Твёрдость металла – одна из важных характеристик. Она влияет на выбор подходящих методов металлообработки, на возможность изготовления изделий с определёнными свойствами. Узнайте, в чём и какими способами измеряется твёрдость, а также зачем её выяснять.
Что такое твердость металла
Твёрдость любого металла является его способностью при механическом воздействии более твёрдого предмета противостоять пластическим и упругим деформациям, а также разрушению поверхностного слоя. Иными словами, это возможность сохранять целостность и форму при контактах с телами, обладающими более значительной твёрдостью.
В чем измеряется и как обозначается твердость
Единой шкалы рассматриваемой физической величины нет, поэтому в международной системе единиц (СИ) она не учтена. Есть разные методики с определёнными специфическими мерами.
В качестве основной единицы измерения чаще всего используют обозначение кгс/мм2. Расшифровывается это так: килограмм-сила на квадратный миллиметр. Единица характеризует силу, измеряемую в килограммах и прикладываемую к зоне площади, равной 1 мм2.
В других методиках для обозначений используют буквы. Первой всегда является английская H, так как твёрдость на этом языке пишется «hardness». А вторая буква указывает на название конкретного метода. Рассмотрим возможные варианты:
- HRA – методика, созданная Роквеллом и предполагающая применение шкалы A.
- HRB – тот же способ, но со шкалой B.
- HRC – тот же метод Роквелла, для которого используется шкала C.
- HB – способ Бринелля, разработанный шведским инженером с данной фамилией.
- HSD – определение характеристики по Шору.
- HV – способ Виккерса.
Для чего измеряется твердость
Данная характеристика напрямую влияет на основные свойства материалов, условия их использования и некоторые процессы. Это:
