Металлы в ходе производственных процессов подвергаются многократной обработке. Одни операции проводятся для придания нужных размеров и конфигурации, а другие улучшают свойства. Например, закалка металла повышает его прочность и делает возможным применение для изготовления изделий, выдерживающих высокие нагрузки. В этой статье расскажем, как получается закаленная сталь и какими свойствами она обладает.
Описание технологии
Закалкой в металлургии называют вид термической обработки, предполагающий нагрев до критических температур, при которых меняется тип решётки. Далее выполняется резкое охлаждение с применением масла, твёрдого теплоносителя, воды, воздуха, жидкого полимера или водяного тумана.
Изменения, происходящие в кристаллической решётке, свойственны только материалам с полиморфизмом. Так называют способность вещества с постоянным химическим составом образовывать разные кристаллические структуры при влиянии внешних факторов, например, давления, температурного режима.
Что происходит с закаляемым металлом? Он за счёт структурных изменений под воздействием высокой температуры (обычно 800-900℃) становится твёрже. Но при этом его хрупкость увеличивается, а вязкость снижается.
Чтобы сделать материал менее хрупким и более пластичным, после закаливания, если при нём произошло полиморфное превращение, выполняют отпуск. При нём сплав или чистый металл сначала нагревается до средневысоких температур от 150 до 650℃, а затем остывает, но медленно. Если не было полиморфного превращения, то следующим этапом становится старение. Оно проводится при нахождении в обычных условиях или при температурном режиме от 50 до 150 градусов. Также старение может быть механическим, протекающим при пластической деформации.
Факт! При закалке в структуре полиморфных материалов формируется мартенсит. Это концентрирующийся в альфа-железе твёрдый перенасыщенный углеродный раствор, названный в честь учёного из Германии Адольфа Мартенса.
Зачем нужна закалка стали?
Для чего, с какой целью нужно проводить закалку? Она позволяет добиваться:
