Для разрезания металлов используются разные способы. Одни основаны на тепловом воздействии, другие предполагают механическую обработку. Современная и эффективная технология – гидроабразивная резка. В этой статье расскажем, какие виды гидрорезки существуют, на каком оборудовании проводятся работы, и в каких сферах используют рассматриваемый метод.
Что такое гидроабразивная резка?
Под гидроабразивной резкой понимается металлообработка, при которой классический режущий инструмент заменяется подаваемой под давлением и с огромной скоростью выхода, сфокусированной тончайшей струёйводы, которая в большинстве случаев смешивается с абразивным материалом.
Суть технологии – эрозионное воздействие, оказываемое на разрезаемый металл либо только водой, либо комбинацией водяной узконаправленной струи и абразивных мельчайших твёрдых частиц. При таком процессе из полости создаваемого реза высокоскоростным и направленным потоком твердофазных частичек отрываются и сразу уносятся фрагменты обрабатываемого материала.
Обычно используют двухфазную струю, состоящую из воды в сочетании с абразивом. Результат зависит от нескольких параметров технологического процесса: вида расходников, их качества и потребления, величины абразивных частиц, максимального рабочего давления подачи, а также свойств материала.
История возникновения технологии
Впервые водную струю в промышленной сфере начали использовать ещё в начале позапрошлого XIX века. Тогда советские и новозеландские инженеры подавали воду под давлением в шахты, чтобы вымывать из них угольные рыхлые породы, руду и камень. Позже, когда в разгаре была золотая лихорадка, эту технологию переняли американские добытчики золота. Водяной поток позволял вычленять драгметалл и перемещать его по подготовленным каналам.
В 30-е годы двадцатого века гидроабразивным способом раскраивали бумагу, для чего на неё подавали струю очищенной воды. В 35-м году Элмо Смит из США предложил дополнять водный поток абразивом. Это позволило обрабатывать не только мягкие и тонкие металлы, но и более твёрдые.
Непосредственно гидроабразивной резке больше 4 десятков лет. В 40-х годах прошлого столетия активные исследования этой технологии велись советскими учёными, но позже изучение способа по каким-то причинам сошло на нет. В 79 году американские специалисты внедрили в струю воды песок, и это усовершенствовало режущие свойства. Годом позже был разработан и представлен первый в мире прототип стандартного станка. А ещё спустя 3 года, в 1983 было запущено серийное производство агрегатов для гидрорезки.
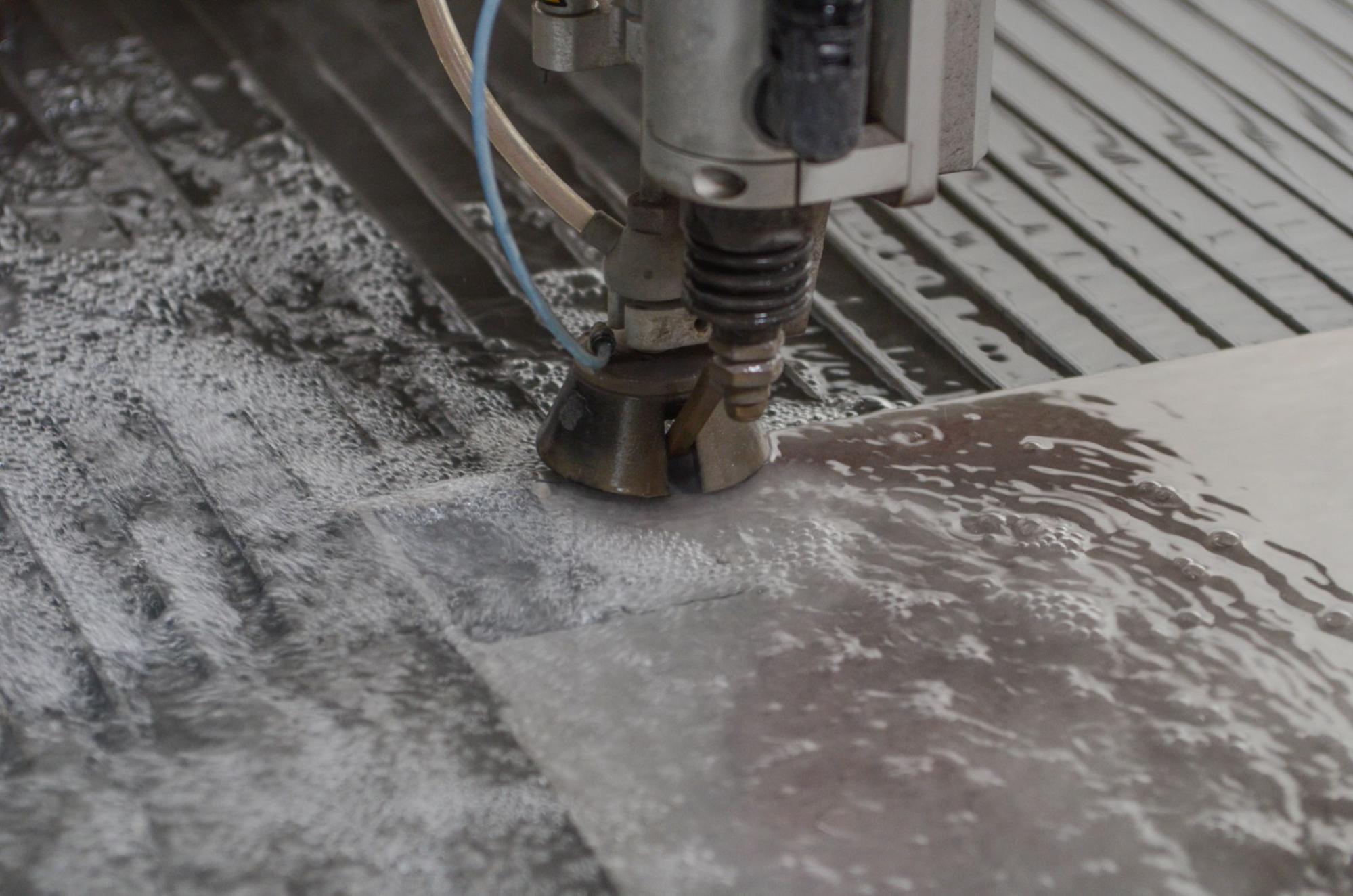
Принцип работы
Главным режущим элементом является водная струя, обычно соединяемая с абразивным материалом, выходящая под большим давлением и на высокой скорости через узкое сопло целенаправленно на участок реза. Принцип работ включает несколько основных этапов и видов воздействий:
- Давление. Для его создания вода нагнетается мощным насосным оборудованием. Технологический процесс протекает при значении давления от 20 до 50 тысяч фунтов на 1 квадратный дюйм. В пересчёте на используемые в России единицы измерения это примерно 9-27,2 тонн на 6,45 см2.
