Сквозные и несквозные отверстия предусмотрены в различных деталях и изделиях, например, во втулках, колёсных проставках, гайках, подшипниках, зубчатых колёсах, звёздочках, крыльчатках, лопастях, маховиках, муфтах, ниппелях, патрубках, проушинах, стаканах, ступицах, фланцах, форсунках, цапфах, шайбах, шарнирах, шатунах, шкивах, штуцерах. Всё это используется в разных конструкциях и узлах, применяемых в промышленности: металлообработке, станко-, машино-, судо-, автомобилестроении и других отраслях.
Обработка отверстий – это целый комплекс технологических операций, выполняемых с целью доведения геометрии и габаритов до требуемых параметров, установленных общепринятыми стандартами, специфическими требованиями или нестандартными техническими заданиями. В статье расскажем, какие методы и инструменты применяются, а также как выбрать подходящий способ.
Виды отверстий
По расположению в деталях отверстия делятся на:
- Центральные. Располагаются в центре изделия, то есть в зоне оси. К таковым относятся отверстия, например, во фланцах, муфтах. Для обработки применяются токарные станки, которые также используют для доведения до требуемых параметров торцевых зон, наружных поверхностей. Такой подход обеспечивает точность взаимного расположения частей изделий.
- Нецентральные. Могут находиться в разных участках, отличных от осевой области. Подобные отверстия формируются по окружности фланцев, колёсных проставок. Они обрабатываются с помощью фрезерных, сверлильно-расточных станков.
По форме выделяют следующие разновидности:
- Цилиндрические. Они имеют конфигурацию цилиндра и разные диаметры, считаются самыми распространёнными. Для формирования используют различное оборудование.
- Конические. Их форма – усечённый конус. Главный параметр – конусность, представляющая собой отношение разности диаметров поперечных торцевых сечений геометрической фигуры к длине проложенного между ними отрезка, то есть расстоянию между торцами. Обрабатывают такие отверстия на расточных машинах с помощью развёрток и свёрл, расточных головок или резцов. Все эти инструменты имеют коническую конфигурацию.
- Фасонные. Они имеют форму, отличную от конической и круглой. Сечение может быть овальным, эллиптическим, прямоугольным, треугольным, квадратным, многогранным или другим, с более сложным контуром.
- Ступенчатые. Они формируются в несколько заходов (одним инструментом разных размеров или разными рабочими элементами) путём создания отверстий разных диаметров, обычно переходящих друг в друга и располагающихся на одной оси. Получаются своеобразные ступени, выступы.
- Резьбовые. Их особенность – резьба, представляющая собой чередующиеся выступы и канавки. Такие отверстия используются в резьбовых разъёмных соединениях, например, в парных крепёжных деталях – гайках, используемых в комплексе с болтами, шпильками.