Закалённые металлы становятся более твёрдыми, прочными, долговечными, износостойкими. За счёт упрочнения можно уменьшать вес изделий, так как для достижения нужных параметров толщина твёрдого материала может быть меньше.
Рассматриваемую термообработку применяют к разным изделиям, которые должны сохранять первоначальную прочность и твёрдость. Прежде всего, это режущие инструменты: мечи, оснастка некоторых станков (резцы, фрезы, свёрла), ножи. Широко используют закалённую продукцию и в промышленности, особенно в механизмах, работающих с критическими нагрузками. В такие узлы внедряются прошедшие закалку подшипники, шестерни, колёса.
Какие металлы подлежат калению
Технология применима не ко всем материалам. Закалять можно стекло, а также различные чистые металлы и их сплавы. Но реакции могут быть разными. Если одни материалы упрочняются, то другие, наоборот, становятся мягче и пластичнее.
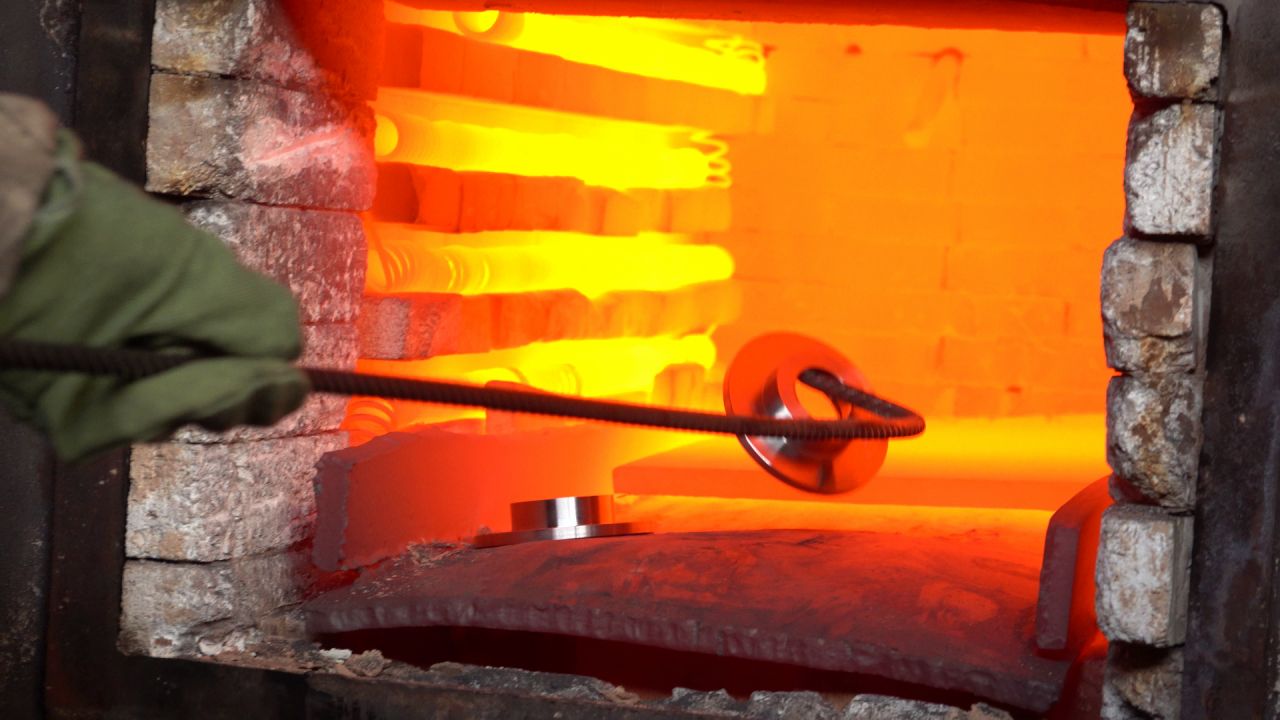
Калить возможно:
Для каждой группы, для каждой марки требуются определённые условия. Температуры, время термообработки и период охлаждения – всё это оптимизируется под конкретные материалы. При этом нужно учитывать их состав, начальные свойства и исходные желаемые характеристики.
Свойства стали после закалки
При нагреве состав, конфигурация компонентов кристаллической решётки и структура сталей претерпевают некоторые изменения. Достигая температуры 723 градуса, сплав ещё остаётся твёрдым, но в нём уже распадается карбид железа, называемый цементитом. Также в гамма-железе образуется равномерный углеродный твёрдый раствор. Его название – аустенит. И такое состояние с точки зрения последующей закалки считается исходным.
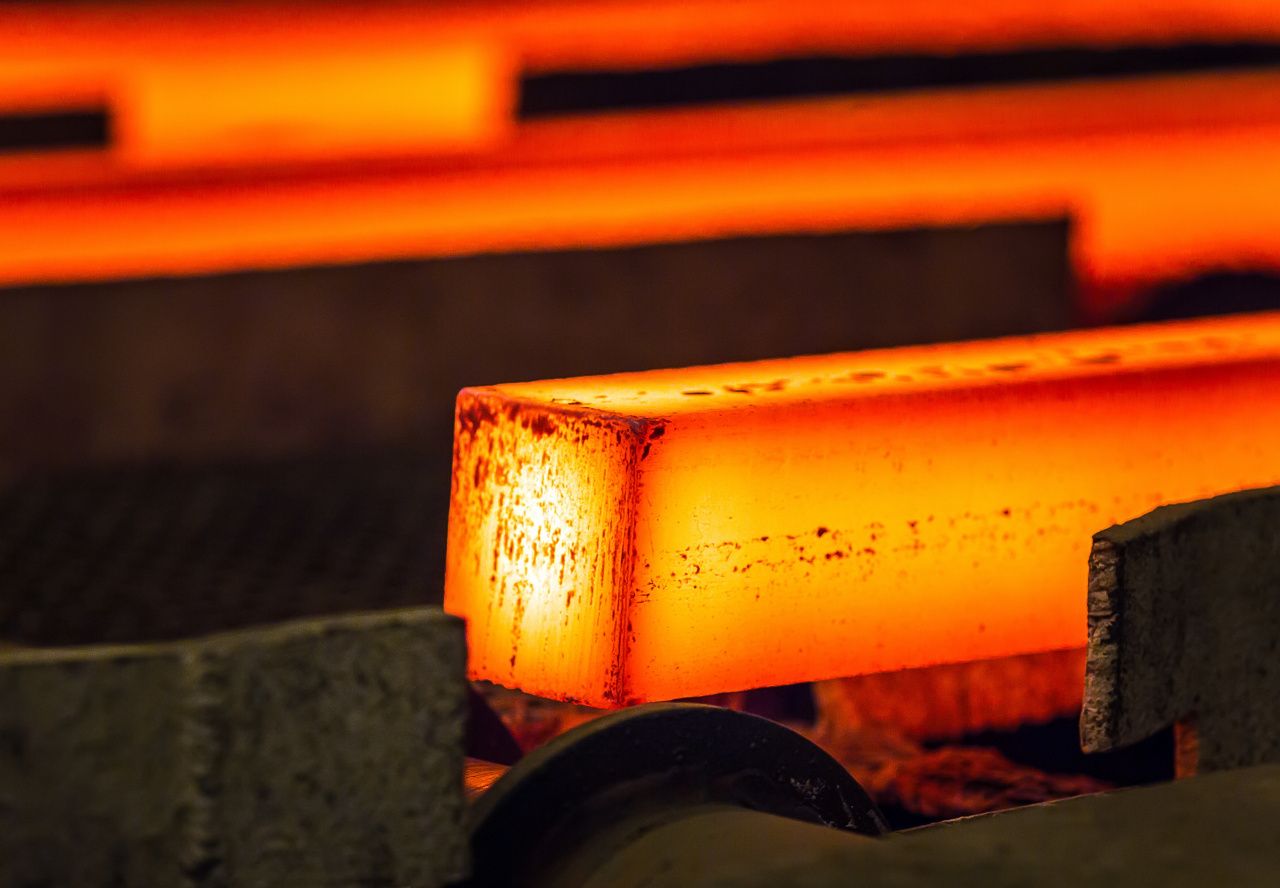
Когда сталь медленно охлаждается, аустенит подвергается распаду, в результате чего металл обретает своё прежнее состояние. Но если охлаждение происходит быстро, то изменения просто не успевают произойти. Формируется кристаллическая решётка с особой структурой. При закалке главную роль играют такие фазовые состояния, как сорбит, перлит, троостит и мартенсит.