- Очистка воды. Она обязательно фильтруется, так как любые имеющиеся в ней примеси могут, во-первых, снизить качество реза, во-вторых, засорить сопло, в-третьих, повредить рабочие узлы оборудования.
- Подача. Водяной поток по трубкам высокого давления перемещается к рабочей головке и через её маленькое отверстие выходит на обрабатываемую зону. При этом гидравлическая энергия трансформируется в кинетическую. Формируется высокоскоростная, тонкая, сфокусированная и направленная струя.
- Смешивание с абразивом. Если он используется, что необходимо в случае высокой твёрдости разрезаемого материала, то к основанию режущей головки подсоединяется смесительная специальная камера. В ней, когда вода выходит из отверстия, появляется вакуумная среда. Благодаря этому абразивные частички буквально втягиваются в водяной поток и, смешиваясь с ним, через сопло или фокусирующую подающую трубку, направляются на материал.
- Непосредственно резка. Выходящая под большим давлением и с огромной скоростью струя с абразивом или без него попадает на поверхность металла или иного материала и разрушает его с контролем рабочих параметров. Такое разрушение стартует с поверхностных слоёв, постепенно углубляется в толщу.
- Удаление образующихся отходов. Под зоной резки находится отдельный приёмный резервуар. В него попадают отработанные вода и абразив. Последний обычно утилизируется или перерабатывается. А вода очищается и может повторно использоваться для следующих циклов.
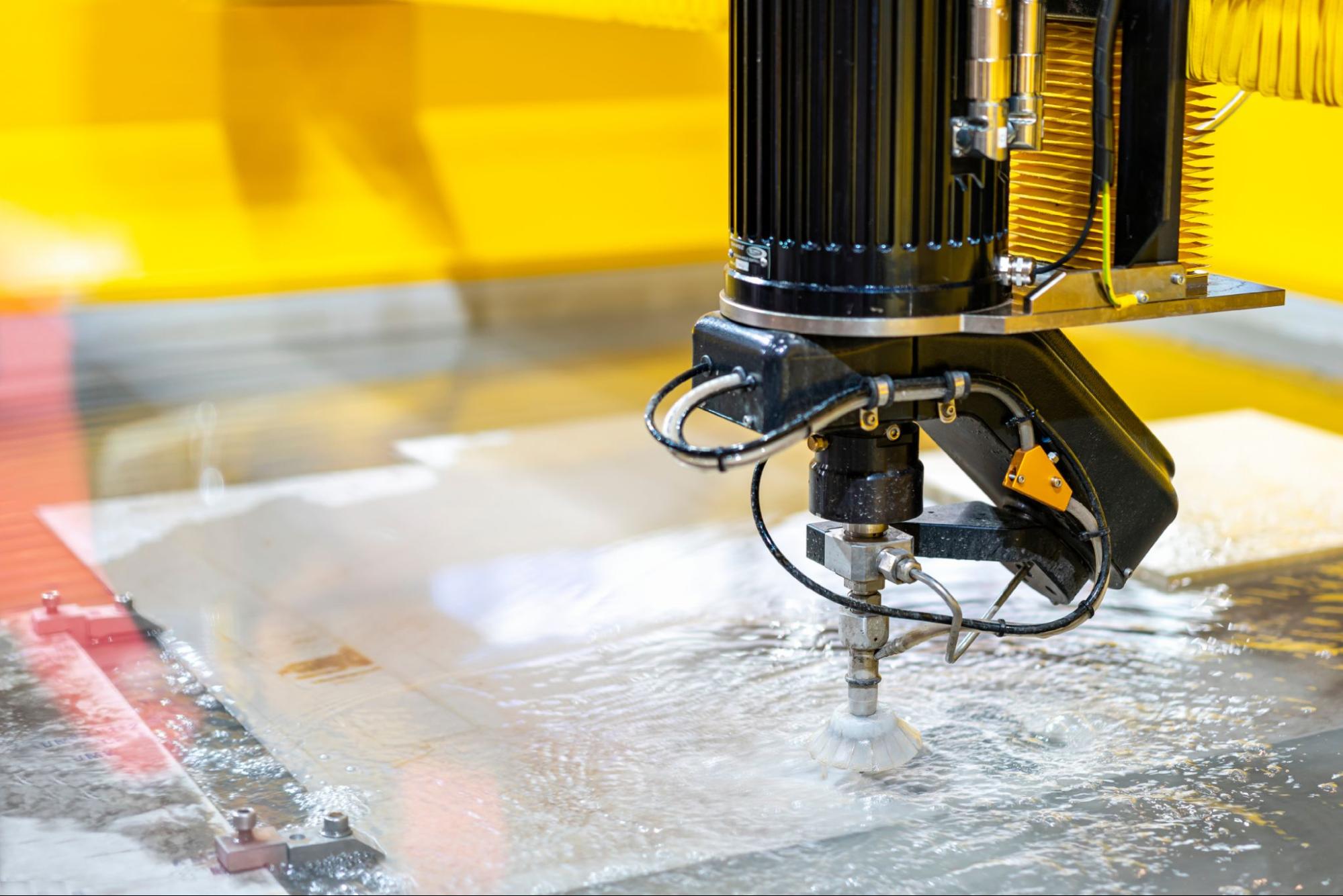
Рабочие параметры
Для достижения ожидаемых результатов оборудование должно функционировать с определёнными рабочими параметрами. Первый – давление. Оно обычно составляет от 2000 бар (атмосфер) до 5000. В мощных станках, используемых для резких твёрдых металлов и твердосплавных материалов, показатель достигает 6900 бар. Меньшие значения тоже возможны, но они подходят только для тонколистовых либо мягких заготовок.