По степени прохождения через материал отверстия могут быть:
- Сквозными. Проходят через всю толщину металла.
- Глухими. Не проходят через материалы полностью, формируются на определённую неполную глубину.
Также отверстия классифицируются по назначению. И по этому критерию они подразделяются на:
- Крепёжные. Формируются в элементах конструкций, узлов или механизмов для их сборки, иногда оснащаются резьбой. Для крепежа обычно применяют винты, шпили и болты с гайками.
- Технологические. Они предусматриваются технологией дальнейшей эксплуатации изделий. Через такие отверстия могут прокладываться, например, трубы, кабели.
- Дренажные. Их основная задача – отведение влаги, которая образуется из-за конденсата, просачиваний, утечек, капиллярного эффекта, атмосферных явлений, влияющих на конструкции, используемые на открытом воздухе.
- Ответственные. Они имеют важное значение в многокомпонентных механизмах, предназначаются для установки главных рабочих или несущих элементов конструкций.
- Облегчающие. Их делают для снижения общей массы тяжёлых металлических конструкций. Такие отверстия при правильном создании не влияют на прочность, но при этом заметно уменьшают вес и понижают нагрузку, ложащуюся, к примеру, на опору.
Способы обработки отверстий
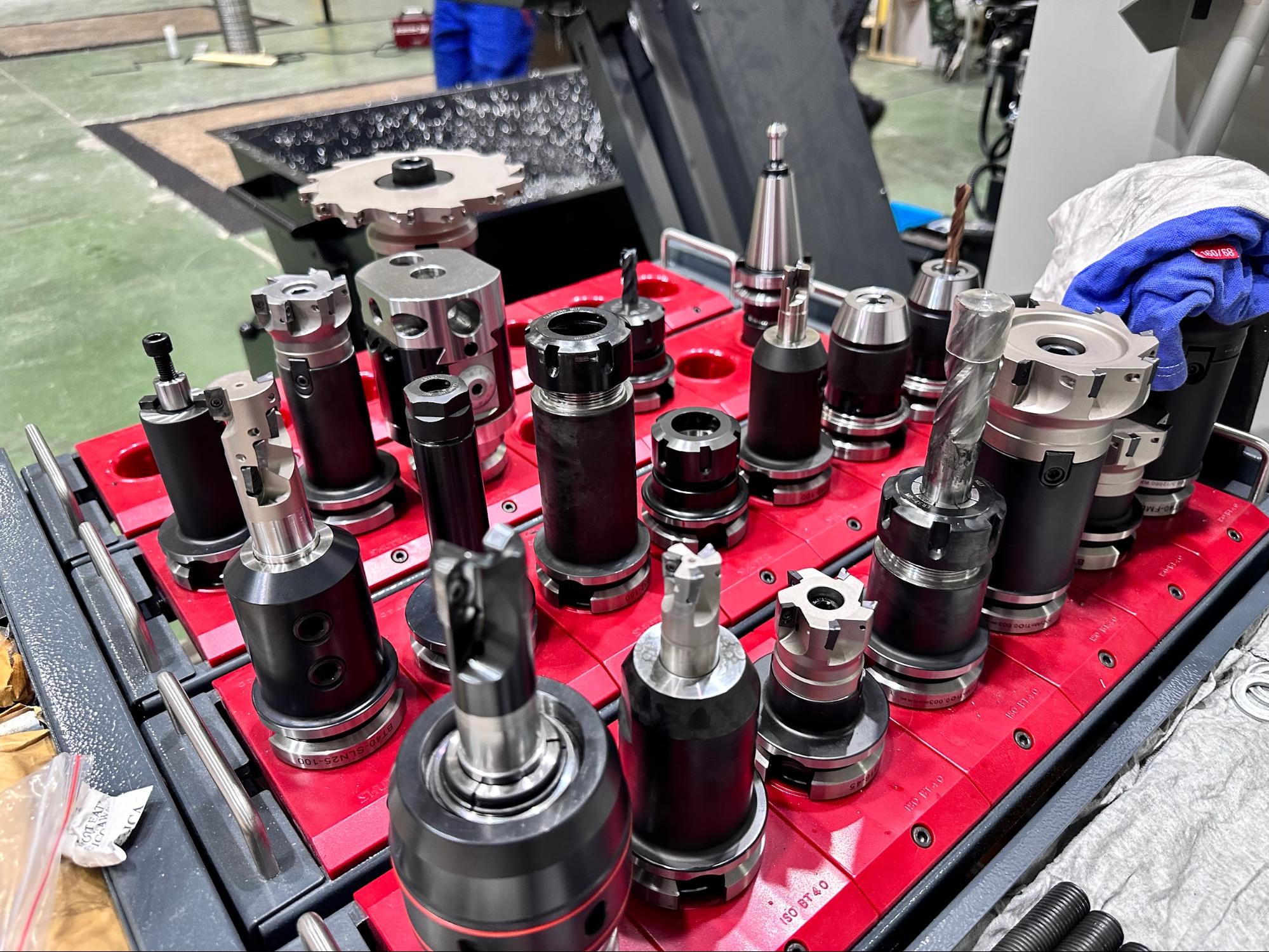
Существующие способы обработки отверстий различны. Они делятся на ручные и автоматические. В первом случае операции проводятся ручными инструментами (развёртками, резцами), с приложением физических усилий мастера. Автоматические методы предполагают применение специализированного оборудования, в котором движение рабочих элементов обеспечивается функционированием двигателя и механизмов, передающих вращение. К таким агрегатам относят фрезерные, сверлильно-расточные, токарные, шлифовальные.
Все технологические операции делятся на:
- Черновые. При них снимается основной припуск, что необходимо для достижения точности размещения отверстия по отношению к оси или к базе, для получения равномерного припуска, а также для подготовки к последующей чистовой обработке.
- Чистовые. Такие операции позволяют добиваться высокой точности, а также соответствия геометрии и габаритов стандартам или чертежам.
- Отделочные. Такие процедуры проводятся не всегда, а только в случаях повышенных требований к конечному качеству: допустимой степени шероховатости, точности размеров и конфигурации.
Ниже рассмотрим виды обработки отверстий, используемые для разных изделий.
Сверление
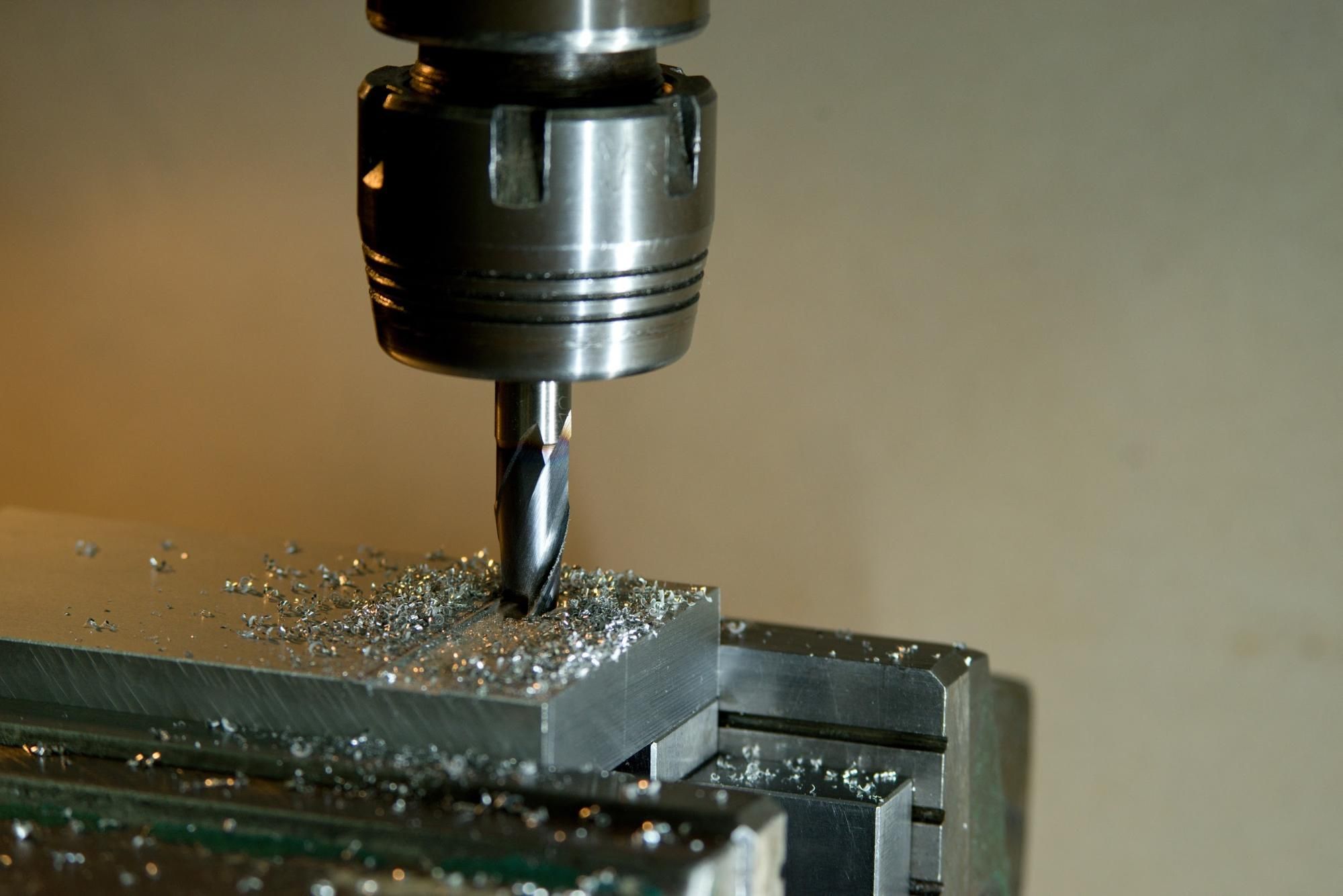
Обработка отверстий свёрлами называется сверлением. Такая технология используется как для первичной подготовки заготовок, так и для последующих технологических операций, например, увеличения диаметра. С помощью свёрл создают и обрабатывают глухие и сквозные отверстия.