- Износостойкость. Она характеризует продолжительность периода, в течение которого металл может использоваться без износа, без изменения первоначальных характеристик. Например, чем твёрже материал детали, тем дольше она служит и бесперебойно работает в механизме.
- Допустимость определённых способов металлообработки, например, штамповки, шлифовки, резки, фрезеровки. Некоторые методики применимы только к мягким металлам и их сплавам.
- Сопротивление локальным, направленным высоким нагрузкам. Особенно это важно для подшипников, валов, подвергающихся длительному влиянию трения, центробежной силы.
- Возможность применения металла для разрезания или деформирования других материалов. Так, инструментальная крепкая сталь подходит для производства режущих элементов типа ножей, фрез, свёрл.
Зачем определяют твёрдость? Для проверки долговечности, прочности, износостойкости и надёжности детали или многокомпонентной конструкции, изготовленной из оцениваемого металла.
Замеры выполняют для входного контроля качества сырья, для оценки готовой продукции. Твердомеры применяют в разных отраслях промышленности: энергетике, машино-, станко-, судо- и автомобилестроении, в металлургии, строительстве.
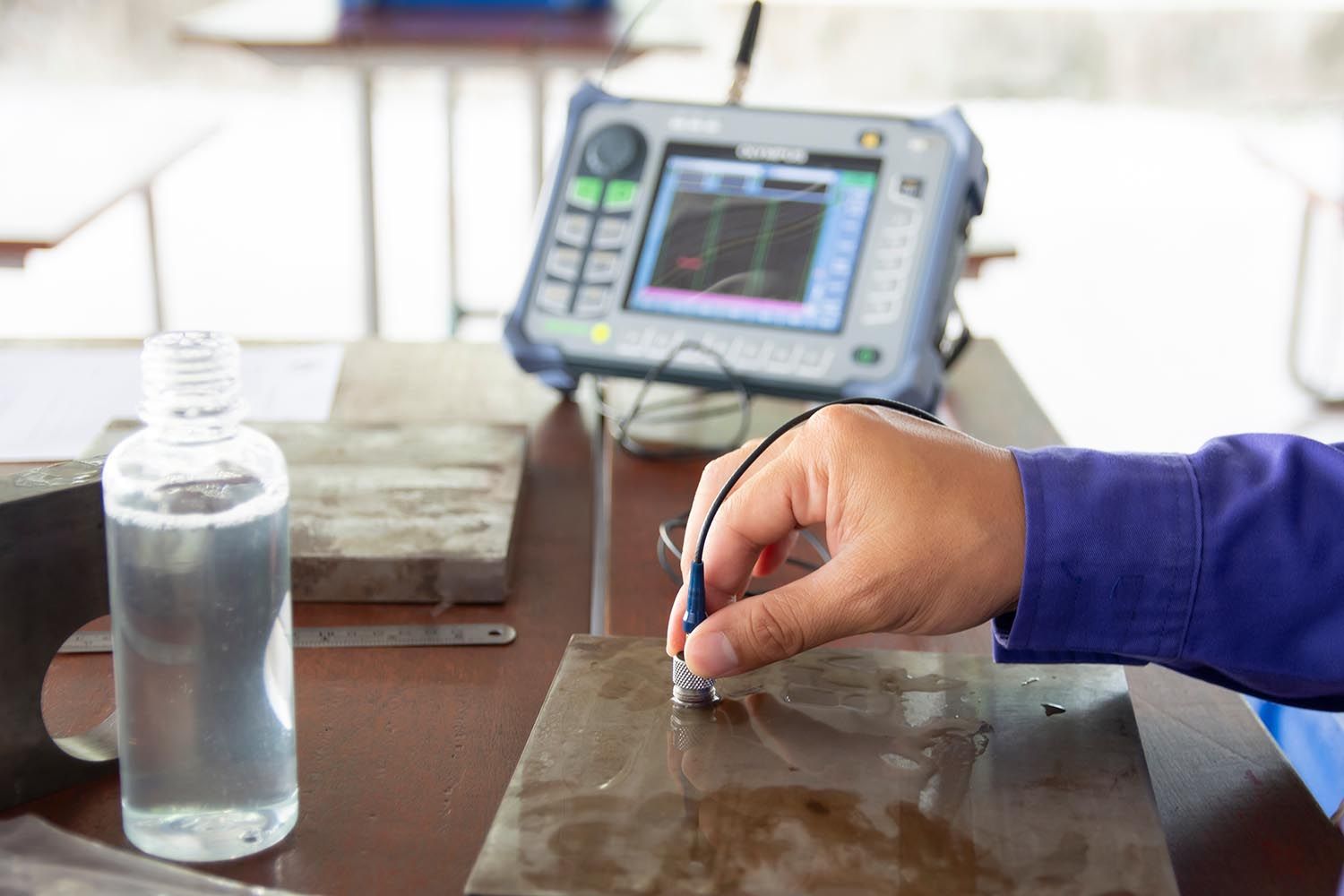
От чего зависит характеристика
От чего твёрдость металла зависит? От его структурного строения, а именно от того, каким образом взаимно располагаются и как связываются друг с другом атомы, входящие в кристаллическую решётку. Решётки металлов различаются по размерам и конфигурациям, и именно они определяют структуру материалов.
На твёрдость сплавов влияет их элементный состав, то есть комбинация химических элементов, из которых материал изготовлен. Например, чёрная сталь, состоящая преимущественно из железа с добавлением углерода, мягче нержавеющей стали, в которой есть титан, никель и хром. Эти элементы по отдельности твёрже углерода и железа, поэтому часто используются в качестве легирующих добавок.