Второй важный параметр – скорость, с которой выходит струя. Она равна порядка 1000-1200 метров в секунду. Это фактически скорость звука, поэтому воздействие очень интенсивное, что и позволяет разрезать материалы.
Третий параметр – диаметр струи. Он очень мал – всего от 0,2-0,5 до 1-1,5 мм, в зависимости от характеристик материала и реза. Столь тонкая струя формируется выходным соплом, который по диаметру чуть больше водяного потока – примерно 0,6-1,2 миллиметра.
Четвёртый параметр – размер частичек абразива. Для высокой точности и достойного качества формируемого реза величина должна быть очень маленькой – от 100 микрометров до 600. В пересчёте на миллиметры это 0,1-0,6 мм. Если размер увеличивается, то воздействие получается менее точным, а кромка реза – не такой ровной.
Не менее важен расход используемых для разрезания материалов. Так, абразивные частицы потребляются примерно по 35-50 граммов за одну секунду. Расход воды может достигать 4 литров в минуту. Это не так много, ведь струя очень тонкая, поэтому и потребление незначительное.
Рабочая головка движется по заданной траектории, которая программируется заблаговременно оператором на станке, оснащённом числовым программным управлением (ЧПУ) или ПО для автоматизированного проектирования (CAD).
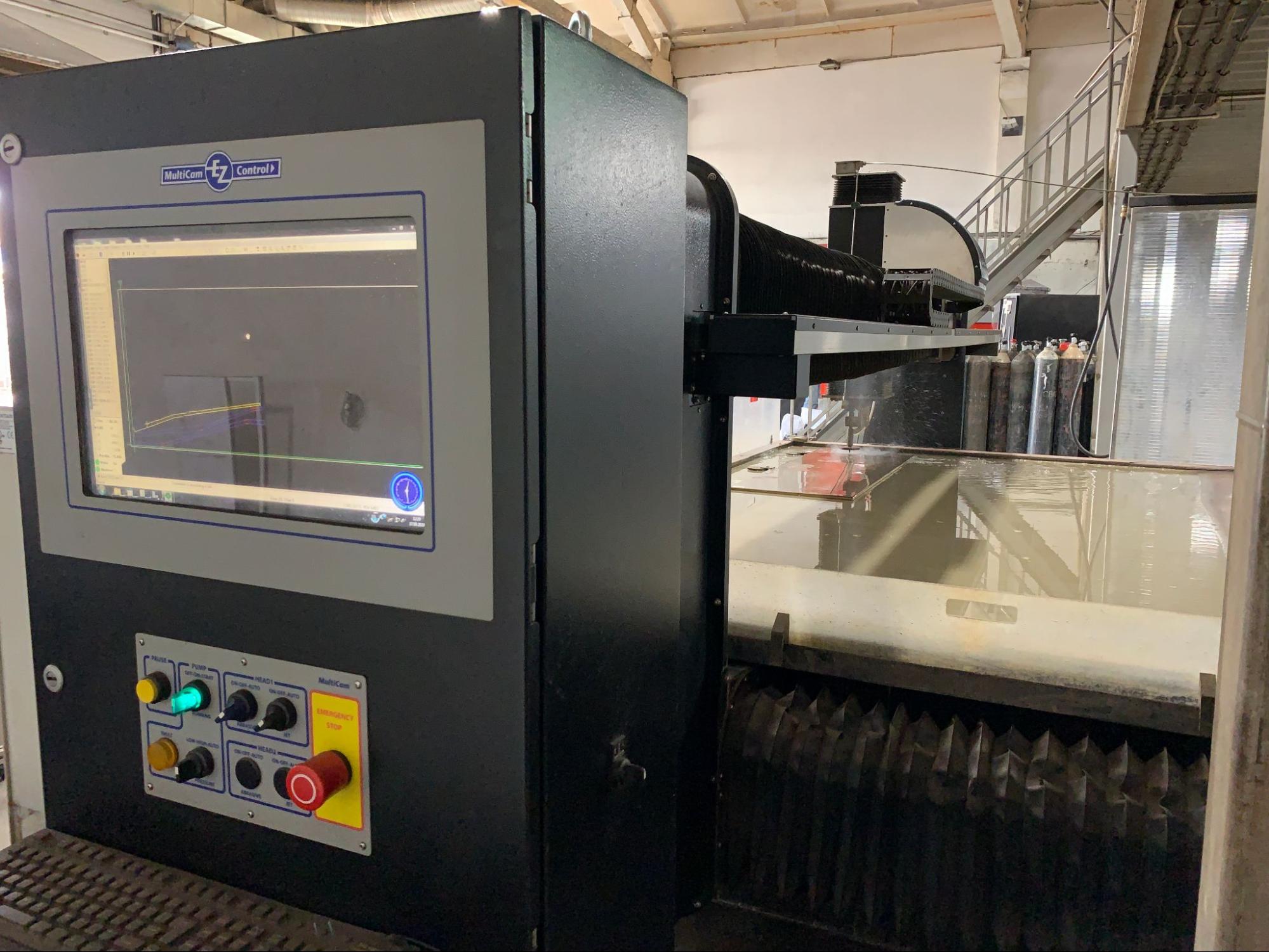
Виды гидроабразивной резки
Есть два вида:
- Гидроабразивная резка с применением абразивного материала. В струю в данном случае вводятся мельчайшие твёрдые частички, которые оказывают дополнительное механическое воздействие и усиливают струю. Такая технология подходит для различных металлов, толстых и плотных пластиков, для керамики, искусственного или натурального камня, для незакалённого стекла.