Наиболее твёрдой является сталь, достигшая мартенситной фазы. Из таких сплавов получаются качественные режущие инструменты, а также детали, на которые воздействует значительная сила трения: обоймы, втулки, шестерни, валы. При закаливании до троостита достигается комбинация упругости и твёрдости. Такие свойства должны быть присущими пружинам, рессорам, амортизаторам, некоторым видам ударного инструмента.
Чтобы сталь стала износостойкой, оптимально вязкой и упругой, её закаляют до сорбитного состояния. Это необходимо для изготовления элементов конструкций, функционирующих при длительных или непрерывных динамических нагрузках. К ним относятся рельсы. Рассмотренные фазы характерны для всех углеродистых сталей. Но каждой отдельной марке свойственны определённые скоростные режимы охлаждения и температурные значения.
Рассмотрим свойства сталей, изменяющиеся после закалки:
Перечисленные свойства возможно «настраивать», корректно подбирая температуры, виды и последовательность этапов обработки, скорость охлаждения. Например, хрупкость и твёрдость балансируются посредством отпуска.
Способы закалки металла
Есть разные методы закаливания. Они классифицируются по источникам термического воздействия, а также по способам охлаждения.
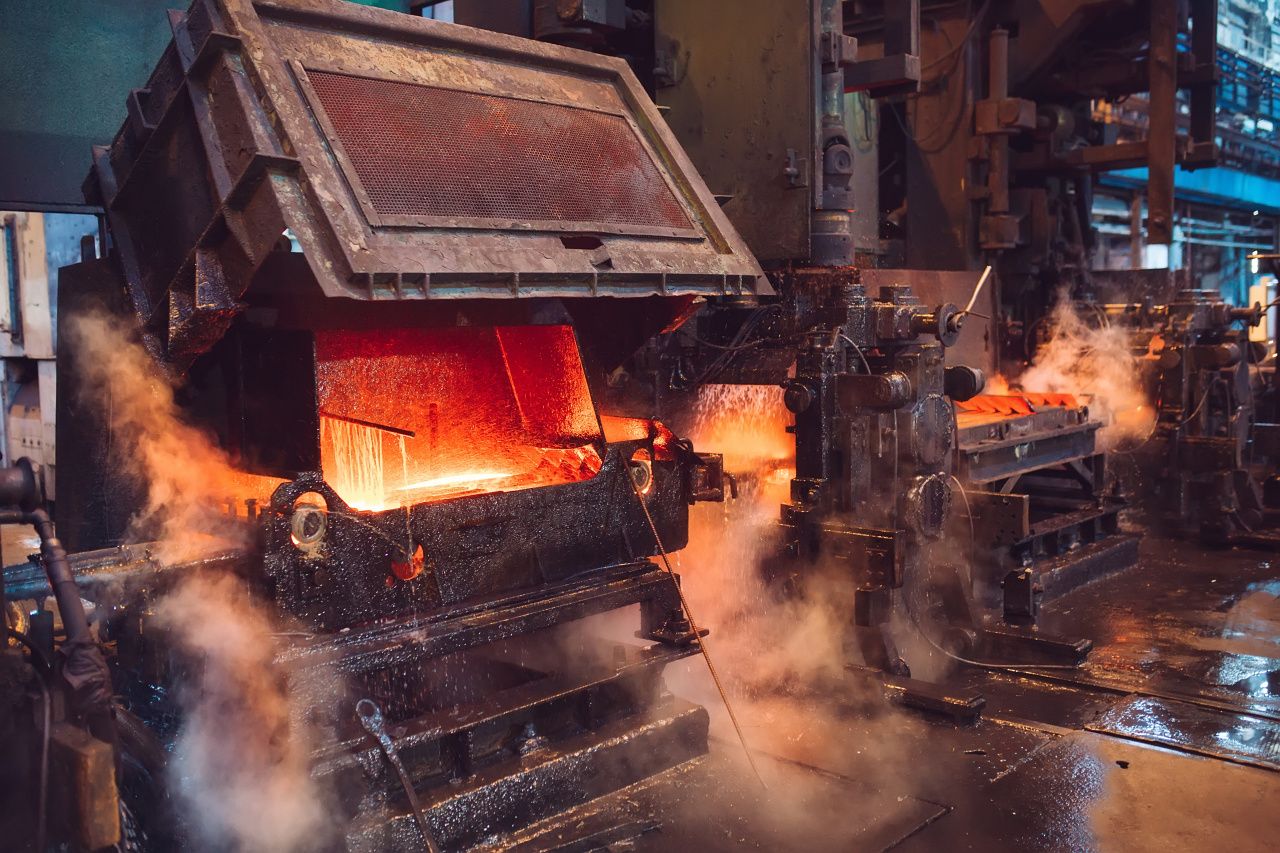
Основными источниками нагревания являются:
Также все способы различаются по видам охлаждающих сред. Ещё один критерий классификации – это циклы рабочих операций и их комплексы. Например, иногда в технологические процессы обязательно входит отпуск. Но для изотермических технологий такой этап не требуется.
Закалка в одной среде
При таком способе охлаждение осуществляется в одной среде, в которую металл помещается разогретым до нужного состояния. Далее он полностью остывает и, если нужно, проходит другие этапы обработки.
В качестве охлаждающей среды для среднеуглеродистых, нержавеющих и низколегированных сталей применяют воду. А для высоколегированных сплавов подходит минеральное масло или воздух.
Главный минус закаливания в единственной среде – это сохранение в металлах повышенных напряжений. Для их нейтрализации в процесс могут внедряться дополнительные методы термообработки, например, отпуск.
Важно знать! Слишком холодной вода быть недолжна. При погружении в неё произойдёт отделение, отскок водной среды от раскалённой поверхности. Это приведёт к формированию паровой рубашки, что замедлит охлаждение. Чтобы не допустить этого, воду нагревают до температур от 40 градусов до 60.