Сверление бывает:
- Ручным. Для него требуются сверлильные механические мобильные устройства, к примеру, пневматические, электрические или аккумуляторные дрели со сверловыми насадками.
- Станочным. Операции выполняются на специальных стационарных или более мобильных настольных станках: токарных, расточных, радиальных или вертикальных сверлильных. При применении последних заготовка фиксируется в неподвижном состоянии, а сверло перемещается возвратно-поступательно, одновременно вращаясь. При токарной обработке главное вращательное движение осуществляется деталью, а режущий рабочий инструмент углубляется в неё, двигается поступательно.
Ручные методы применимы для отверстий не более 12 миллиметров в диаметре. При этом твёрдость материала должна быть малой или средней. Если она будет высокой, то физического усилия для продвижения не хватит. Вручную можно сверлить цветные металлы и включающие их сплавы, конструкционные стали, а также полимерные составы (полипропилен, прочие пластики). Если диаметр отверстия должен быть большим, а производительность сверления – высокой, то станочные технологии подходят лучше.
Главный инструмент – сверло. В стандартном исполнении оно имеет две режущие кромки, отличающиеся острыми краями и располагающиеся по спирали. Специальные модели могут иметь другую конфигурацию.
Свёрла бывают трубчатыми, спиральными, перовыми, центровочными, ружейными, пушечными, шнековыми, кольцевыми, эжекторными, однокромочными, оснащаемыми внутренними каналами для подачи смазочно-охлаждающих жидкостей (СОЖ) и для отвода стружки. Возможные диаметры сверлильных рабочих инструментов – от 0,15 мм до 25 см.
Самый распространённый вид – спиральный. Диапазон диаметров большой, поэтому можно формировать широкие отверстия, но в таком случае операции проводятся в несколько заходов с последовательной заменой инструментов на более толстые. Если нужно просверлить очень глубокое отверстие, то подойдёт либо кольцевое сверло с сохранением стержня высверливаемого материала, либо ружейное, имеющее каналы для отведения образующейся стружки и опцию внутренней подачи СОЖ.
Во многих источниках понятия сверления и рассверливания разделяются. Первое предполагает создание нового отверстия, его первичное просверливание. А рассверливание – это либо получение необходимой геометрии, либо расширение диаметра.
Рассверливание не следует применять в заготовках, произведённых штамповкой, ковкой или литьём. Это обусловлено неоднородной твёрдостью внутренних поверхностей. Сверло с большой вероятностью будет смещаться из-за неравномерности ложащейся на его ось нагрузки. Кроме того, возможны поломки инструмента из-за окалины внутри литой детали или внутреннего концентрированного напряжения в штампованной или кованой заготовке.
Сверление позволяет добиваться высокой точности формируемых диаметральных размеров, относящейся к 11-12 квалитетам. Погрешности геометрии при этом составляют не более 40 мкм (0,04 мм) при диаметрах до 5 см. Степень шероховатости Ra обычно не выходит за пределы значений от 6,3 до 12-12,5 мкм.