- Гидроабразивная резка без абразива. Такой вариант подходит больше для мягких материалов, например, тканей, бумаги, картона, пенопласта, резины, войлока, пенополистирола, тонких полимеров, древесины, а также продуктов питания. В качестве режущего материала используется только вода, которая фокусируется в тонкую струю и благодаря насосу достигает нужных значений давления. Она формирует резы с чистыми кромками. Такая технология менее инвазивна, чем предыдущая.
Современные многофункциональные станки универсальны и позволяют использовать оба метода. В конструкции оборудования предусмотрена возможность подсоединения к рабочей головке смесительной камеры для подачи абразива при необходимости.
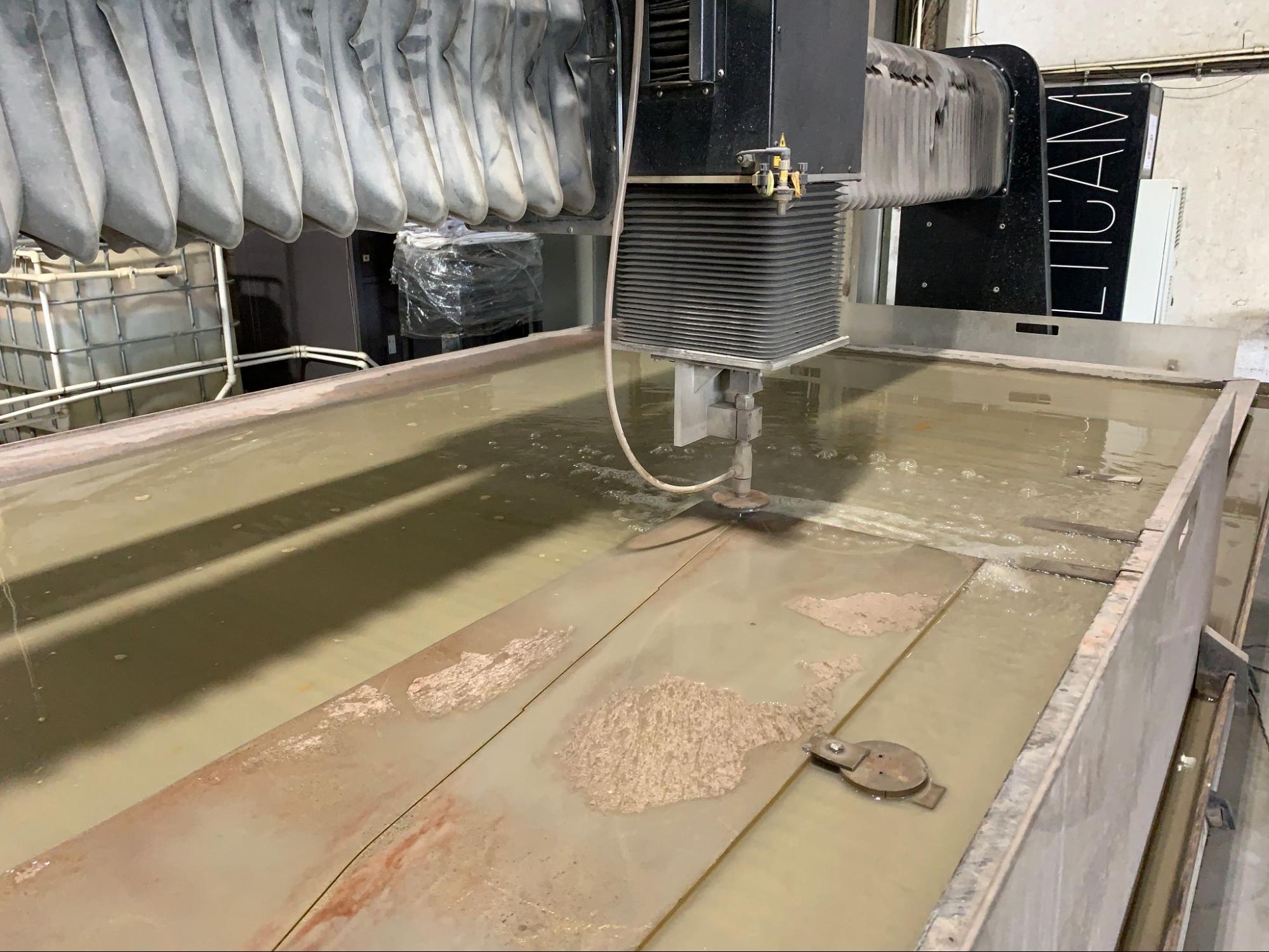
Области применения гидроабразивной резки
Гидроабразивный способ обработки получил широкое применение и активно используется в следующих областях:
- автомобилестроение – изготовление прокладок, элементов кузовов, некоторых запчастей или деталей для постпродажного обслуживания;
- аэрокосмический комплекс – выпуск изделий для космических кораблей и воздушного транспорта, производимых из композитов или лёгких металлов типа титана, алюминия;
- реализация архитектурных проектов, отделочные работы – нарезание керамической или керамогранитной плитки, облицовочных фасадных материалов;
- рекламная сфера – производство стендов, вывесок, прочих конструкций из металлов, пластиков;
- электроника – нарезание печатных плат, изготовление корпусов сложных электронных устройств;
- машино-, станкостроение – выпуск различных станков, прочих агрегатов, в том числе для металлообработки;
- строительство – производство отделочных, утеплительных, изоляционных, облицовочных материалов: сэндвич-панелей, вагонки, плитки, базальтовых плит, рулонной и листовой минеральной ваты;
- интерьерный, ландшафтный дизайн – изготовление декоративных элементов, например, фигурных ограждений, скульптур, статуй, фигур;
- инструментальная промышленность – выпуск различных измерительных, монтажных, режущих, слесарных, зажимных инструментов, а также оснастки для них;
- пищевая промышленность – точная и быстрая порционная или фасовочная предпродажная нарезка продуктов питания (замороженных рыбы, мяса, овощей и полуфабрикатов, готовой выпечки, колбасных изделий),
- оборонный комплекс – нарезание и раскрой разных материалов и изделий, включая взрывоопасные и взрывчатые: снарядов, кевлара, углепластиков;
- изготовление упаковок в разных сферах промышленности;
- целлюлозно-бумажная отрасль – выпуск гофрированного и обычного картона, печатной или другой рулонной и листовой бумаги;
- кожевенная промышленность – изготовление верхней одежды, аксессуаров, прочих изделий из кожи;
- обувное производство – раскрой обуви;
- металлообработка – выполнение металлических заготовок для разных производств.