На то, насколько твёрдым получится сплав, влияет способ его изготовления и соблюдение технологии. Чем состав более однородный, тем он качественнее и твёрже. Если концентрации элементов в разных частях неодинаковые, сплав будет менее стойким к деформациям.
Также твёрдость зависит от методики финишной обработки, применённой при производстве. Характеристику улучшает термообработка (закалка), лазерное воздействие с наплавлением упрочняющего поверхностного слоя, цементация с внедрением углерода.
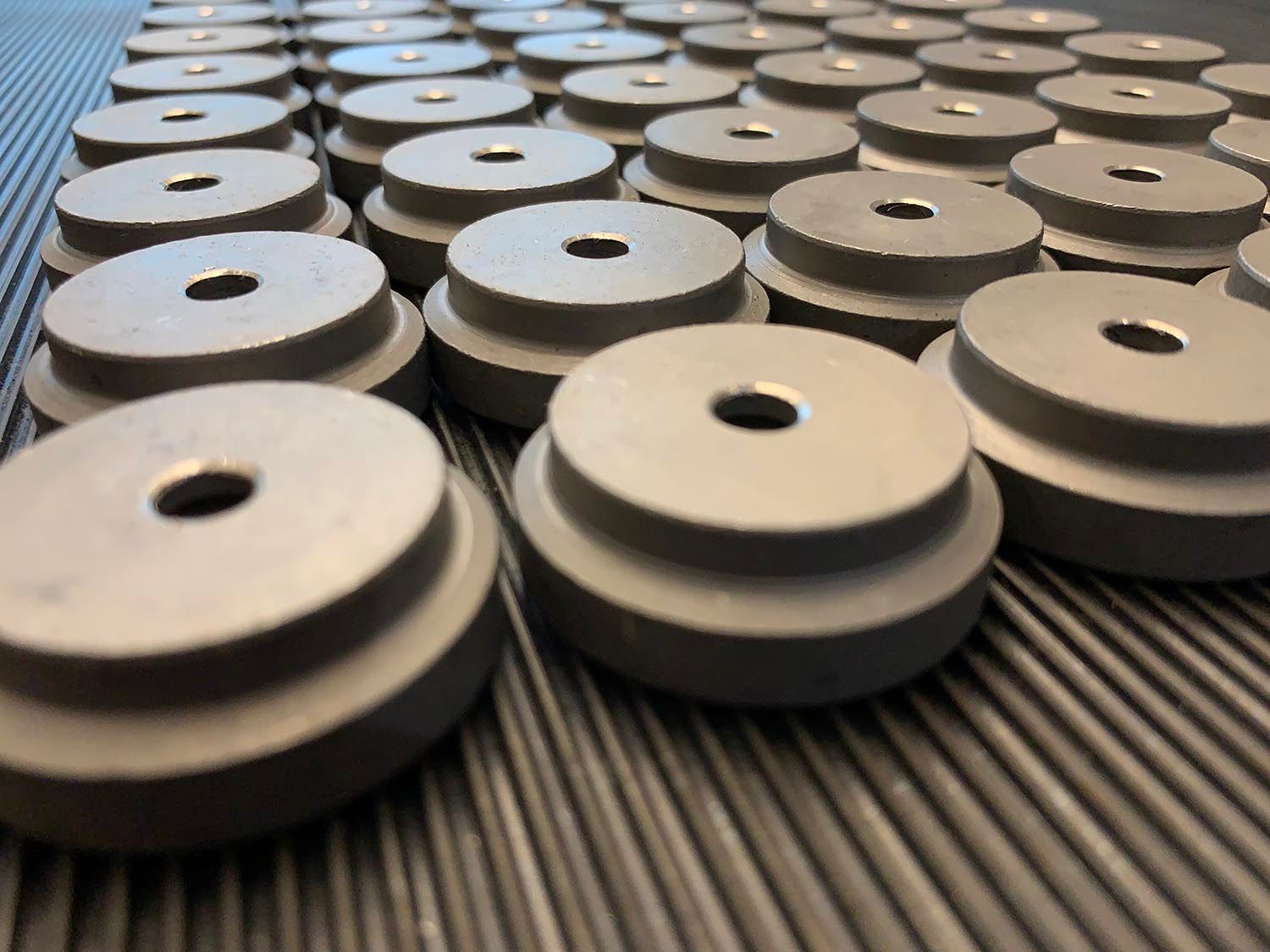
Методы определения твердости металла
Есть разные методики, на которых основывается измерение твёрдости металла. Все они условно делятся на три типа:
- Вдавливание. Это внедрение в испытуемый образец твёрдого тела, называемого индентором. Функцию последнего может выполнять пирамидка, конус или маленький шар. После вдавливания проверяют размер оставленного отпечатка – диаметр сферического углубления после воздействия шарика или глубину впадины, сформированной вершиной пирамиды или конуса. Значение определяется отношением известной величины нагрузки к площади оставшегося следа. Самые распространённые методики данного типа – Роквелла, Виккерса, Бринелля. Другие, менее известные – приспособления ПМТ-2 Хрущева-Берковича, способ Мартеля, моноторон Шора.
- Царапание. Если после проведения по поверхности остаётся царапина, это значит, что испытуемый материал мягче воздействовавшего на него тела. Наконечник, который может быть гипсовым, корундовым или алмазным, имеет заданную и известную твёрдость. Царапание предполагают методы Мооса, приборы Хенкенса и Мартенса, напильник Барба, микрохарактеризатор Бирбаума, устройства ПМТ-3 Берковича и Хрущева.
- Упругий отскок. Для определения твёрдости он применяется редко. Обычно на оцениваемую металлическую поверхность с известной высоты летит в свободном падении боек. Из-за отдачи он отскакивает и подпрыгивает на определённое расстояние.
Ниже рассмотрим самые популярные методы.