Зенкерование
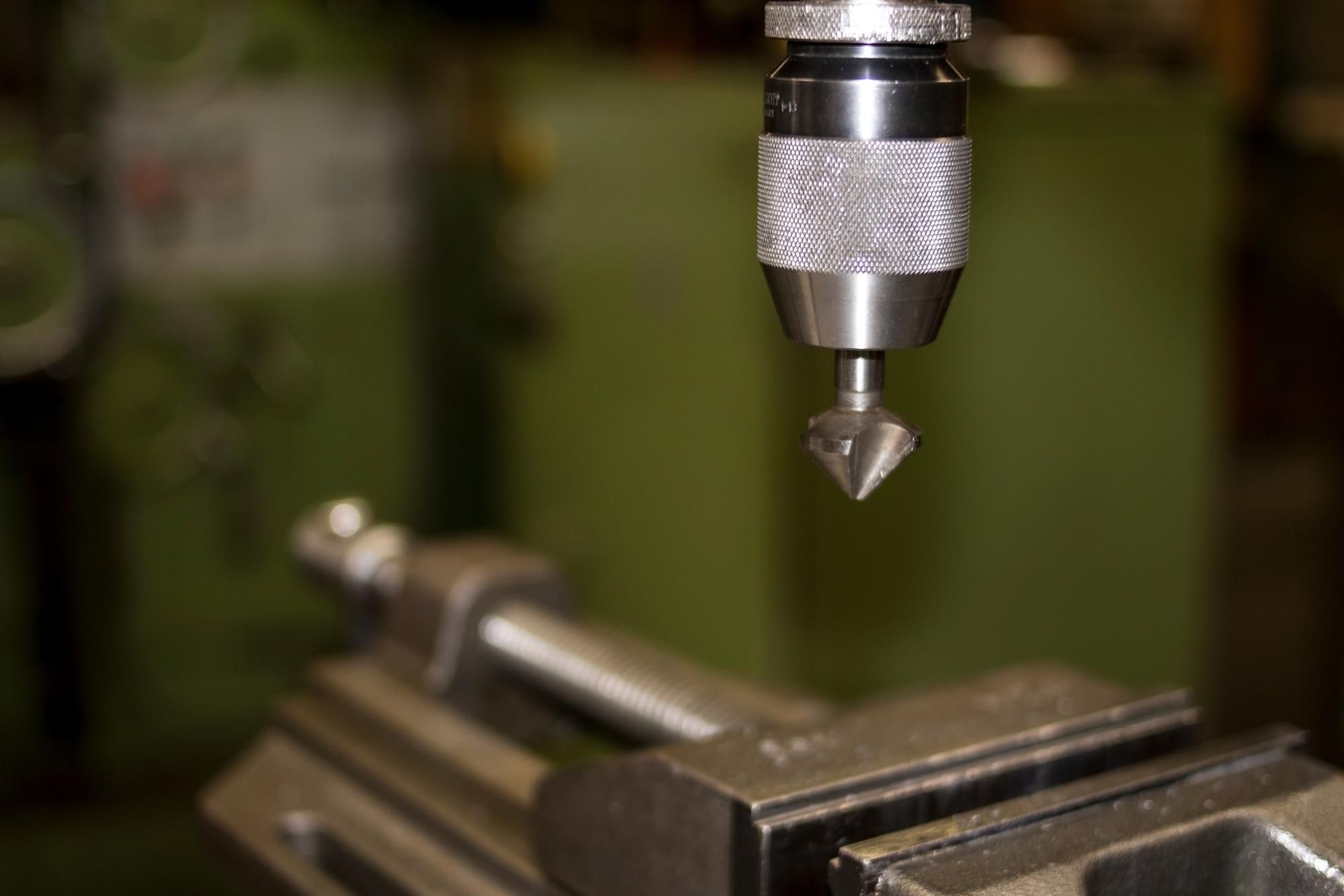
Для зенкерования применяют зенкеры. Эти многолезвийные рабочие элементы также оснащаются режущими кромками, но в количестве от трёх. Главное назначение – черновая либо получистовая обработка, проводимая для улучшения качества или расширения цилиндрического или конического отверстия в кованом, литом, штампованном или выполненном по иной технологии изделии. Другие возможные функции – доведение геометрии до заданных параметров с погрешностью не более 15-50 мкм, снижение шероховатости до показателя Ra 1,25-5 мкм, достижение точности (в некоторых случаях до 8 квалитета, но обычно до 10-12).
Зенкер может быть насадным или цельным. Последний состоит из стержня и рабочей головки. Насадной представляет собой насадку, фиксируемую на вращающемся шпинделе станка.
Зенкеры устанавливаются в сверлильные станки: компактные настольные (если диаметр отверстий малый, а их глубина небольшая) или стационарные для более широких и глубоких отверстий в крупногабаритных заготовках. Ручная зенкеровка не осуществляется, так как она не позволяет поддерживать необходимую точность.
Зенкерование следует выполнять с соблюдением некоторых рекомендаций:
- Желательно проводить операцию сразу после сверления и на том же оборудовании, но со сменой рабочего инструмента.
- Если зенкеруется грубое отверстие в корпусном изделии, то последнее должно быть надёжно зафиксировано на рабочем столе оборудования.
- Величина припусков определяется по специальным справочным таблицам с учётом диаметров используемых зенкеров.
- Режим должен иметь те же настройки, что и при сверлении зенкеруемого отверстия.
- Важно соблюдать правила безопасности и охраны труда, действующие для работ на слесарно-сверлильных агрегатах.
Зенкование и цекование

Под термином «зенкование» понимается обработка исключительно верхней части созданного ранее отверстия. Это требуется, например, при необходимости снятия фаски с целью повышения эстетичности, а также при формировании углубления для маскировки выступающей головки крепёжной детали.
Зенкование выполняется зенковками с соблюдением нескольких правил:
- Операция проводится в окончательно просверленном отверстии.
- Зенкование выполняется на том же станке (сверлильном) после завершения сверления.
- Скорость вращения шпинделя должна быть небольшой – максимально 100 об/мин. При этом предпочтительна ручная подача инструмента с небольшим давлением.
- При зенковании инструментом цилиндрического типа с цапфой, которая больше отверстия, алгоритм будет таким: сверление отверстия, по диаметру совпадающего с типоразмером цапфы; проведение зенкования; рассверливание до конечного требуемого размера.
Есть ещё один вид обработки – цекование. Его делают, чтобы зачистить поверхность, которая в будущем будет контактировать с головкой болта, с гайкой, стопорным кольцом или шайбой. Станок такой же, инструмент – цековка, устанавливаемая на шпинделе с помощью оправки.