Ступенчатое закаливание стали
Такая закалка отнимает больше времени, но зато отличается равномерностью и большей эффективностью. Суть заключается в том, что сначала заготовка погружается в среду, в которой температура превышает точку старта формирования мартенсита. Далее температура должна достичь нужных значений по всему объёму изделия, во всех точках его сечения. Затем начинается второй этап, при котором металл охлаждается, но с небольшой скоростью. В это время структура равномерно переходит в мартенситную фазу.
Изотермическое закаливание
В основе такого способа – изотермический процесс распадения аустенита с его превращением в бейнит, который является видом троостита. Такие трансформации происходят при температурных значениях, превышающих точку мартенсита. Охлаждение более медленное и высокотемпературное, что позволяет понижать остаточные напряжения.
Данная технология больше подходит для легированных конструкционных сталей. Они проходят несколько этапов обработки. Сначала заготовка разогревается до необходимой, подобранной по составу материала температуры. Далее происходит высокотемпературное охлаждение: в резервуаре, заполненном селитрой, расплавленной щёлочью или солью. Температура среды при этом составляет от 150 градусов Цельсия до 500 (в зависимости от режима нагрева). В этой ванне изделие остаётся некоторое время. Отпуск после такой закалки не требуется, так как напряжение снимается и без него.
Светлое закаливание стали
Этот вариант подходит для металлоизделий, которые имеют поверхности, подверженные окислению. Чтобы не допустить запуска окислительных реакций, нагревание стали осуществляется в печах с созданием вакуума или в инертных газах, таких как аргон, азот. Охлаждение же требует применения только неокисляющих расплавов или жидких растворов. Светлое закаливание используют, если изделие не будет в дальнейшем шлифоваться или же должно соответствовать требованиям к составу поверхностного слоя, а именно к содержанию в нём углерода.
Закаливание с самоотпуском
Такой способ особенно подходит для ударных рабочих инструментов, в которых должны сочетаться поверхностная твёрдость и внутренняя оптимальная мягкость. Самоотпуск называется именно так, потому что фактически протекает самостоятельно, без внешних воздействий.