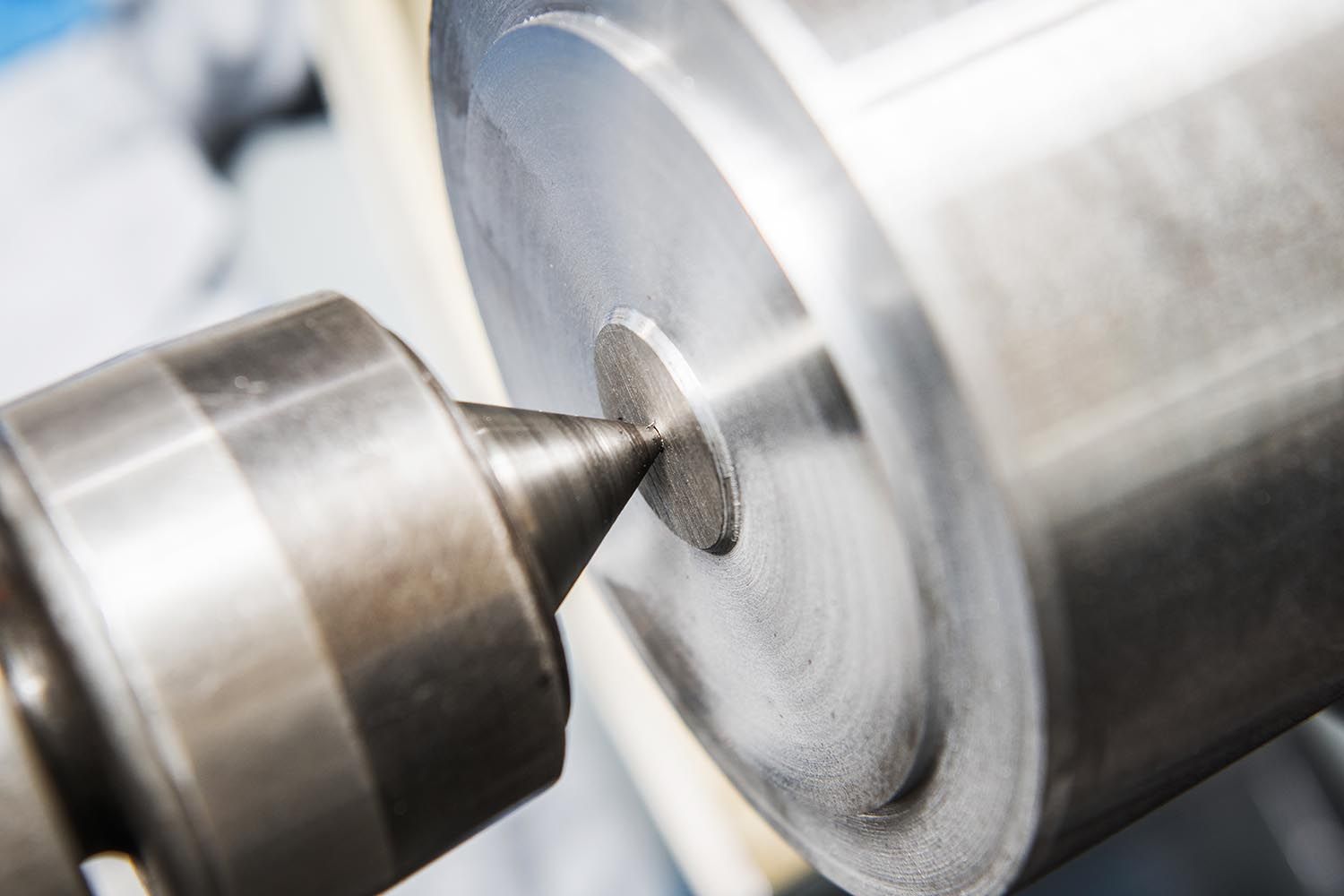
Измерение по Бринеллю
Этот метод был создан инженером и металлургом из Швеции Юханом Августом Бринеллем. Суть заключается в статических нагрузках, воздействующих на образцы. Измеряют твёрдость с помощью стенда, задающего силу, равную минимум 30 килоньютонам (кН). Инденторы – твердосплавные небольшие сферы, диаметр которых составляет всего 1/16 дюйма.
Инструкция:
- Образец фиксируется на основании стенда.
- Сверху выставляется шарик.
- На индентор с небольшой скоростью опускается головка пресса.
- Материал выдерживается под нагрузкой, равной 450 HB или 650, в течение периода от 10 минут до 15.
- После снятия нагрузки исследуется сформировавшийся отпечаток. Оцениваются его диаметр и полученная форма.
- По выясненным параметрам и специальной формуле выявляется искомый параметр.