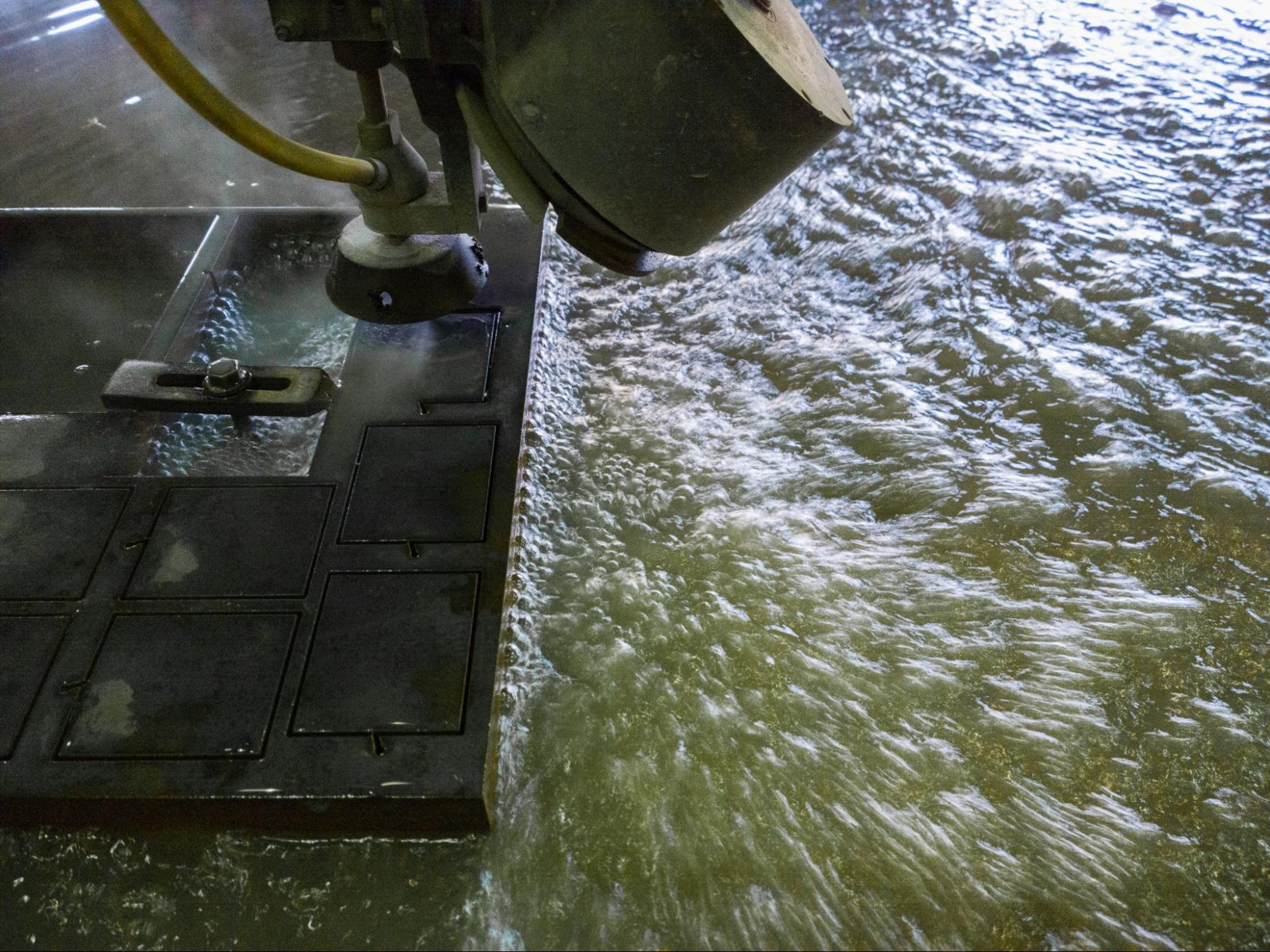
Широкие возможности
Гидроабразивным способом можно резать:
- чёрные металлы и сплавы: чугун, железо, стали разных марок (легированные, нержавеющие, конструкционные);
- цветные сплавы и металлы: никель, магний, алюминий, медь, титан, латунь;
- обычное стекло и композиционное, в том числе армированное, триплекс, стеклотекстолит, бронестекло;
- железобетон, бетон;
- натуральный камень и искусственный: мрамор, песчаник, гранит, сиенит, габбро, кварцит, травертин, сланец и прочие;
- синтетические композитные, полимерные материалы, например, поролон, полиуретан, пенопласт, пенополиуретан;
- керамика;
- любой текстиль;
- картон и бумага;
- кожа;
- продукты питания.
Возможно осуществлять резку или раскрой металлопроката: листов, швеллеров, труб, прутков, балок, арматуры, уголков. Гидрорезка позволяет формировать сложные, фигурные разрезы или надрезы не на всю глубину. Можно создавать как заготовки, так и полноценные готовые изделия, причём в некоторых случаях не требующие финишной чистовой обработки благодаря высокому качеству кромок.
Гидроабразивная резка эффективно работает там, где недопустимы другие технологии, предполагающие термические воздействия – нагрев до критических температур, который может быть опасным при контактах с взрывоопасными, плавящимися, легковоспламеняющимися, горючими веществами. Также гидрорезка подойдёт для волокнистых, имеющих пористую структуру и многослойных огнезащитных, изоляционных или других материалов с особыми характеристиками.

Гидроабразивная резка в сравнении с другими методами
Главное отличие от других методов – это нетепловая энергия. В зоне реза нет даже локального повышения температуры, так как, во-первых, отсутствуют быстрые вращательные или возвратно-поступательные движения рабочих инструментов, во-вторых, не используются источники тепла, в-третьих, вода дополнительно охлаждает участок воздействия. Такие особенности делают гидрорезку практически универсальной, подходящей даже для материалов, которые нельзя нагревать.