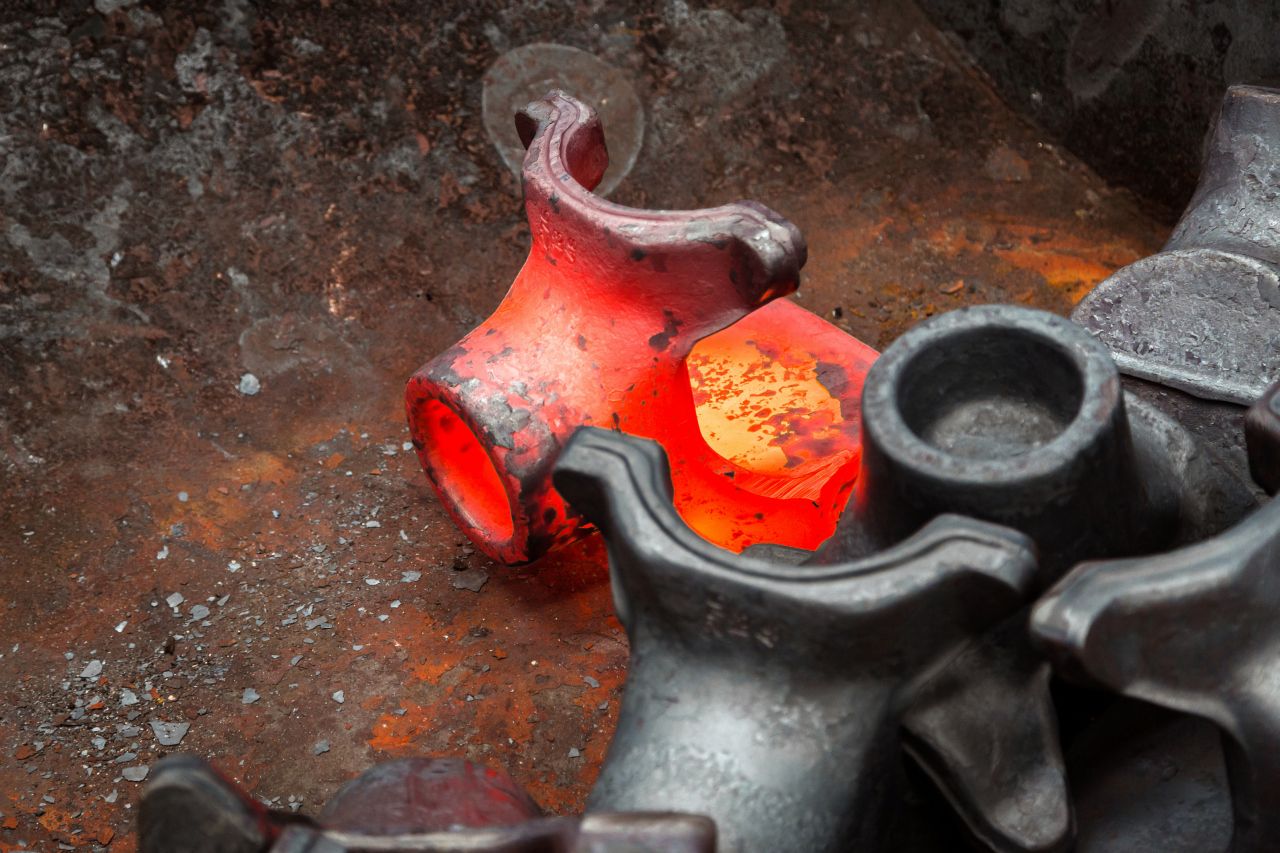
После нагрева деталь погружается в охлаждающую среду, но остаётся там недолго. Благодаря быстрому извлечению сохраняется внутренняя тепловая энергия, которая распространяется по всему объёму и позволяет равномерно доводить материал до температуры отпуска, снимая напряжение.
Закалка с самоотпуском – процесс, требующий достаточных знаний. Он под силу только профессионалам, способным точно рассчитать длительность периода пребывания в охлаждающей среде.
Оборудование для термообработки
Используется оборудование двух типов: нагревательное и охлаждающее. Первое отвечает за термическую обработку, а второе охлаждает нагретые заготовки.