Расточка
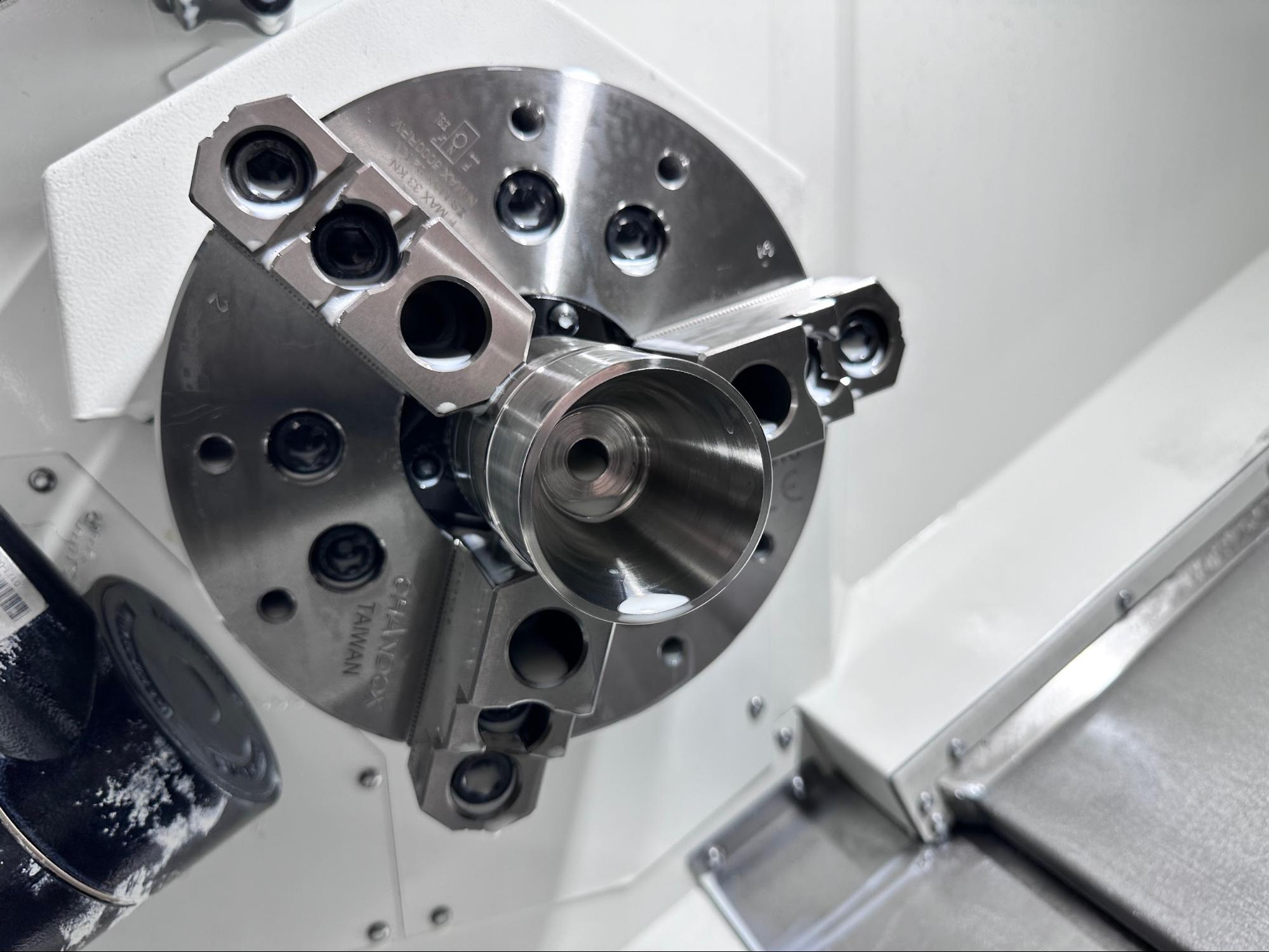
Для расточки подходят фрезерные, узкоспециализированные расточные, токарные универсальные станки. Операции проводятся резцами, различающимися по конструкции. Они могут крепиться в резцедержателе агрегата или в специальном дополнительном держателе.
Движение резки активируется и поддерживается вращением заготовки. А для подачи перемещается рабочий инструмент. Если требуется высокая производительность технологического процесса, а диаметр отверстий превышает 10 см, то для растачивания применяют расточные многолезвийные головки, имеющие пластины из твёрдых сплавов.
Метод обладает стабильностью прямолинейности оси, а также высокой точностью отверстия по отношению к базе. Чистовая расточка позволяет до 12 мкм снижать погрешности диаметров, равных 5-12 см. Шероховатость не выходит за пределы 2,5-5 мкм. Черновая расточка имеет точность геометрии, соответствующую 11-12 квалитетам, а чистовая – 9-10.
Развертывание
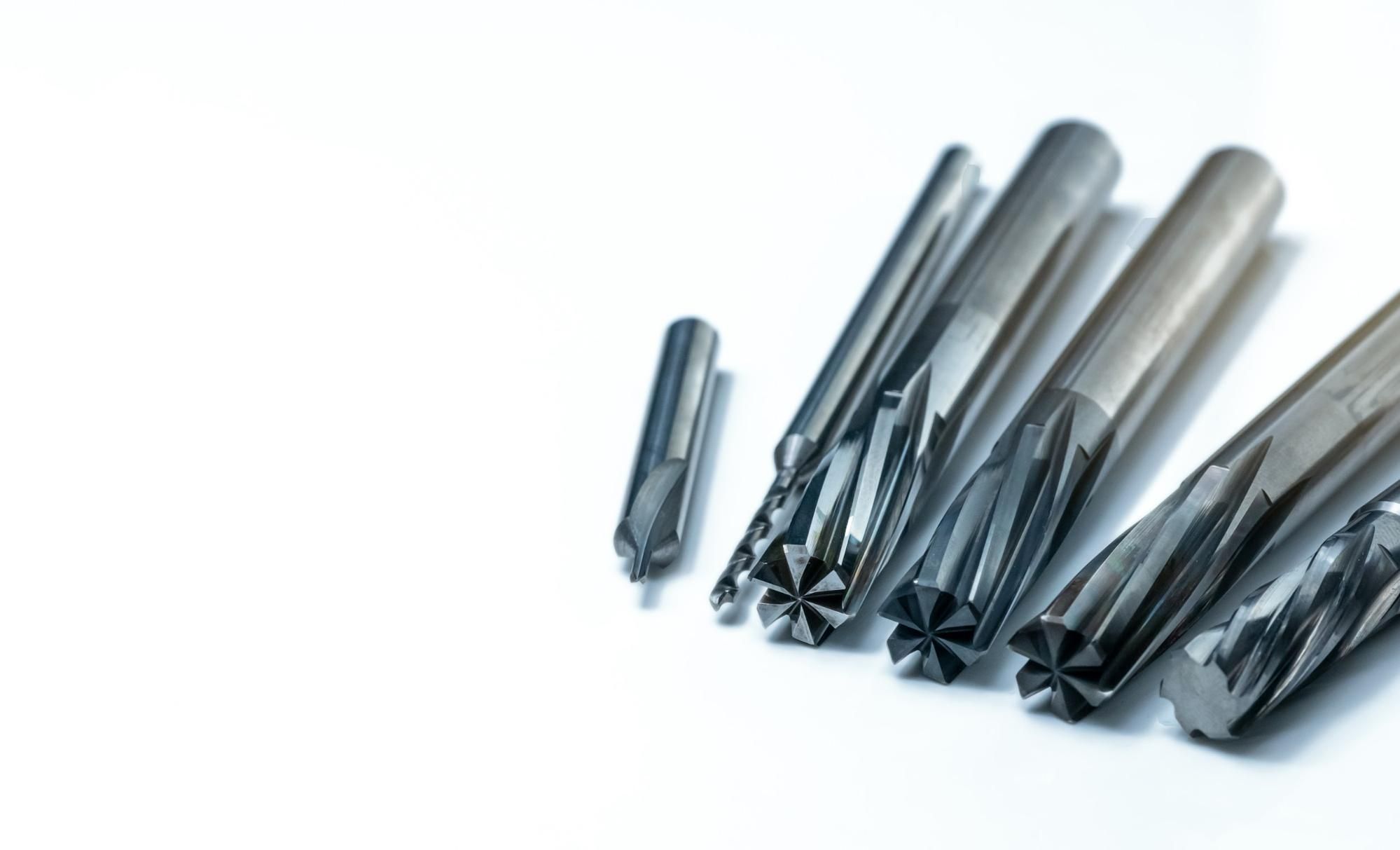
Развёртываются предварительно просверленные отверстия. Для такой операции применяют развёртки из быстрорежущих сталей или твёрдых сплавов: машинные и ручные, чистовые и черновые, насадные и цельные. Инструменты устанавливаются в сверлильные или токарные станки. Степень точности может достигать 6-9 квалитетов. Также достигается незначительная шероховатость – не более 0,63 мкм.