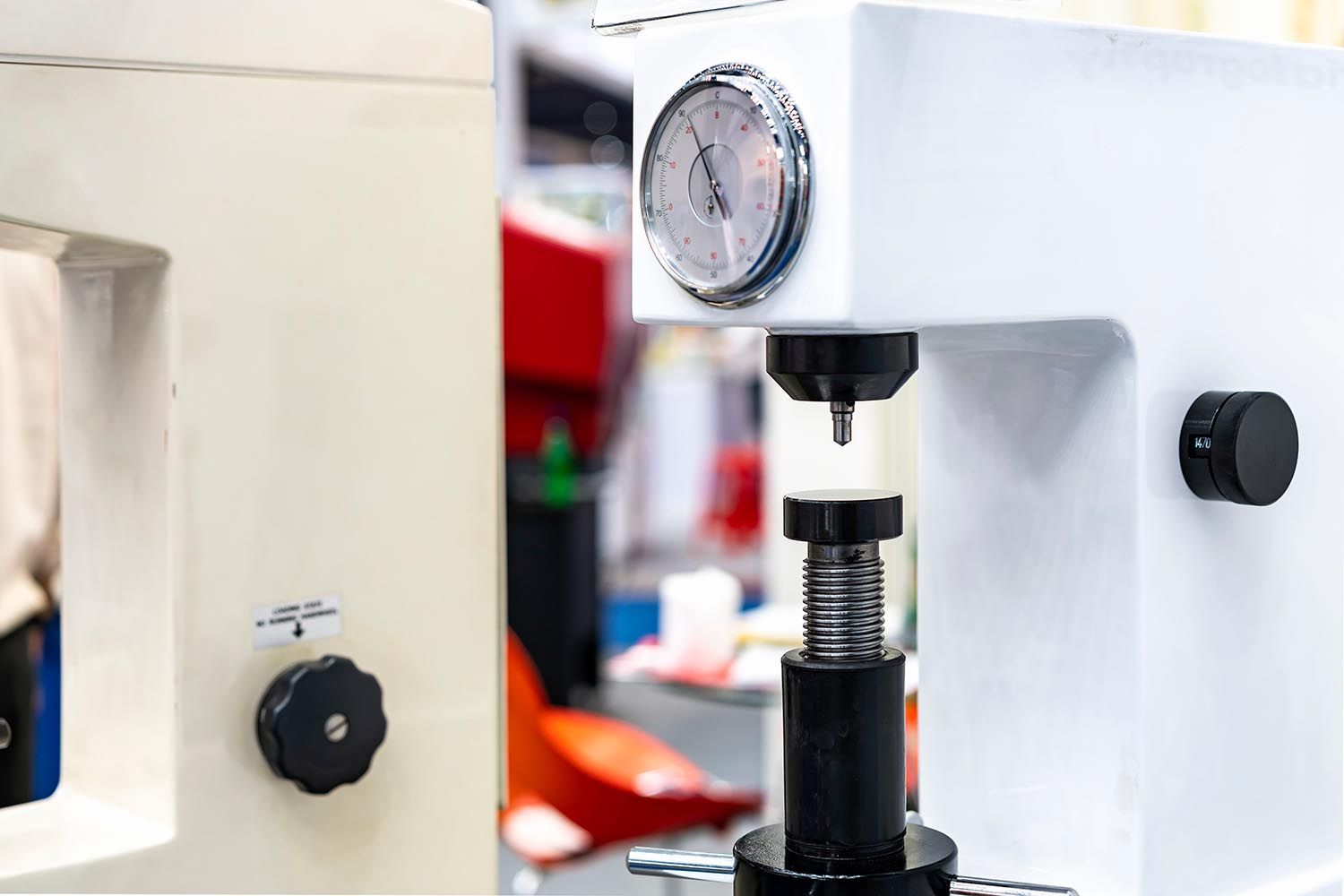
Твердость по Роквеллу
Стэнли и Хью Роквеллы доработали и усовершенствовали теорию «Die Kegelprobe». Это испытание конусом, идея которого возникла у учёного из Австрии Людвига и была обнародована в 1908 году.
Роквеллы создали твердомер, быстро измерявший заготовки при производстве подшипников из стали. Индентор – наконечник-конус, имеющий скруглённую под углом 120 градусов головку, или же шарик, сделанный из карбида вольфрама либо стали инструментального типа.
При испытаниях действуют нагрузки, составляющие 60 килограмм-сил, 100 либо 120 кгс. Получаемые данные фиксируются в таблице, в которой предусмотрено одиннадцать шкал, обозначаемых буквами латинского алфавита от A до T (наиболее востребованные – первые три). Далее проводятся вычисления по формуле. Но в современных твердомерах предусмотрен цифровой дисплей, на котором отображаются результаты.