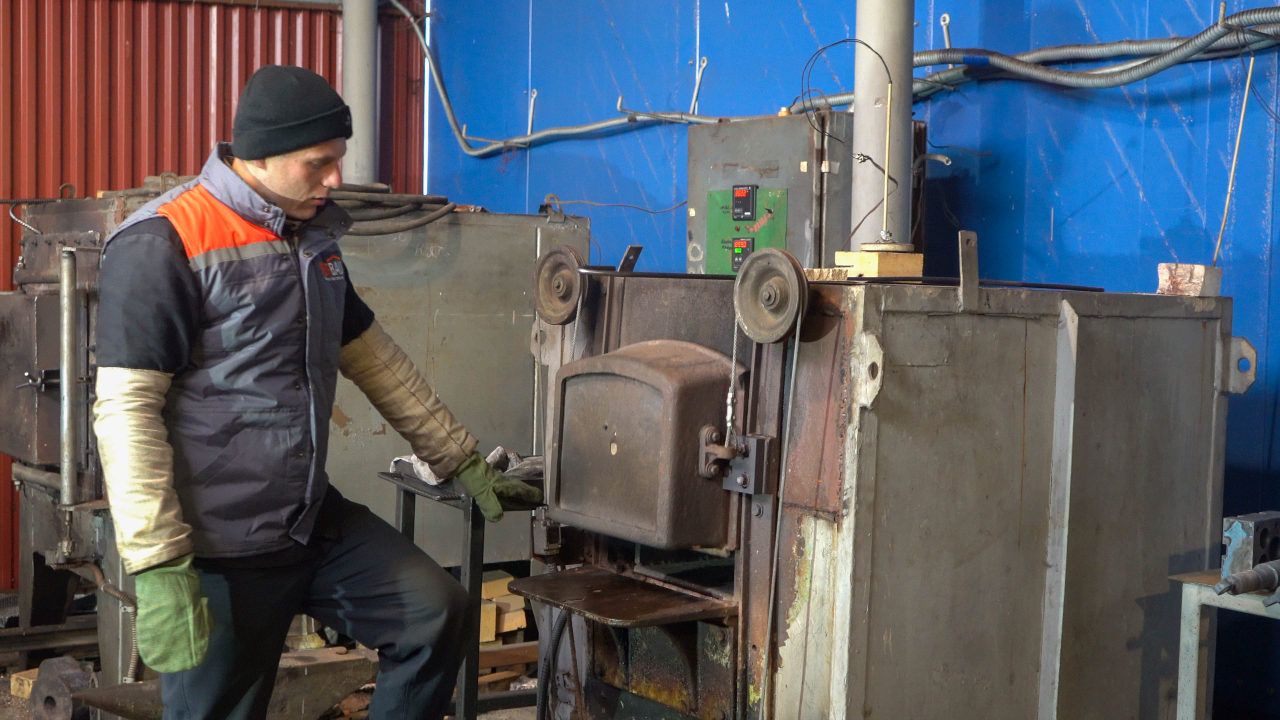
Для нагревания используют такие установки:
Охлаждение осуществляется в закалочных ваннах. Это ёмкости из жаропрочной и термостойкой стали, печи для металлических и соляных расплавов, а также графитовые тигли.
Функции закалочных жидкостей могут выполнять вода, минеральные масла, водополимерные составы, расплавы металлов и солей. Для последних используют олово и свинец, соединения калия, натрия, бария. В закалочных ваннах, работающих с жидкостями, предусмотрены системы нагрева и охлаждения, а также мешалки для перемешивания сред до однородности и для разрушения образующейся паровой рубашки.
Температура для закалки
Нормативные температурные значения устанавливаются в зависимости от состава металлов: содержания в них легирующих компонентов и массовой доли углерода. Чем меньше концентрация углерода, тем более значительные температуры.
Если нагрев недостаточный, то необходимая структура не успевает образовываться, то есть ожидаемый эффект не достигается. Перегрев чреват обезуглероживанием, возрастанием внутреннего напряжения, изменениями величины и форм структурных частей, а также окислительными реакциями в поверхностных слоях. Режимы, применимые к разным маркам сталей, можно найти в справочных таблицах.
Температуры для их контроля анализируются. Для этого используют пирометры бесконтактного и контактного типов. А в последние годы активно применяются инфракрасные измерительные устройства, которые позволяют оценивать температурный режим дистанционно и в любых точках поверхности. Для приблизительного определения температур можно пользоваться таблицами цветовых соответствий.
Методы охлаждения
Технологии охлаждения различны, так как от них зависят конечные характеристики закаливаемых изделий. Выделяют такие методы:
Перечисленные методы могут комбинироваться и применяться последовательно.
