гарантия на все услуги;
- Профессиональные работники;
- Возможность купить материал в нужном объеме.
«ПрофБау» – это ответственное выполнение любых заказов. На https://www.profbau.ru/services вы можете узнать подробности обо всех видах услуг. Оставляйте заявку онлайн или звоните по телефону +7 (495) 138-25-25.