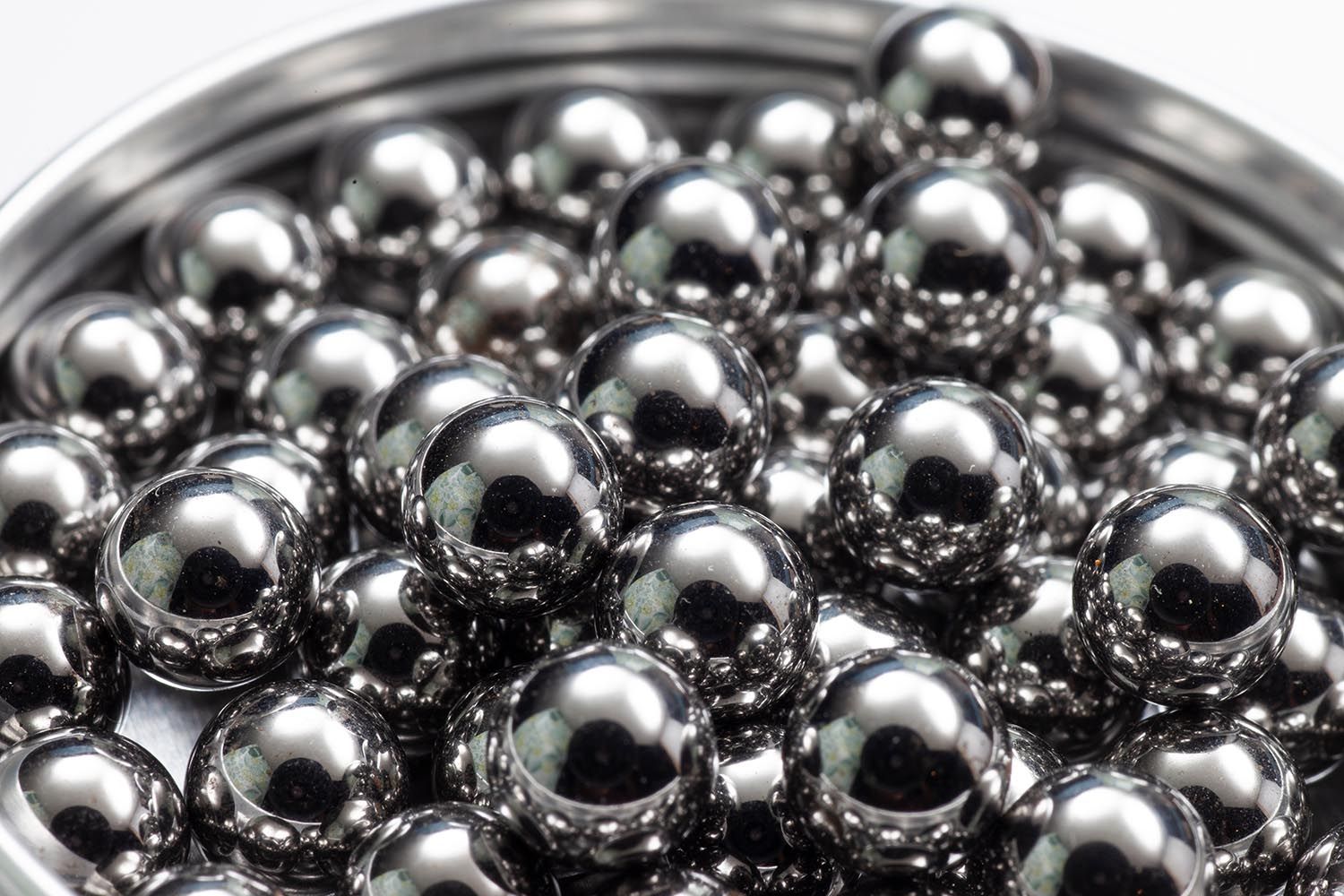
Метод Виккерса
Именно способ Виккерса практикуют в России, согласно действующему ГОСТ. Испытания проводят пирамидками. Они выполняются из алмаза, а их грани сходятся под углом, равным 136 градусам. Испытание короткое, длится 10-15 секунд, но не менее 5. Вариант подходит для разных заготовок и материалов: тонкостенных, различных сталей (цементированных, термически обработанных, азотированных).
Способ Шора
Альбертом Фердинандом Шором выведен способ отскока, для которого разработано специализированное устройство – дюрометр. Под прямым углом на металлическую поверхность с установленной заранее высоты падает твердосплавный стержень со сферическим концом или шарик. По расстоянию, на которое отскочил индентор, выясняют твёрдость.
В конструкцию измерительного прибора входят опора (её площадь – минимально 100 квадратных сантиметров), индикаторная шкала, индентор и задающая его требующееся ускорение пружина. Результаты оцениваются по двум шкалам A и D. В высокоточных моделях дюрометров шкал шесть – от A до D, а также O и OO.
Косвенные методы определения твердости металла
Существуют и косвенные методики, практикуемые для анализа твёрдости относительно иных физических свойств. Для испытаний используют динамические и ультразвуковые приборы, а единицей измерения обычно становится общепринятая, например, HSD, HRB, HV, HRA, HB.