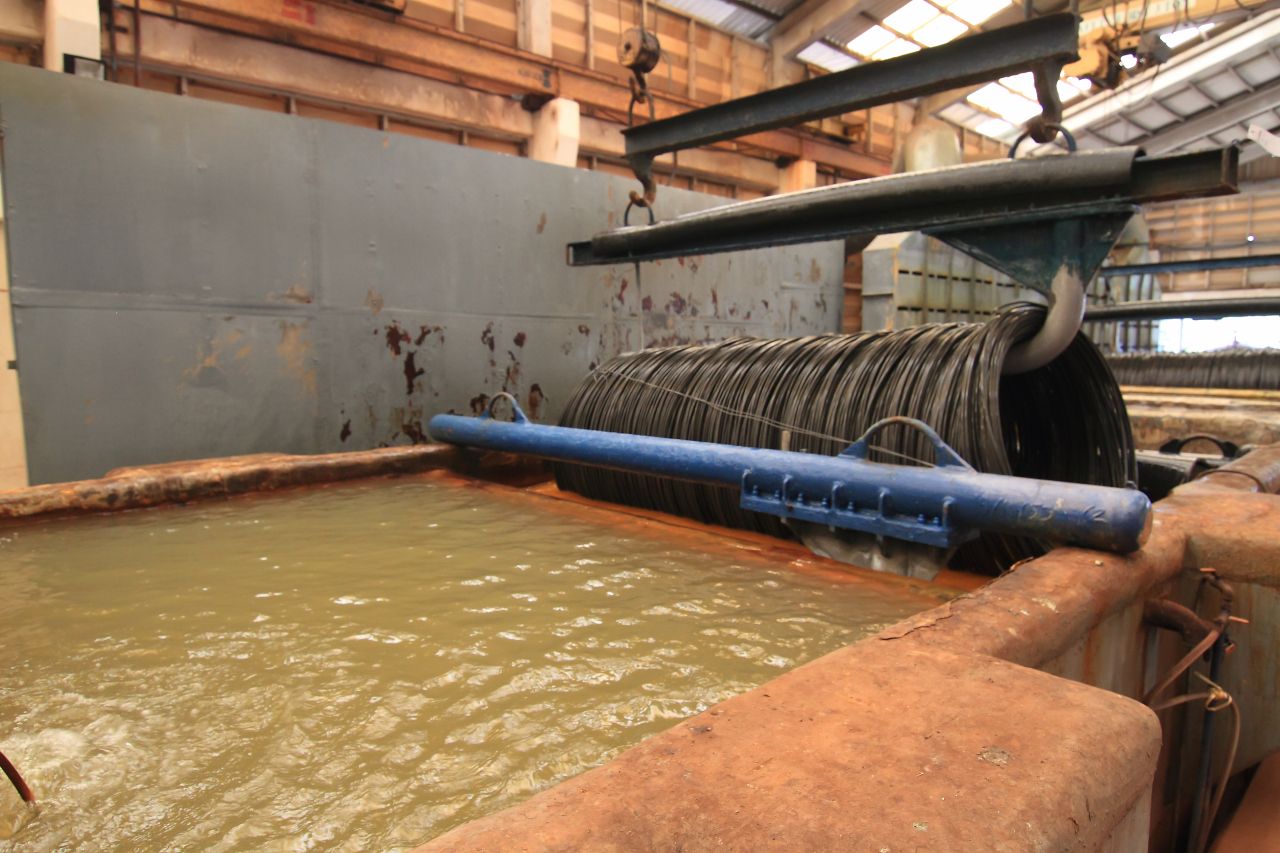
В качестве охлаждающих сред используют:
Чтобы охлаждать металлы правильно и до нужной структуры, среды в некоторых случаях чередуют.
Закалка цветных металлов
Технологии, применимые к цветным металлам, имеют некоторые особенности. Наиболее часто закаливают сплавы с алюминием и медью. Изделия из чистого алюминия подвергаются данной термообработке в редких случаях, так как при производстве деформируемые и литейные сплавы уже проходят все технологические операции, необходимые для повышения твёрдости.
Необходимость закалки алюминия может возникнуть, к примеру, если в участках сварных швов утратилась былая прочность. Для этих целей используют закалочные печи с термодатчиками и температурными регуляторами. Своими силами закалить алюминиевые предметы довольно сложно, так как нужно рассчитать температуры с точностью до 5 градусов, учтя марку и свойства материала. Довольно проблематично и охлаждение. Если оно будет некорректным, деталь может деформироваться.
Закаливание меди также имеет свои нюансы. Так, при нагреве до температур выше 600℃ и последующем быстром охлаждении водой заготовка из-за произошедшего отпуска станет мягкой. Оптимальный режим – не более 400 градусов. Красного каления допускать нельзя. Нагретое медное изделие остужается на воздухе.