Развёртывание после сверления, расточки или зенкерования выполняют для достижения максимальной гладкости внутренних поверхностей. При этом действуют следующие правила:
- Припуски определяются по справочным таблицам.
- Ручное развёртывание требует вращения в одном направлении – по часовой стрелке. Сначала проводится черновая обработка, затем чистовая.
- Станочное развёртывание проводят сразу после окончания рассверливания на этом же станке.
- Оптимальное положение шпинделя машины – вертикальное.
- Работы со сталью требуют подачи СОЖ. Чугун обрабатывается без таких жидкостей.
- Качество контролируется специальными калибрами.
Скорость развёртывания зависит от твердости материала. Так, для чугуна это 7-20 оборотов в минуту, а для стали – 4-10.
Шлифование
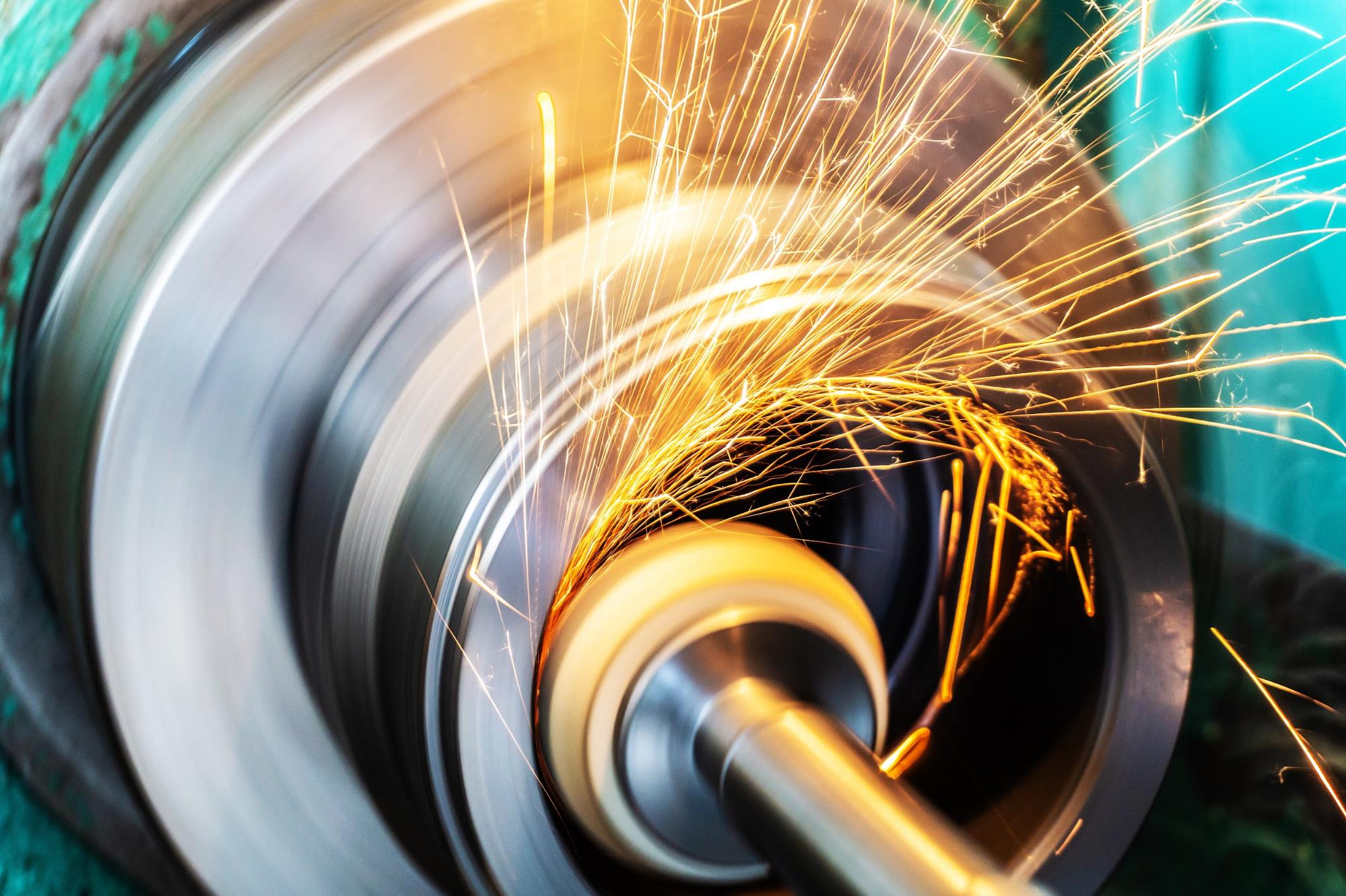
Таким способом заготовки обрабатывают на внутришлифовальных станках (бесцентровых, планетарных и патронных), оснащаемых шлифовальными кругами, вращающимися с определённой скоростью. Но также вращаться может и шлифуемое изделие. Бабка с кругом движется по длине детали с поперечной подачей. Когда инструмент завершает прохождение, цикл повторяется. Подача измеряется в долях ширины шлифовального рабочего круга на один совершаемый изделием оборот.