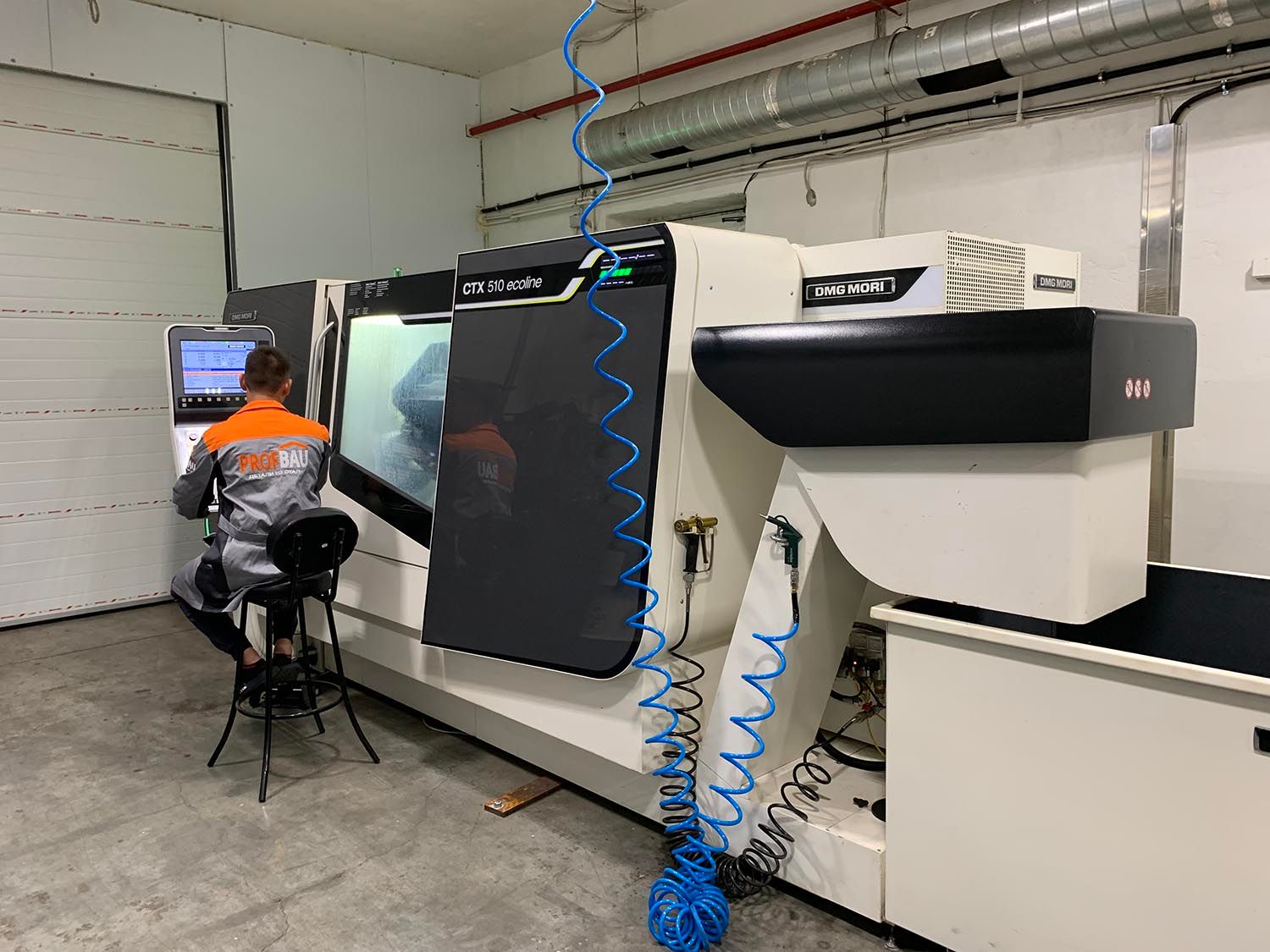
Ультразвуковой метод
Измерительное устройство – ультразвуковой импеданс контактного вида. Он регистрирует частоту колебательных движений внедряемых в изучаемые образцы металлических стержней с алмазными наконечниками. Чем сильнее элемент углубляется в поверхностный слой, тем значительнее степень понижения частоты колебаний.
Такой метод подходит для образцов любых габаритов и веса, для различных сложных деталей: метизов, подшипников, шестерней. Оставляемые отпечатки практически незаметны. Но для крупнозернистых структур бронзы и чугуна вариант не подойдёт.