Важно! В домашних условиях закалять металлы не только сложно, но ещё и опасно, так как температуры поднимаются высоко, что всегда связано с рисками ожогов. Кроме того, требуется постоянный и точный контроль температур. Для этого подойдёт пирометр: стандартные термометры для измерения столь горячих материалов не применяются.
Возможные дефекты
При нарушении технологии могут возникать дефекты. К ним приводят внешние факторы и такие ошибки, как отклонения от заданных температурных показателей, неоднородное накаливание заготовок, слишком быстрое, неравномерное или медленное охлаждение, а также низкое качество металла, например, большое количество примесей, повреждения.
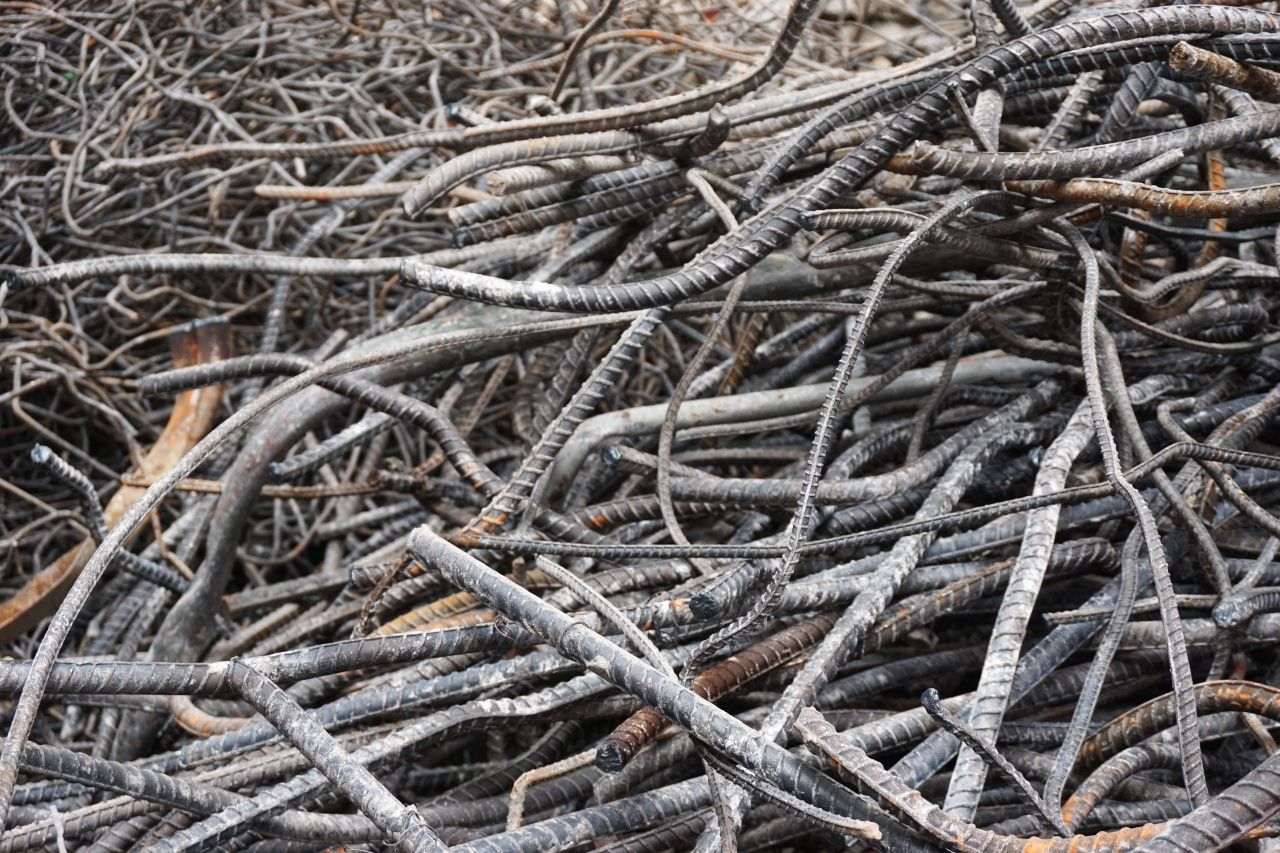
Рассмотрим возможные дефекты и их причины:
Заключение
Закалка – процесс сложный, требующий ответственного подхода, знания особенностей и строгого соблюдения технологии. Чтобы получить желаемый результат, такую операцию следует доверить опытным профессионалам.
Компания Profbau уже много лет успешно занимается производством и металлообработкой. Мы используем современные технологии и автоматизированное оборудование, выполняем заказы любой сложности и любых объёмов, работаем профессионально и оперативно. Хотите узнать подробности и получить качественные изделия? Свяжитесь с нами любым удобным способом.