Шлифование проводится такими способами:
- Врезным. Подача инструмента поперечная, его ширина больше длины шлифуемой поверхности. Обрабатывать можно фасонные поверхности, если круг имеет подходящий профиль. Вариант подходит для массовых, крупносерийных производств.
- Планетарным. Этот метод применим к большим заготовкам, вращать которые невозможно. Шлифовальный круг не только крутится относительно своей оси, но совершает планетарное движение, то есть вращается дополнительно.
- Бесцентровым. Заготовка не закрепляется и вращается. Внешняя поверхность предварительно шлифуется, так как служит технологической базой.
Класс чистоты отшлифованных поверхностей – от 6-го до 10-го. Квалитет точности – пятый или шестой.
Хонингование
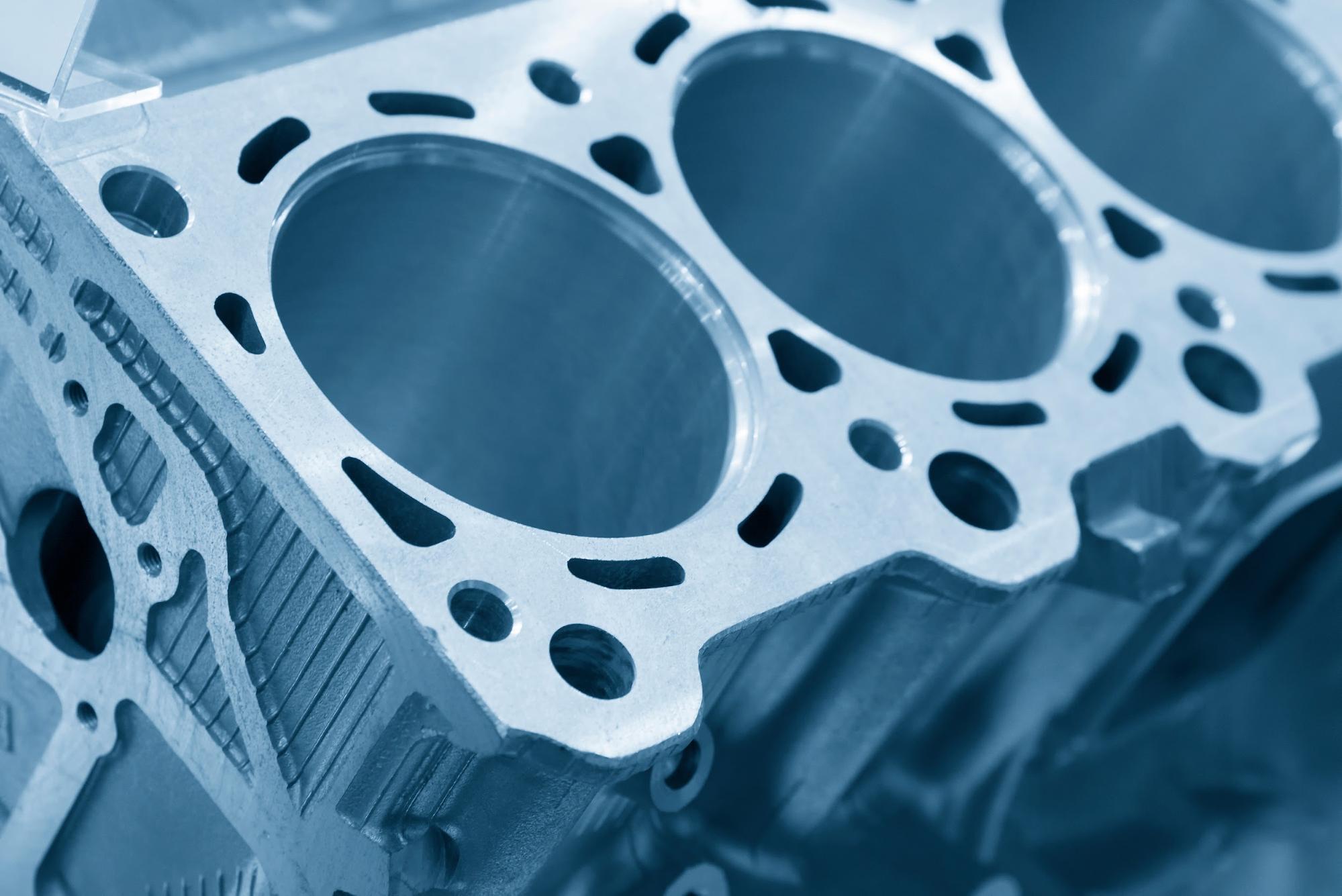
Под хонингованием предполагается финишная обработка цилиндрических сквозных отверстий специальными хонинговальными головками, устанавливаемыми в хонинговальные станки. Инструмент напоминает втулку. В её радиальных пазах зафиксированы бруски с определённой абразивностью. Они вращаются и перемещаются возвратно-поступательно по оси отверстия. Также возможны радиальные движения для оказания давления на поверхности.