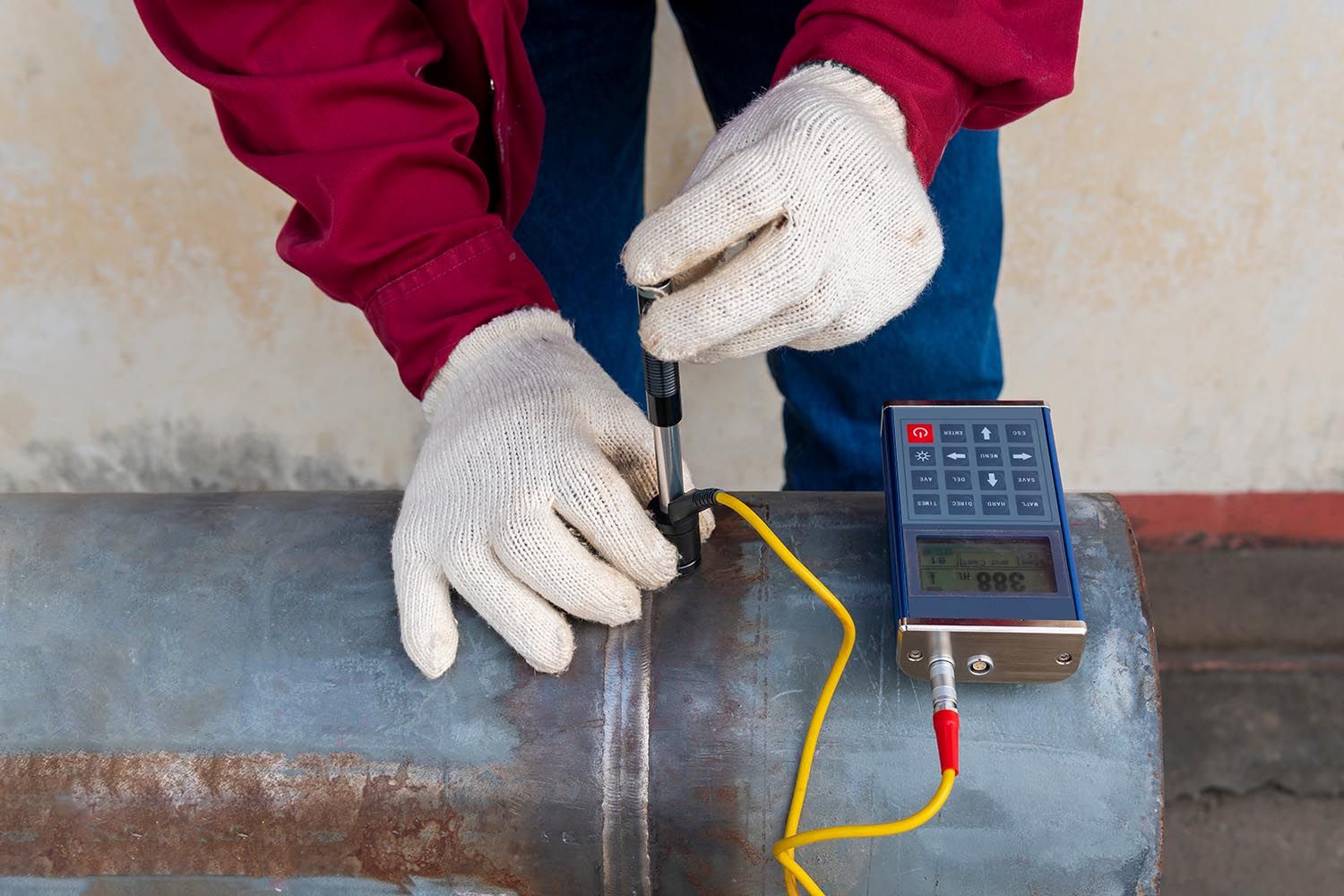
Динамический способ
Он получил название Либа и предполагает определение отношения скорости индентора в момент его отскока от изучаемого образца к скорости движения при ударении о поверхность. Роль бойка играет шарообразный элемент из карбида вольфрама, оснащённый зонами кобальтовой фазы.
Чем более твёрдо вещество, тем ниже значение энергии, расходуемой при соударении на оставление отпечатка, и тем быстрее отскок индентора от поверхности. Динамические измерения применимы к крупногабаритным изделиям, а также к закалённым и упрочнённым материалам, к шероховатым текстурам.
Динамические твердомеры мобильные, несложные в эксплуатации, быстро работают и могут показывать результаты в труднодоступных участках. Но погрешности довольно высоки. Также необходимы периодические калибровки шкал.
Общие правила проведения испытаний и требования, предъявляемые к испытуемым образцам
Действуют следующие правила:
- Образцы следует подготавливать к испытаниям, чтобы уменьшить погрешности. Методы подготовки определяются в зависимости от применяемых методик и нормативно-технических документов. Но обычно поверхность должна быть ровной, очищенной, плоской, без окалины и ржавчины, отполированной и отшлифованной, без следов лакокрасочных покрытий и масел, без царапин и сколов. Допустимая шероховатость Ra – максимально 2,5 мкм.
- Образец должен быть надёжно зафиксирован для сохранения стабильного положения и минимизации рисков смещений от оси прикладываемой нагрузки.
- Перед испытаниями нужно проверять исправность приборов.
- Воздействия не должны быть разрушающими, что достигается благодаря соответствию силы характеристикам материалов.
- Результаты выражаются в конкретных единицах. Нужно соблюдать правильную размерность.
- Толщина металла должна быть минимум в 10 раз больше глубины внедрения индентора.
- Необходимо соблюдение действующих государственных стандартов.
Твёрдость – одна из главных показателей. Её важно знать для выбора технологии производства металлоизделий и подбора оптимальных способов металлообработки. Специалисты компании Profbau перед работами обязательно изучают свойства сырья и заготовок. Это позволяет добиваться высокого качества и полного соответствия техническим требованиям, а также выполнять заказы любой сложности. Обратиться в «Профбау» можно по телефону, электронной почте, в офисе в Москве или на сайте через форму заявки или обратной связи.