Если сравнивать гидроабразивную и лазерную резку, то последняя больше подходит для разных материалов, кроме отражающих, особо чувствительных к нагреванию и имеющих значительную толщину. А гидрорезка в таких случаях может использоваться.
Лазер хорошо работает при малой и средней толщине – не больше 25 мм для металлов и 50 мм для других материалов. Гидроабразивная резка имеет более широкий диапазон – до 200 миллиметров для некоторых металлических заготовок. При лазерной технологии можно добиваться более высокой точности и значительной скорости. Расходы ниже, так как потребляется только электричество.
Качество реза примерно одинаковое, так как лазер выделяет локальное и направленное тепло, поэтому другие участки материала не затрагивает. А гидроабразивная резка полностью холодная. Поэтому края всегда чистые, без наплавов, окалины, заусенцев. Также нужно помнить, что при использовании лазера выделяются газы, так что помещение должно быть хорошо проветриваемым.
При плазменной резке тоже протекает термический процесс, при котором эффективно, с высокой скоростью и небольшими расходами разрезаются металлы, проводящие ток. Но из-за критических температур вероятны наплавы, окалины и прочие дефекты. А это требует дополнительной финальной отделки. Также плазменный способ демонстрирует более высокую скорость, но имеет ограничения по толщине, видам и свойствам обрабатываемых материалов.
Кислородно-топливная технология применима, прежде всего, к чёрным металлам, их низколегированным сплавам – мягким чугунам, сталям. В основе способа – способность материала окисляться. И именно поэтому применение ограниченное, так как находится в зависимости от свойств окисления. Кислородно-топливную резку используют для тонколистовых изделий. Гидрорезка точнее и совместима с большим количеством материалов.
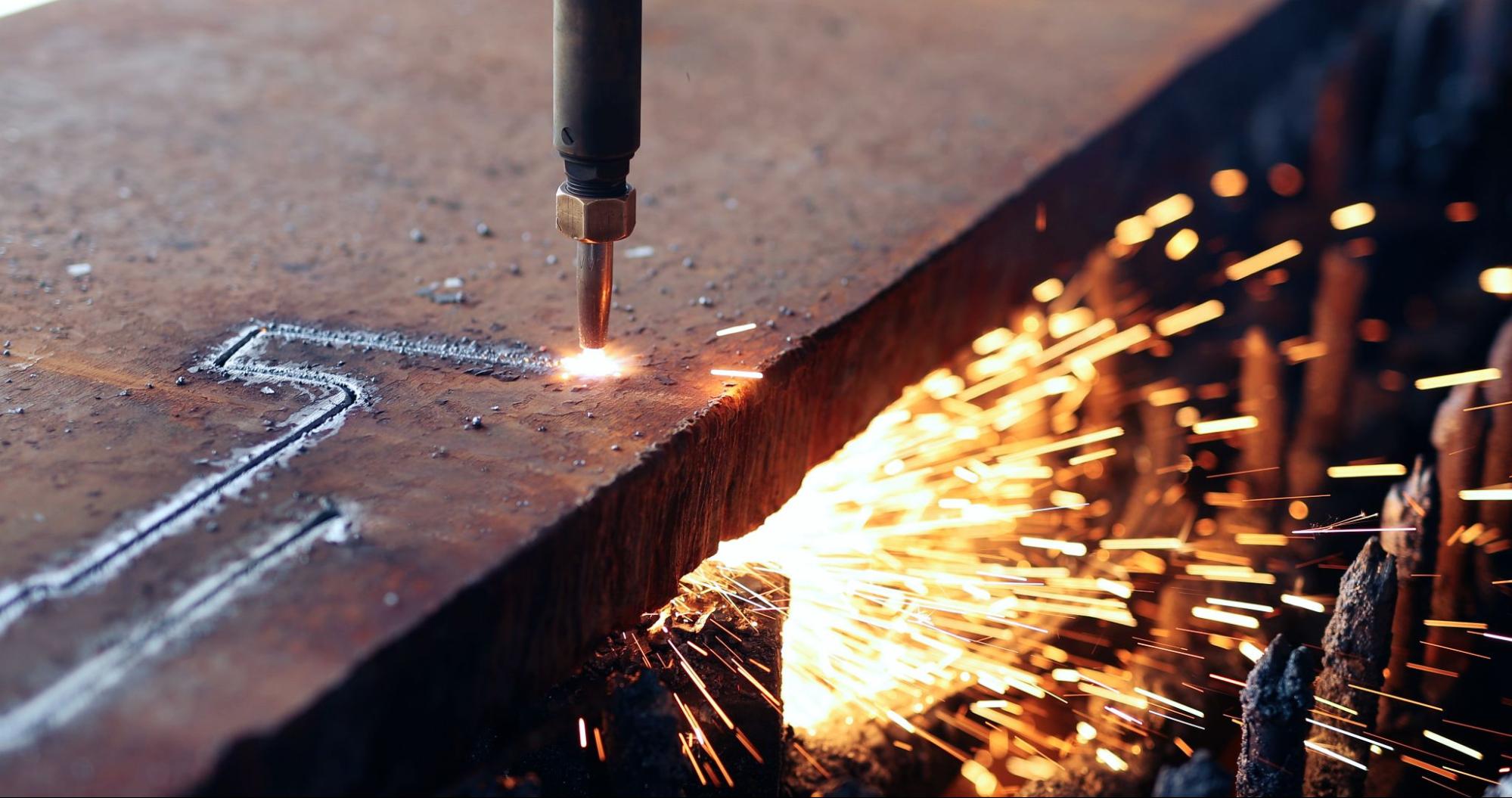
Оборудование для гидрорезки
Оборудование имеет конструкцию, состоящую из пяти главных узлов:
- Насосная станция. Это основной элемент, нагнетающий нужное давление.
- Координатный стол. На нём располагаются разрезаемые материалы. Они фиксируются в нескольких точках для исключения рисков случайных смещений.