Цель операции – получение своеобразной сетки, упорядоченной шероховатой фактуры, которая может удерживать смазочные материалы. Такой обработке могут подвергаться цилиндры, используемые в двигателях внутреннего сгорания. Другие цели – устранение дефектов, например, конусности, седловидности, нежелательной бочкообразной формы.
Хонингование обычно проводят после растачивания, когда достигнуто необходимое расположение оси отверстия. Операция требует интенсивного охлаждения, которое не только не допускает критического нагрева материалов, но и вымывает остатки остающихся на поверхности мелких частиц абразива.
Протягивание
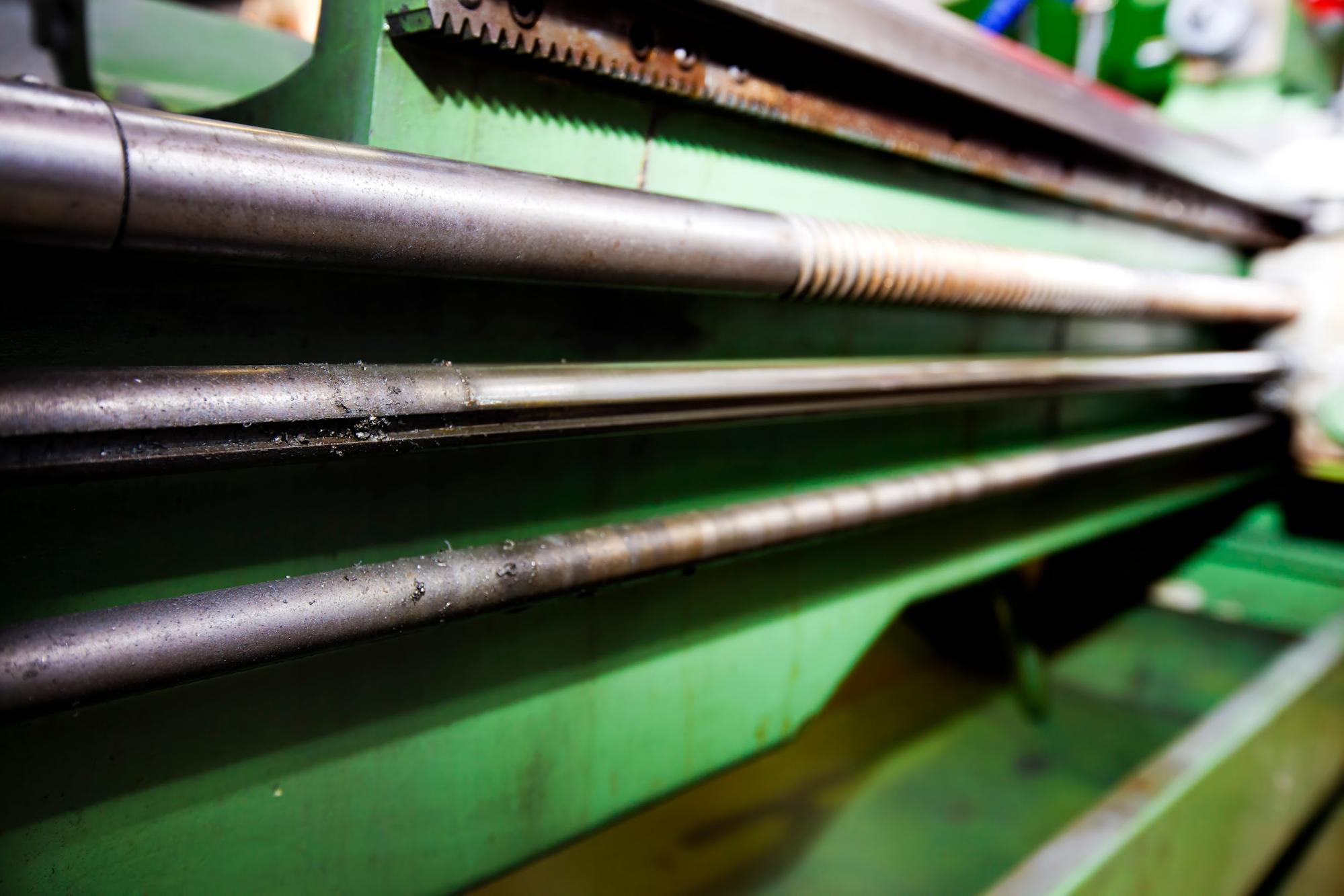
Это чистовая обработка специальными протяжками с зубцами разной высоты, которые перпендикулярно расположены относительно оси рабочих элементов. Каждым зубцом послойно снимается металл. Протяжка движется по оси заготовки. Достигается доведение до заданных параметров диаметральных размеров и формы. Кроме того, протяжки уплотняют структуру металлов, повышая их износостойкость.
Операции выполняются на протяжных станках, которые бывают вертикальными или горизонтальными, гидравлическими или механическими, одно- или многошпиндельными. Агрегаты производительные, имеют несложную конструкцию.
Какой метод обработки отверстий лучше выбрать
При выборе метода учитываются такие факторы:
- Точность, желаемое конечное качество обработки.
- Физико-химические свойства материала, его толщина.
- Особенности заготовки: форма, габариты.
- Характеристики отверстия: вид, расположение в изделии, геометрия, глубина, допустимая степень шероховатости.
- Объём партии – количество обрабатываемых деталей.
- Срочность выполнения работ.
Подобрать оптимальный способ могут только профессионалы.
Заключение
Специалисты компании Profbau оперативно, профессионально и недорого обрабатывают отверстия в различных заготовках и деталях, включая прецизионные, к которым предъявляются строгие требования точности.
Мы работаем на современном оборудовании, соблюдаем технологии, учитываем характеристики материалов и добиваемся максимальной точности геометрии и габаритов, полного соответствия продукции требованиям заказчиков, актуальным стандартам. Связаться с нами можно по телефону, лично в офисе, в мессенджере или по электронной почте.