- Режущая головка. Это зона с выходным отверстием, из которого выходит высокоскоростная направленная струя. К этой же головке может подсоединяться следующий элемент.
- Система подачи абразивного материала. Это смесительная камера, в которой формируется вакуум, за счёт чего абразив быстро втягивается в рабочую головку и выходит вместе с водяной струёй.
- Стойка оператора с модулем управления. Тут стоит мастер, который задаёт настройки, регулирует рабочие параметры и контролирует процесс.
По конструкционным особенностям насосы станков делятся на два вида. Первый – мультипликаторный. В нём подающие воду плунжеры движутся возвратно-поступательно и создают масляное давление на гидравлический главный поршень. Он и торец плунжера имеют двадцатикратную разницу площадей. Это позволяет увеличивать давление в двадцать раз. К примеру, если масло подаётся при 200 атмосферах, то вода будет выходить уже со значением, равным 4 тысячам атмосфер.
Второй вариант – прямого действия. Это система из трёх поршней, нагнетающих воду. Они движутся посредством коленвала. По трубкам высокого давления жидкость далее перемещается в рабочую головку, смешивается с абразивом (если предусмотрена смесительная камера), идёт в фокусирующую трубку и из отверстия буквально вылетает, после чего врезается в расположенную на координатном столе заготовку.
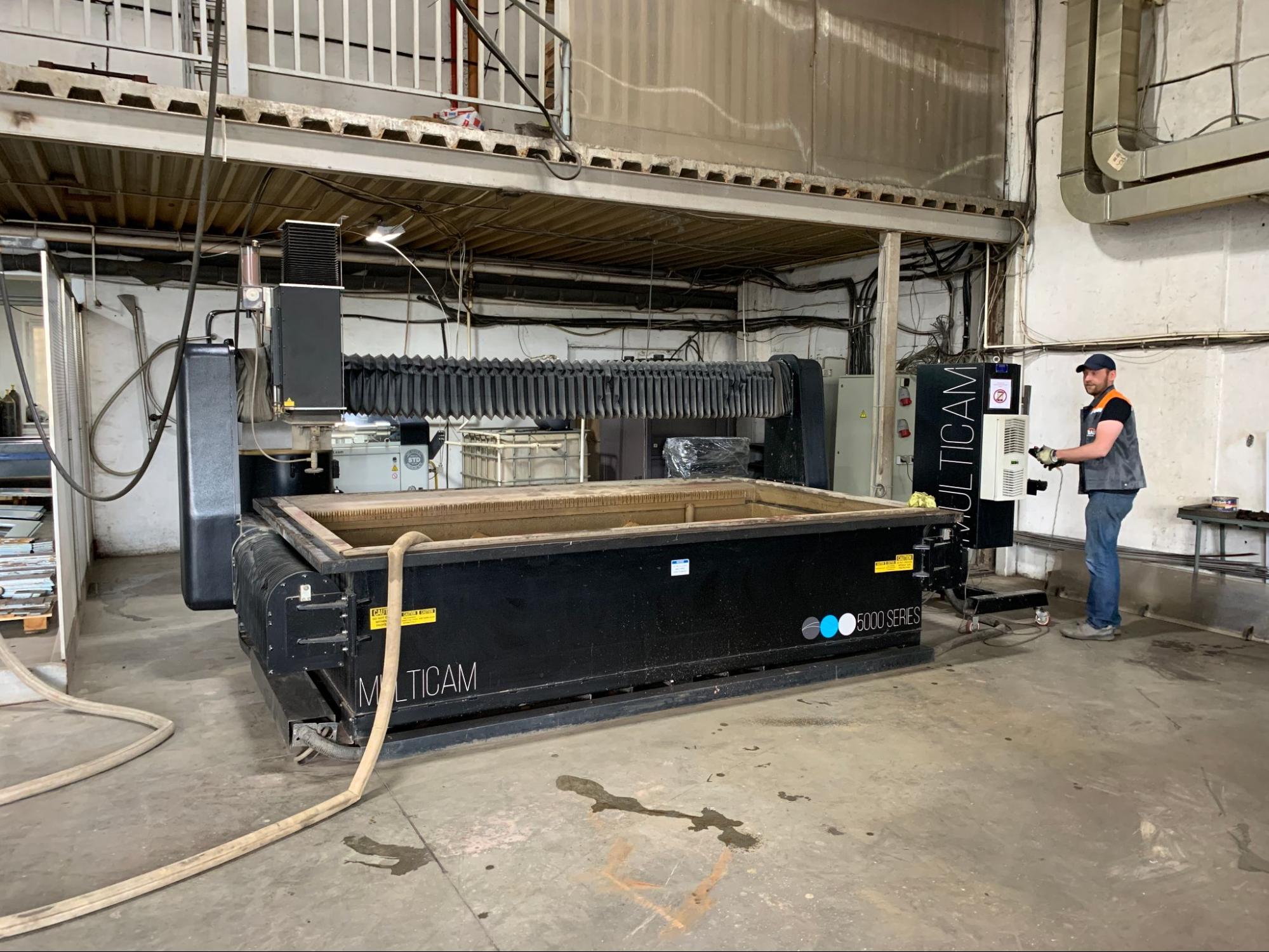
Расходные материалы
Главным сырьём является вода. Она перед использованием подвергается многоэтапной очистке. Её режущая способность многократно возрастает с добавлением абразива. Самый недорогой и доступный – песок мелкой фракции. Размер одной песчинки – всего 600-650 микрон. Также в качестве абразивов используют гранатовый песок, и самым лучшим считается имеющим океаническое происхождение. Материал твёрдый, обладает оптимальной фракцией.
Важно! Расход материалов зависит от толщины, твёрдости сплавов и металлов. Чем материал толще и твёрже, тем больше потребление абразива и воды.
Другие расходные материалы – это фокусирующие трубки, сопла. Они производятся из особо прочных синтетических рубинов, кристаллов корунда, сапфиров, алмазов, керамокарбида. Так, сапфировая трубка в среднем служит 60 часов, керамокарбидная – до 120.
Преимущества гидроабразивной резки
Гидрорезка имеет несколько преимуществ:
- Универсальность. Технология применяется в различных областях, подходит для самых разных материалов, включая мягкие и чувствительные к повышенным температурам.
- Отсутствие наплавов, окалины и иных дефектов, возникающих при нагревании металлов до высоких температур.
- Экономия. Вода и абразивы стоят относительно недорого, их расход небольшой, а металлической стружки нет.
- Экологическая чистота. Абразивы и вода безвредны для окружающей среды и людей. При резке не выделяются пары, газы, летучие вещества.
- Высокая точность. При гидрорезке можно добиваться ровных краёв срезов, их максимального соответствия стандартам или индивидуальным заданным параметрам (габаритам заготовок, их конфигурации).
- Возможность создавать детали сложных форм, с фигурными срезами.
- Высокая безопасность. Нет рисков возгораний или травмирования режущими инструментами.
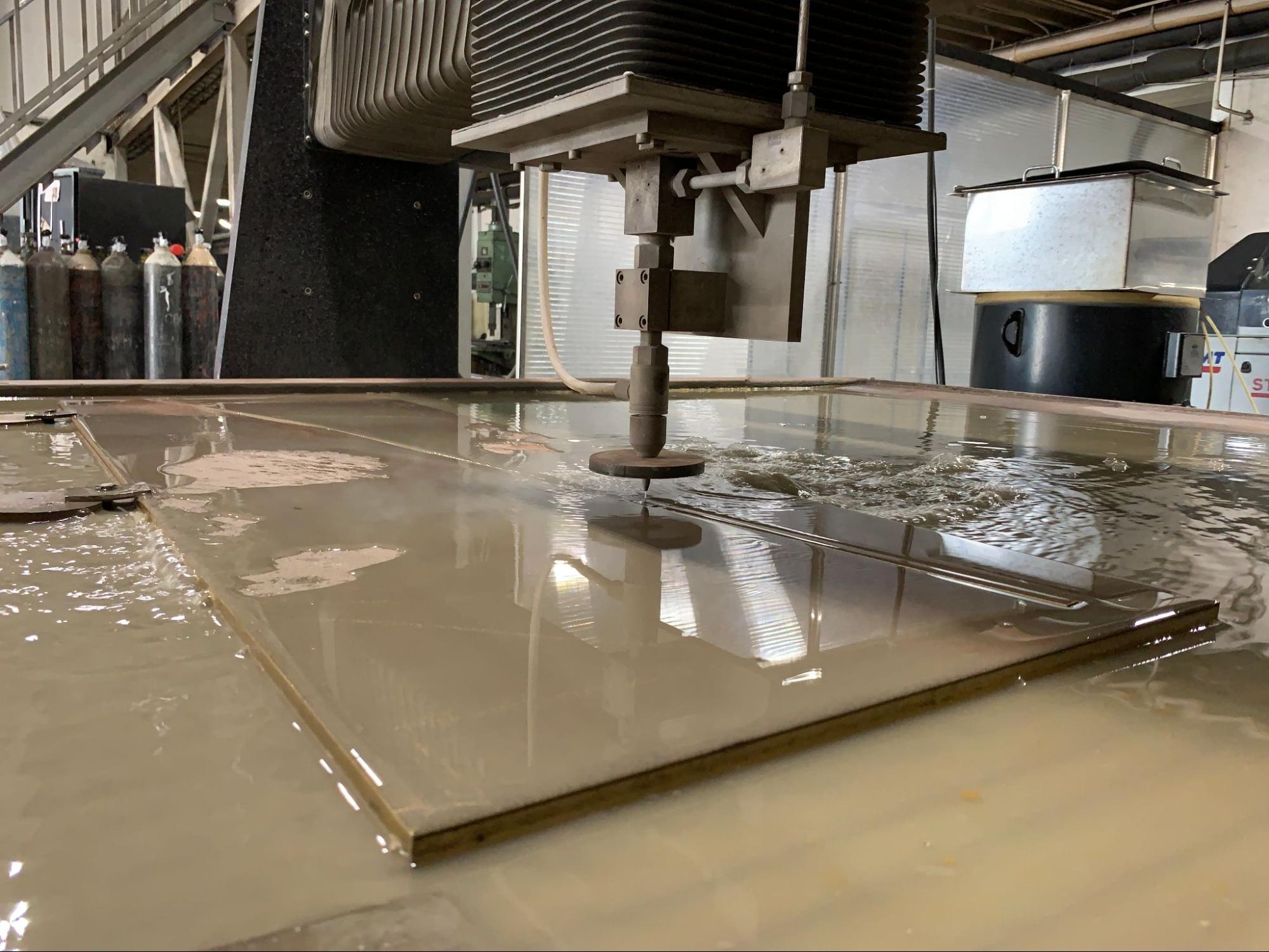
Недостатки метода
Рассмотрим недостатки:
- Не самая высокая скорость. Она ниже, чем при некоторых других технологиях.
- Затраты на абразив, а также на замену выходящих из строя сопел, фокусирующих трубок.
- Эффективная резка только изделий несложных, стандартных форм.
- Высокие риски коррозии. Струя воды с абразивом, во-первых, может повреждать защитные покрытия материалов, во-вторых, провоцирует окисление металлов и появление ржавчины.
- Достаточно громкие звуки. Гидрорезка – шумный процесс.
- Конусность. По мере углубления в толщу материала струя ослабевает, поэтому на входе зона воздействия больше, чем на выходе. Из-за этого отверстия обретают коническую форму.
Заключение
Результаты гидроабразивной резки зависят от возможностей используемого оборудования и опыта мастера. Компания Profbau – предприятие полного цикла, которое давно и успешно занимается металлообработкой и производством изделий.
Мы используем только автоматизированные современные станки, на которых работают квалифицированные сотрудники. Знаем все тонкости технологии, учитываем характеристики металлов. Выполняем работы оперативно, с высокой точностью, с экономным расходованием материалов, максимальным соответствием конечных размеров и форм изделий требованиям заказчиков и заданным параметрам.